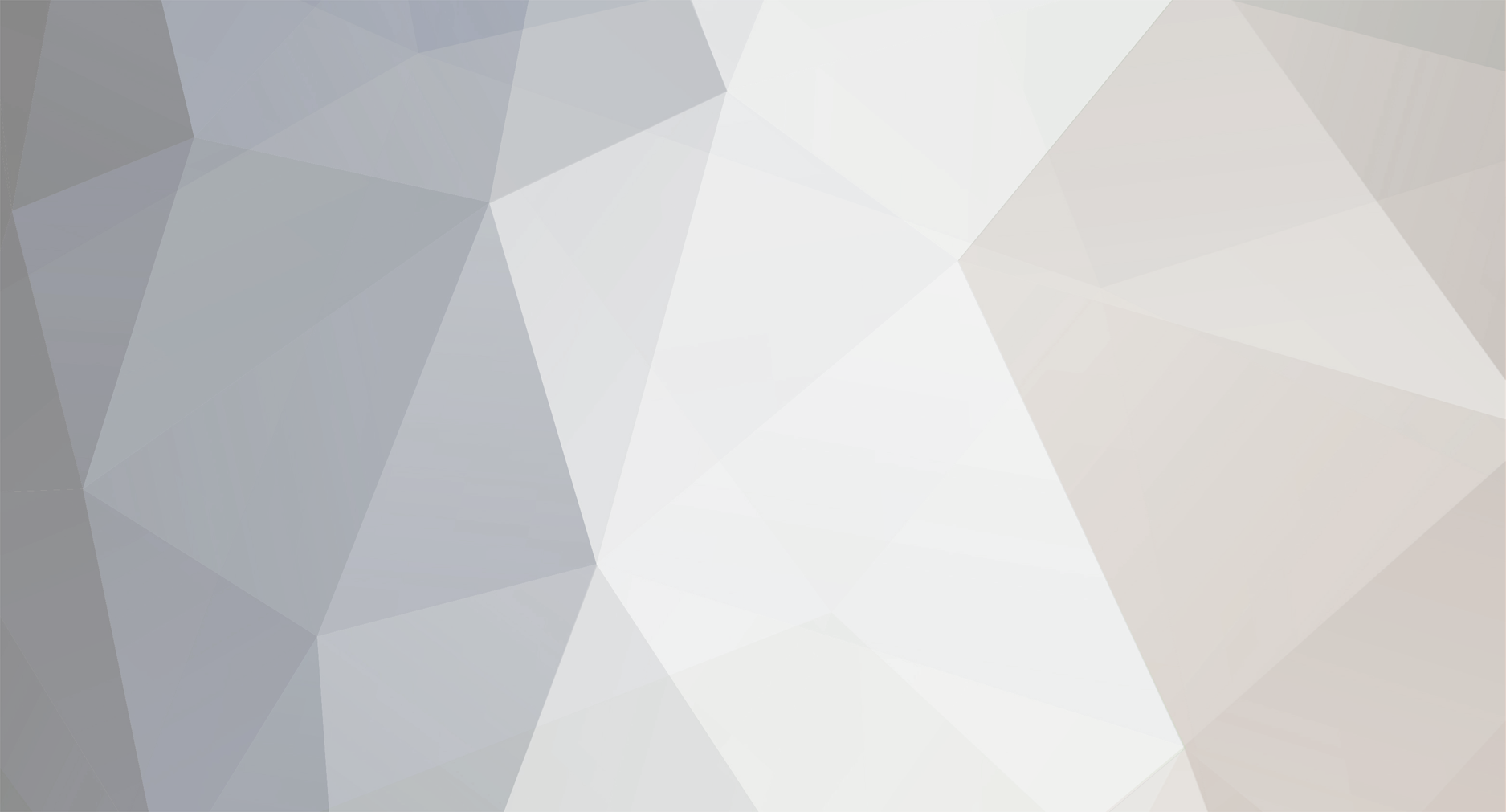
Сан Толич
Участник-
Постов
363 -
Зарегистрирован
-
Посещение
-
Победитель дней
9
Тип контента
Профили
Форумы
Блоги
Загрузки
События
Весь контент Сан Толич
-
Лучше иметь отдельно полуавтомат и аппарат для TIG-сварки. Все равно если для заработка, то TIG нужен с AC/DC. Но если так хочется зависеть лишь от одного аппарата, то можете посмотреть Гроверс комбо. С DC TIG есть Викинг МТМ.
-
Да не пытаюсь я этого делать, и не пытался. И стойкость расходки Опять не в ту степь. На третий круг заходить уже не буду. Толи выразился так, что непонятым остался, толи настройке режима резки так вам поучить хочется, что предмет вопроса отлетел на задворки. Буду литературу добывать да в ней ответ искать. А металлолом как будет в ассортименте, так может и натурными наблюдениями займусь. Мне потенциал источника понять хочется. А на него, как мне видится, три параметра влияют: выходные ток и напряжение и потребляемая мощность, которая на любой из множителей может влиять, если она ниже их произведения. Взять к примеру powermax 105 от гипера. Из его руководства: макс.ток 105 А, номинальное выходное напряжение 160В, коэф.мощности 0.94. Имеем макс.мощность грубо говоря 17,8 кВт, т.к в руководстве о ней не написано, но указанный потребляемый ток в 30А в целом это подтверждает. Теперь берем моего китайца и его руководство: макс.ток 100А, мощность 13 кВт, про остальное ни слова. Если примем, что ток 100А он действительно выдает, а КМ пусть будет таким же (точность не принципиальна), то напряжение на дуге будет 122В. Что говорит о том, что при таком же токе он не порежет как гипер в плане и скорости и максимальной толщины даже с его резаком.
-
Что-то увели в другую сторону. Про режимы резки, качество кромки и прочие сопутствующие результаты речи не было. А замеренное напряжение, которое портал удерживает, это и есть то напряжение, которое может выдать источник при заданной высоте резки. Вот! И там с ростом толщины напряжение дуги растет, потому как длина дуги меняется. Если источник не сможет обеспечить необходимого напряжения на дуге при заданной высоте резки, то этой самой резки не будет. Приложил примеры от гипера, два из них при одной высоте резки. И рассмотрим очень абстрактный пример. Ток 85А, напряжение 146В - мощность 12 410 Вт. Допустим это максимальная мощность источника (КПД источника в счет не берем). Теперь хотим резать на токе 105А. Итого мы можем получить 12 410 / 105 = 118 В, что говорит, если опираться на таблицу гипера, что на этом токе мы ничего толстого нормально не порежем, по крайней мере на тех режимах, что указаны, т.к. источник не сможет растянуть дугу при токе 105А. И мой вопрос как раз о том, есть ли данные по напряжению на плазменной дуге в зависимости от толщины металла, т.к. если источник еще может выдать ток, но уже уперся в свою максимальную мощность и дугу выше не тянет. Или я по своему незнанию силовой электроники и работы инверторных источников заблуждаюсь в своих рассуждениях и вопросах?
-
Резка с ЧПУ, масса на столе. Есть контроллер высоты дуги. На нем выставляется значение напряжения. Для его поддержания контроллер, измеряя напряжение дуги, поднимает/опускает плазмотрон. Т.е. напряжение регулирую как бы я, задавая его величину в контроллеру высоты. Положив лист 4мм на стол, и поставив на ТНС напряжение 100В, я получу нужную мне высоту резки в 1,5мм, поставив напряжение 120В - резак поднимется вверх и высота резки станет гораздо выше и качество реза упадет. Понимать, какую толщину осилит источник. Если источник не растянет дугу на нужную толщину, то он нормально не ее прорежет. Вот об этом и вопрос. Если 100А источник при максимальной мощности на токе 80А растянет дугу сильнее, чем на токе 100А, то вроде как он должен на меньшем токе прорезать лист большей толщины (в пределах разумного конечно, т.к. ток резки здесь тоже важен). Железяк нет в быстром доступе для проверки, так бы может и не спрашивал. Это напряжение дуги при резке. В букваре к гипертерму powermax 105 в таблицах режимов резки эти величины можно повстречать, для тока до 85А там как раз тонкие листы стартуют с рекомендуемого напряжения 120В, а толстые типа 25-30мм - уже 140В.
-
Есть ли у кого-то информация о зависимости напряжения от толщины резки? Суть вопроса в чем: с ростом толщины металла длина дуги увеличивается и, соответственно, растет напряжение. С ростом напряжения получаем рост потребления источником. Максимальная мощность источника ограничена, в связи с чем можно получить одну и ту же потребляемую мощность при меньшем токе, но большем напряжении, или наоборот. Например источник может резать на токе 85 А с напряжением 140 В или на токе 100А с напряжением 120 В, т.е. не сможет растянуть дугу на ту же длину, т.к. не хватит мощности. В первом случае можно порезать большую толщину на малой скорости, а во втором - меньшую толщину на бОльшей скорости. Правильно ли я это себе представляю? Или я заблуждаюсь в оценке потребляемой источником мощности и он вытащит ее из сети сверх того, что указано в технических характеристиках? Возможно я подберу материалы разной толщины, чтобы реальными наблюдениями ответить на свой вопрос, но пока их нет в быстром доступе, задам вопрос знающим людям.
-
Уходящее качество. Засилие клипов, третьесортных статеек в поисковой выдаче, ложное ощущении достаточного качества информации из той самой выдачи ведут ко всему этому. Иногда в чатах такую дичь спрашивают, что даже не знаешь как относиться: с сожалением о том что собеседник "не копенгаген", и что о знании и понимании азов не озаботился, или непублично смеяться над его глупостью, не пытаясь хоть как-то помочь ответом.
-
Я, честно говоря, подумал про "детские наконечники" с резьбой М6, но потом подумал, что наверняка речь про диаметр 1.2, и там такого быть не должно и написал про шкурные интересы снабжения.
-
Да что тут раскрывать. Откатывался снабженец в одной и той же организации, а потом пришел "оптимизатор затрат" и зашел с уровня повыше. Теперь местечковая месть, чтобы как можно дольше сохранить поставщика под аргументом "с его проволокой проблем не было". Но после слов о лояльном, давно берущем проволоку предприятии эту версию можно развернуть в обратную сторону. Пришел кто-то новый с мелкими шкурными интересами и хочет протащить "своего" поставщика. Когда-то, работая на одном немаленьком заводе, я насмотрелся на подобное, но только в части металлорежущего инструмента.
-
шкурный интерес снабженца
-
Тут надо опыт пользователей разных моделей искать, ну и видео от производителей именно на тонком алюминии. Тонкий алюминий в импульсном режиме далеко не каждый полуавтомат позволит сварить. В большинстве обзоров на китайцев весьма толстые пластинки сваривают, а про малые толщины потом всплывает информация, что тяжеловато. Ежели Picomig 225 Puls TKG по зубам, то можно покопаться с пристрастием потратив время на сварку образцов.
-
10-литровый углекислотный баллон, простой редуктор и кислородный рукав тысяч в 6-7 обойдутся, если не в глуши живете, конечно. Вентиль крутить и редуктор на нужный расход настраивать не велика наука. Базис за 15 минут читаешь, а потом с деталями разбираешься по ходу работы. И на оставшиеся 28 (из ваших 35) можно найти Сварога N24002N ну или чего другое (можно и б/у поискать, если можно проверить при покупке). П.с. 10-баллон друг покупал 1,5 месяца назад за ~3200, заправка 300 руб, редуктор простенький 1000 руб, шланг не помню, ну и 5кг катушка проволоки порядка 1000.
-
и те переходники с картинки но многим проще на ПВЗ сходить. Ходил бы автор в сварочный, темы бы этой не было)
-
Адаптер/переходник TIG горелок. Поиском на ура находится. БРС для газа отдельно поискать или переходник еще какой-то сделать. И тогда две горелки легко и непринужденно будут ставиться.
-
Себе недавно 15-летний Неон ВД-160 (2009 г.в.) купил, не смог пройти мимо . Так этот малыш 3мм электроды УОНИ-13/55 на минимальном токе поджигает и тянет (заявлено 30А, клещей для DC нет, чтобы факт 30А подтвердить). Я впечатлен. Как сварщик, я сугубо - любитель, сравнительной базы нет, и количеством сваренного тоже не похвастаю. Но имеющийся дома недорогой китаец МР-3 2мм на токе 20А не тянет, как только зашитый ГС перестает работать.
-
А что мешает еще кандидатов в выбор добавить? Ответ хоть и не по теме вашего вопроса, но в тему выбора.
-
Клиенты разные бывают. Бывают рвачи, которые лишнюю копейку не потратят, но из своего "бизнеса" отжимают все до капли. И оборудование все запущено, и рабочие как оборванцы, зато шеф "красавчик" с рыночными ценами за паршивенький товар, с намерениями постоянно обмануть. А бывают адекватные, которые понимают цену ремонта. И если для первого "А чо так дорого", то второй знает, что через оговоренное время его проблема будет решена. У адекватного мастера цены все-равно плюс/минус от сложности работ зависят, а не от того, насколько сильно можно поиметь клиента в его (клиента) критической ситуации. Да, жизненные ситуации бывают разными, но я про свое восприятие ситуации, не более того.
-
Если длина не 50, а 500 все-таки, то я от 3000 до 5000 бы рассматривал. Все-таки рихтовка и токарка 500мм детали потребуют и времени и опыта.
-
Обратный кабель к столу, изделие на столе. Когда изделие к столу прилипает (ну или само слегка приваривается) после начала сварки, то грандиозного хлопка уже нет. Эту взаимосвязь я увидел. Околошовную зону специально не зачищал. Профтруба в состоянии поставки и без следов коррозии. Хлопает и реже и слабее. Попробую "стерильные" условия для сравнения. Может действительно дело в дисциплине подготовке.
-
Столкнулся с этой проблемой. Аппарат простой: Invermig 350 Compact. Наработка на нем небольшая, ТПН новый, горелка также особо не работала. Соответственно факторы связанные с роликами и горелкой я пока исключаю. Временами при первом касании холодной проволоки хлопает. Откусывание шарика не всегда помогает, в том смысле что нет четкой взаимосвязи. Может ли это быть просто особенностью схемотехники аппарата, с которой просто надо жить дальше? Или надо копать и копать, перебирая все факторы, зависящие от пользователя, и доискиваться до причины?
-
Более чем достаточно для знания о них. Поисковые запросы грамотно составить и смотреть-читать-запоминать. Никто в голову трамбовать информацию не будет. И в конечном счете кому это надо? Искать ответы в первую очередь нужно самостоятельно. А ежели что не понятно, спрашивать у тех кто может знать ответ. Самообразование именно это и подразумевает.
-
Контролер, проводящий ВИК их видит. Полезно почитать хотя бы про дефекты сварных соединений, чтобы понимать, чего не должно быть в швах. Это и есть сварка под рентген и УЗК. По методам контроля информации на уровне ГОСТ и всякий стандартов организаций хватает, да и здесь на форуме можно найти. Вас то на алгебру кидает, то на металлургию, сейчас вот на контроль занесло. Найдите уже учебное заведение, да поучитесь. Иначе так и будет разрозненная не систематизированная информация.
-
Теорию вероятности в общем и принцип нормального распределения в частности, чтобы понимать, насколько швы стабильны в повторяемости, а их качество удовлетворяет документации. Где повезет, а где действительно сможешь А так тема - дичь какая-то, и ее бы предать забвению, чтобы столько полезный ресурс "глубиной" таких вопросов не захламлять. Или реальность становится такой дикой?
-
Надо понять к чему стремиться в этом деле: или сварщик или технолог (и т.п.) по сварке. Первому важно понимать рабочую документацию и уметь делать швы согласно ней. Тем более если корневые швы и сдача НАКС интересуют. А второму важно знать, допускать ли первого до сварки, иными словами делать (или проверять) для него документацию. Первый должен из 10 одинаковых соединений все 10 выполнить одинаково (точнее очень сильно похожими друг на друга), а второй должен эти швы спроектировать и/или проконтролировать, чтобы оценить на пригодность для конструкции. Поэтому если вы хотите "буст" до сварщика, то упор нужен не на металлургию и материаловедение, а на технологию выполнения работ.
-
или не хотят по всей видимости
-
В маркетинг Электроинтел не вкладывается.