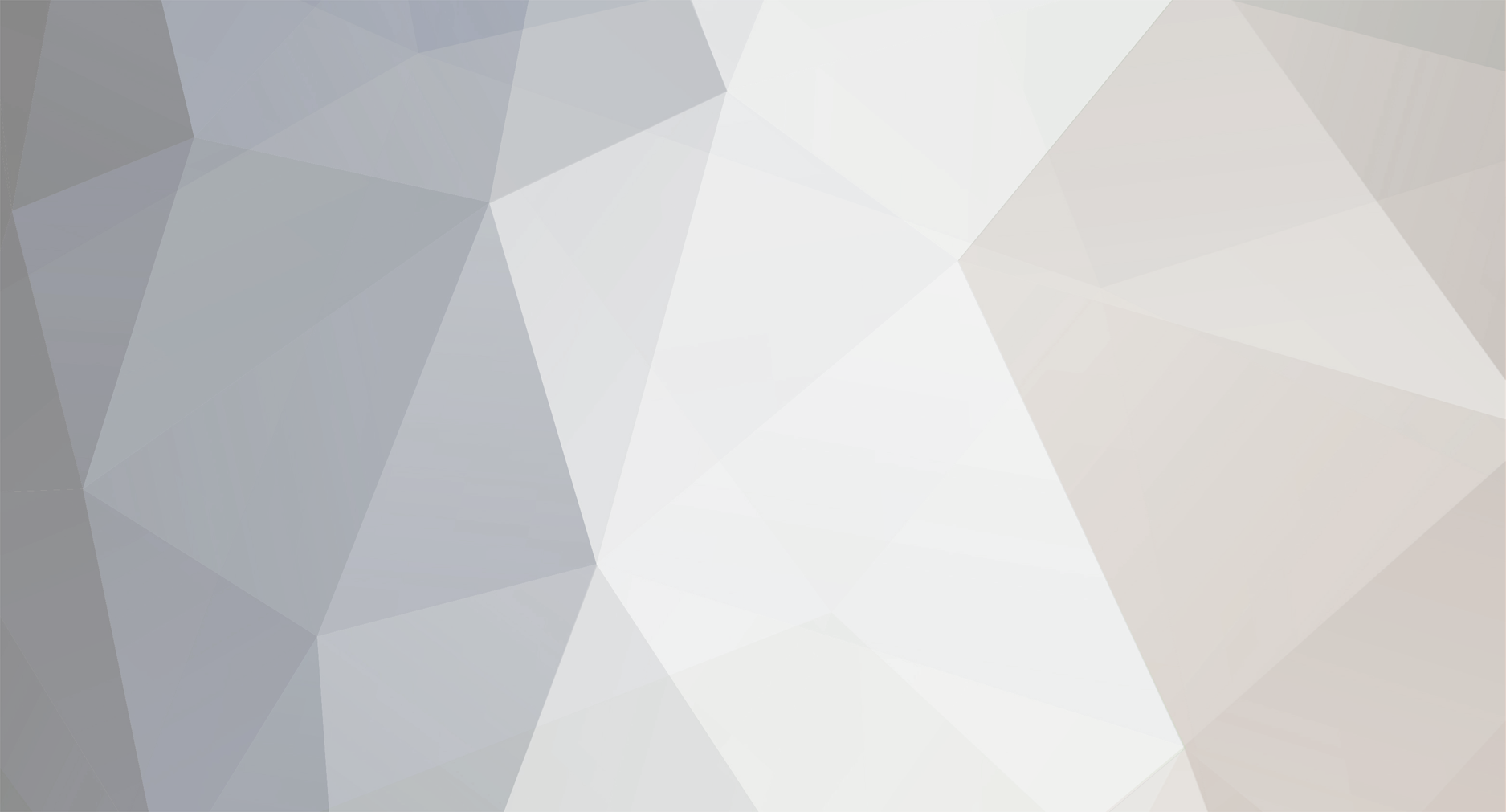
SAV
Участник-
Постов
387 -
Зарегистрирован
-
Посещение
-
Победитель дней
1
Тип контента
Профили
Форумы
Блоги
Загрузки
События
Весь контент SAV
-
На конкретных настройках производительность конкретная, понятное дело. Это софизм, понятно что поднятие производительности достигается увеличением подачи и напряжения. Никаких противоречий с моим тезисом здесь нет. Опять подмена понятий, производительность сварки оценивается в метрах в час конкретного размера и вида шва. Производительность в деталях/час, тоннах изделий/год это не производительность предприятия а не сварки.
-
Это если надо сделать метр шва, то можно поиграться и поварить со скоростью настроек. Если же надо под 100 метров шва сделать, то никто не будет играться а настроит производительность аппарата под максимальную контролируемую скорость ведения горелки. Понятно что в некоторых случаях возможности аппарата ограничены, но всё равно есть смысл работать на максимальной производительности.
-
На практике кстати в режиме КЗ, где я работаю, каждый диаметр проволоки имеет оптимальные параметры при которых производительность наивысшая при небольшом количестве брызг и хорошей температуре присадки. Если подняться выше, то начинает брызгать сильно а если опуститься ниже, то производительность падает и глубина проплавления страдает. На моём аппарате 0,8 это 5 м/мин., 1,0 это 4 м/мин., 1,2 это 3 м/мин. а 1,6 примерно 2,5 м/мин. Округлил до ближайшего удобного значения. Но не уверен что параметры точные, поскольку привод подачи вроде от обычного движка постоянного тока а он может менять скорость вращения в зависимости от сопротивления. Иногда после замены катушки приходится подстраиваться, хотя партия одна. Можно будет как нибудь замерить сколько реально метров отмотает за минуту на новой и пустой катушке а также как поджим тормоза влияет на фактическую скорость.
-
Именно... А как иначе? Вот мне надо получить катет 2-2,5 мм. в тавровом шве. Я на 0,8 проволоке выставляю подачу 4-5 метров в минуту чтобы скорость выхода присадки соответствовала оптимальной скорости заполнения шва для удобного и контролируемого ведения горелки. Затем я напряжением ловлю оптимальное плавление присадки, чтобы было стабильное горение дуги. А как можно делать наоборот? Не напряжение же заполняет шов? Заполнение происходит присадкой и от площади сечения шва, площади сечения проволоки и скорости подачи проволоки будет зависеть скорость движения горелки. Напряжение здесь при чём?
-
Тонкий металл тавровым швом с небольшими катетами варю в режиме КЗ. Подразумеваю заполнение стыковых швов на поворотных деталях. Соответственно, положение нижнее или под небольшим углом чтобы валик усиления формировался. Аппарат 250 ампер, 1 мм. надеюсь потянет в струе. Ещё есть интересный и непонятный момент, я проходил в вертикале сверху вниз стыковые швы без разделки на пятёрке. Чисто по ощущениям варится отлично, проплавление зачётное. Надо будет ещё поэкспериментировать в этом направлении. При широком зазоре и при отдельных деталях их грани прекрасно проплавляются. Во всяком случае детали плавятся намного лучше, чем после прохождения корня заполнять. Я к тому что не проще ли 5-6 варить в стык в вертикале под некоторыми углами сверху вниз за один проход, если в режиме КЗ?
-
Мне в первую очередь важно внесение на большой скорости хорошо разогретой присадки и разогрев детали дугой. Во вторую очередь важно минимальное количество брызг. В режиме КЗ разогрев и минимальное количество брызг достигается только на очень малых подачах, поэтому падает производительность где нужно заполнять зазоры и разделку. То, что я вижу на импульсе - позволяет иметь большую подачу и хорошо прогревать детали, к тому же почти без брызг. Но если это всё на смеси, то на чернине не вижу смысла брать импульс, проще смеситель взять, заправить аргоном мои немецкие баллоны на 200 очков и поливать струёй. Всё-таки простой аппарат надёжнее чем с процессорным управлением.
-
Производительность это скорость подачи присадки и больше никак. Напряжение нужно не для производительности а для того, чтобы присадка успевала плавится. У тебя хвост виляет собакой. Я как раз за сплавлением слежу и не накидываю холодной присадки. Если мне в режиме КЗ надо больше скорость заполнения, то я просто проволоку толще ставлю. 1,6 на подаче 2,5 м/мин. даёт ток 220-240 а жарит при этом лучше электрода. Это хреново, если уж заморачиваться с аргоном, то лучше нормальный смеситель купить и струёй поливать где надо. Так можно в углекислоте импульсом или нет? Если на дорогие аппараты нет пока денег?
-
170-180 ампер. Думаю на 1,2 вполне можно.
-
В смеси надо постараться в капельный перенос уйти, зато там мелкокапельный перенос получается вроде. Но смесь должна быть с большим процентом углекислоты. У меня смысл не в том, чтобы капельный перенос получить а наоборот, не заморачиваясь аргоном и смесителями в углекислоте обеспечить хорошее проплавление и поднять производительность. Буду экспериментировать, у меня есть керамический шнур для опытов со съёмной подкладкой. Хотя основной вариант вижу сейчас корень проходить в КЗ. Там проплавление неплохое получается кромок. Они в рекламе помнится гордились что гораздо выше заявленных токи показывают, подозреваю что при коротком замыкании неплохие. На проволоке 1,2 и напряжении изначально 18 - стабильное горение в КЗ происходит на скорости 3 м/мин. При увеличении подачи и напряжения теряется стабильность горения, аналогично и на другом аппарате. Это значит в переходный режим выходит. Силу тока при таких настройках показывает 120-140 А., но это среднее значение. Понятно что в момент короткого замыкания выше. Индуктивность на максимуме, чтобы сгладить нарастание и падение тока, да так и варит мягче. Напряжение в процессе работы поднимается до 19-22 вольт. На 1,2 понятно что на капельный перенос я не хочу выходить. Максимум на 1 мм. на этом аппарате. А я вот смотрю и уже не верю что там везде надёжное сплавление после всех этих примеров... От тока зависит до некоторой степени эффективность разогрева детали но с увеличением толщины теплопередача растёт непропорционально меньше. Тем более если хоть начало шва подогревать а дальше шов сзади уже горячий, тепло только вперёд может уходить. Опять же при тавровом в трёх направлениях уходит тепло а в стыковом только в двух. Сравнивают только толщину а количество направлений не учитывают. Это всё рвано как тавровое соединение из 6 мм. по отводу тепла.
-
Варил 0,8 мм. в капельном переносе на аппарате без регулировки индукции. Брызгало конечно значительно и швы были снаружи кривые, но металл прогревало зачётно... При заполнении в нижнем положении в лодочку большая часть капель будет оставаться на месте. Плюс - за счёт уменьшения индуктивности надеюсь уменьшить размер капель. Облицовку усиления можно делать в КЗ на 1,2 мм. Кстати по видео все три капли попали чётко в ванну и не вызвали брызг. Проплавление в этом режиме хорошее очевидно как раз по причине длительного объёмного воздействия раскалённой дуги в область сварки, что подплавляет основной металл, поддерживает температуру в ванне и даёт разогрев присадки, она аж закипает на 2 - 4 капле.
-
Вот это и интересно. Если всё равно в смесь упираюсь, то мне на том же аппарате проще остаться. Ну у меня как раз такой, Аврора 250. Порошковая проволока мне не интересна, да и красота мне ни к чему. Швы всё равно закрыты на изделии.
-
А чем хуже посмотреть как это делают другие? Не глазами же варят и разрушают, точно также глаза со стороны смотрят. Поэтому не имеет значения кто это делает. Я варю и так немало и разрушаю иногда. Ток это установившаяся величина, не на токах получают режим а не режимах устанавливаются токи. Я писал что с аргоном связываться не хочу. Активированную проволоку тоже искать не вижу смысла. Пока восновном тавровые 2-3 мм. иногда 5 мм. Поэтому варю КЗ. Но если пойдут стыки 5-10 мм. и там заполнение делать надо с хорошим проплавлением. По видео видно что капельных перенос дал очень хорошее проплавление в кглекислоте, только брызг многовато и они крупные. Да на видео гораздо лучше видно, чем большинству сварщиков через затёртую оптику... На фоне капельного переноса это ничтожные различия. Мне заполнять после корня, если не заморачиваться аргоном, то может проще на капельный перенос накрутить и заливать? В нижнем положении может и брызгать так не будет и глубина проплавления как у электродов... В крайнем случае думаю импульсный полуавтомат взять, он в углекислоте вроде должен дать хорошее заполнение горячей присадкой почти без брызг.
-
Если ванна от кромки до кромки перекрывает, то почему нет? В данном случае это одно и то же при первом проходе а сплавления присадки с деталями нет местами. Ниточный внутри валика уже него или весь валик сплавился с деталями? Как же тогда не весь металл приплавился, если он смочил? А просто у присадки не всегда есть возможность расплавить металл, если металл относительно холодный а присадка сама около температуры застывания. В случае струи всё прекрасно проплавилось, вопреки тому что он струю направлял только на подкладку, почти не перенося на детали. И ванна там огромная, она ограничена деталями, на открытом участке она была бы намного шире, поэтому края ванны это кромки деталей. Просто там дуга лупит во все стороны, предварительно подогревая детали и присадка хорошо разогрета. Да и скорость заполнения заметно выше, поэтому присадка надёжно сплавляется с деталями. Как результат - гораздо лучшее сплавление и прочность не смотря на то что он якобы не контролировал ванну. Ванна в случае струи это не место, куда попадает струя а весь расплавленный металл. Это намного шире чем узкая струя а при узком канале между кромок эта ванна за струёй поднимается вверх, так как не может расплываться в стороны.
-
Это ваши мысли, или есть всё-таки термин? Вы представляете себе ситуацию, когда ОТК спрашивает сварщика: у тебя есть сплавление? Сварщик ясновидящий? Для того и есть УЗК, чтобы увидеть отражение волны на границе сред, если не произошло где-то сплавление... У вас ОТК значит на слова сварщика ориентируется... Что я собственно и написал: А где обратная сторона сварного соединения у таврового одностороннего шва по вашему же ГОСТу? Никакого отношения корень шва к обратной стороне деталей не имеет. Корень шва где по схеме дальняя сторона зоны сплавления а она не всегда с обратной стороны. Ага, а как обеспечить заполнение зазора и усиление шва? С зазором от 0 до 0,5-1,0 мм... Да это тупо неточность обработки торцевых граней. Чтобы не полировали грани в идеальную плоскость без нужды. Усиление шва там якобы достигается продольной усадкой, но я не думаю что прямо сильно толще стенки трубы будет даже при нулевом зазоре. И что по вашей логике должно до меня дойти? Да жалуйтесь хоть в ООН... Думаете что если "попросили" вам не хамить, то сами можете смело хамить и тролить, никто вас не посмеет заподозрить в хамстве? Почитайте свои посты для начала...
-
Где есть и где нету? Что не понятно? Если есть по всему катету шва сплавление - то это надёжное сплавление. Если не по всей границе произошло сплавление, то в этом режиме не достигается надёжного сплавления. Вот пожалуйста очередной пример вброса с целью увода дискурса в сторону. А потом будут спрашивать как тема про несплавления ушла в обсуждение терминологии и нормативной документации... Запоминайте тролей... А что такое корень шва? В большинстве случает он вообще формируется присадочным материалом. Не надо рассказывать что обе детали обязательно должны сплавится. Во-первых в этом нет необходимости, поскольку материал присадки ничем не хуже материала деталей а во-вторых это просто невозможно при наличии зазора. Корень всегда будет залит присадкой. При наличии зазора без присадки вообще невозможно сплавить детали. Без присадки варят без зазора и без разделки а это очень редкие частные случаи работ. Зазор для того и делают, чтобы туда затекала присадка и обеспечивала сплавление в дальней части шва, которая и есть корень. Никакого замешивания металла деталей при такой технологии не предусматривалось да и необходимости в этом нет. Границы, видимые на срезах шва это не столько разный химсостав сколько разная кристаллическая структура. Поэтому глубина провара вовсе не означает что на эту глубину произошло замешивание присадки и детали. Физическая граница металла присадки и детали находится внутри видимой области провара. То есть нужно срочно запретить все виды сварки, кроме лазерной??? Таки-зачем?
-
Думаю что не проблема найти кто сделал вброс про вагоны... А первое исключает второе? Здесь вообще-то форум, поэтому исключительно теория. Да и под тонну проволоки с электродами уже уварил пожалуй, это ещё теоретик или уже практик? Вопросы темы простые, как обеспечить надёжное сплавление металла детали и присадочного материала.
-
Скос кромок - это действие с кромками а результат этого действия - это наклон кромок. Естественно что я говорю о геометрии а не об обработке. Я инженер... Блин, ну сколько можно нести чушь? Погуглить лень что такое бестележечный вагон, если не понять по названию? http://www.modelmania.com.pl/images/roco/76302.jpg Бестележечный вагон воспринимает нагрузку от подвески по углам, как автомобильная рама, о чём я и писал... Весь этот набор слов, вырванный из контекста и призванный сбить с толку и заболтать вопрос, сделав вид что вы чё-то там понимаете... ))) По существу вопроса: 1. Я уже приводил вашу же цитату, где сказано что крутильные нагрузки на раму возникают только на бестележечных рамах 2. Все слова про пропеллерное скручивание относятся к бестележечным рамам, как я и писал изначально, поскольку только в случает бестележечных рам возникают скручивающие нагрузки, как и указано в вашей же цитате 3. Если вы не понимаете что такое бестележечный вагон, не видели его, то почему считаете что а этом, неустойчивом для скручивания случае применяется стыковка швеллеров непосредственно? 4. Зачем вы сделали вброс вопроса о правильности стыковки швеллеров в теме про несплавления швов а затем накидываете кучу букв с попытками неверной трактовки написанного? Вы троль?
-
Я о том и писал, если рама не тележках, то там вообще нет причин для скручивающих нагрузок. Если только какой дурак положит тяжёлый груз по диагонали платформы... А дальше рассматривается как вариант в том числе последствия скручивания в случае бестележного вагона. Как я и писал, никакой принципиальной проблемы сварить швеллеры в стык при отсутствии скручивающих нагрузок нет. Нагревают до 600 градусов и добиваются рекристализации. В результате исчезает переходная зона и зона термического влияния. Сам шов от трубы отличается только толщиной и немного химсоставом. Вот и понятно почему у отожжённых швов не стремятся делать наклон кромок. Просто у отожжённого шва нет ослабленной переходной зоны и не имеет смысла её располагать под углом...
-
Да, тема про сплавление а мы вагончики будем клеить... Сама рама опирается на тележку не углами даже, ей нет причины скручиваться. Я объясняю лишь то, что сваренные из швеллеров рамы не являются чем-то запредельным с точки зрения споромата. Хотя я бы для крутильной жёсткости из трубы делал, что я и делаю при конструировании оборудования. Это какой диаметр? Паровозы всё ещё варят, к войне готовятся? Видел как трубы атомной станции варят, корень проходят ТИГом а заполняют ручником. Потом заматывают асбестом и прогревают несколько часов ТВЧ чтобы рекристализовать шов и околошёвную зону.
-
А как наклоны полотна могут приводить к скручиванию рамы? Для скручивания должно быть как минимум возвышение одного или двух диагональных концов рамы. Железнодорожные пути в нормальном состоянии не имеют таких дефектов, это только на автомобиле может случиться. Вы скручивание от прогиба (изгиба) не отличаете, какой тут разговор о сопромате может быть... А кто ответственные швы на прихватках делает? Ставьте мосты, чтобы остатками всякого шлака шов не засерать... Пока конструкции были не особо нагруженные, но если труба пойдёт, то вопросами надёжности придётся озаботиться сильнее. Тогда и буду это делать. Сейчас вопрос стоит в том, как в углекислоте обеспечить надёжное сплавление деталей и присадки а также обеспечить общую прочность не ниже прочности трубы.
-
С 2007 года трубами занимаюсь и не помню чтобы кто хоть раз под толщиной трубы понимал толщину СТЕНКИ трубы... Помимо пластин для малых диаметров можно применять подкладной шнур. Как увеличение зазора может снизить прочность соединения? Сам шов заведомо прочнее околошовной зоны, будь он хоть 5 см. шириной. Максимальная величина зазора в совковых гостах нужна была только чтобы казённые сварочные материалы и рабочее время сэкономить. Просто так непоуму. На прочность конструкции это не особо влияет, поскольку поперечный швеллер замкнут и работает правильно а продольный имеет низкую жёсткость на кручение, если его торец не замкнуть а лучше ещё м перемычку вварить напротив другой стороны швеллера. Ходить конечно будет, но жёсткость слабовата на кручение. Теперь вопрос, на рельсах жёсткость на кручение сильно важна? Там скручивающих нагрузок не возникает а растягивающие и изгибающие такое соединение вполне может держать. Только какое это отношение имеет к непровару???
-
А что мешает зазор увеличить? Вон немцы при любом случае зазоры разводят и подкладной материал клеют... На больших диаметрах возможно напряжения меньше. Там пропорции другие и отношение диаметра к толщине. Только тем, кто не знает сопромат... Основные рабочие напряжения на заведомо слабую плоскость, расположенную под углом действуют под тем же углом. Соответственно, нормальная составляющая заведомо меньше чем основные рабочие напряжения. Если проще объяснять, то деревянные ламели клеят не под прямым углом а нарезают гребёнкой под углом. Зачем, чтобы больше клея потратить или чтобы увеличить размер клеевого соединения, которое слабже основного материала? Чем больше будет размер слабой области, тем больше она будет иметь абсолютную прочность, поэтому делают усиление шва. Чем больше от перпендикулярного будет отличаться угол ослабленной плоскости, тем меньше будут действовать растягивающие напряжения на ослабленную плоскость.
-
Посмотри второе видео которое я запостил. Края ванны это разделка кромок. Корень заменён стальной подкладкой. Там видно ванну и её края? Да. Результат на изгибе показывает что сплавления присадки и детали не произошло. Что тут не понятно? Что толку смотреть на края ванны, если стекающий металл присадки не подплавляет детали а сам тут же застывает? На первом видео видно что проплавления металла в случае КЗ и струи происходит только в зоне прямого действия на детали дуги. В остальных местах, куда присадка стекала самотёком геометрия шва совпадает с геометрией деталей до сварки. Границы прямые. Это значит что невозможно сказать произошло ли сплавление детали и присадки а скорее всего оно не произошло. Получается что при заполнении в режиме КЗ необходимо совершать движения, при которых дуга будет воздействовать на детали, иначе не обеспечить подплавление деталей только за счёт тепла присадки и протекания тока. Это в свою очередь значит что ошибка может привести к несплпвлению и браку. Не понятным остаётся два момента, если капельный перенос в первом видео дал хорошее проплавления без колебательных движений, то не лучше ли его использовать в углекислоте? И второй момент, почему на втором видео струйный перенос обеспечил хорошее сплавление не смотря на то, что на первом видео результат мало отличался от режима КЗ?
-
Если труба поворотная, то в вертикале сверху вниз есть смысл варить только корень. Заполнять проще в нижнем положении, зачем делать вертикал? Чтобы снизу вверх кривой гнать? Если даже 1,2 мм. применять в КЗ, то за один проход не факт что получится всегда заполнять как на видео в пульсе. У меня есть опасения что в КЗ могут быть несплавления местами. Подрезов там быть не должно, так как нет никаких проблем немного увеличить угол и варить на 11 или 10 часов. Там валик с плавным переходом сам получается прекрасно. Главный вопрос ещё раз, есть ли вероятность несплавлений в режиме КЗ при заполнении в нижнем положении, как на втором видео? Там вообще нет сплавления присадки с деталями, как специально.
-
На сколько помню из теории, у нормального шва прочность заведомо больше, чем прочность в переходной зоне около шва. Глубина проплавления нужна хоть минимальная, чтобы произошло сплавление присадки и основного металла. В ПА добиться замешивания присадки и детали, не говоря уже о замешивании двух деталей очень трудно. Это в ТИГ, там грей хоть полчаса... При тавровом соединении, если обеспечено сплавление, то катет не имеет смысла делать больше толщины детали, поскольку деталь будет менее прочная, чем шов. Проплавление вглубь позволяет только увеличить размер ослабленной околошовной зоны, что позволяет при меньших допустимых напряжениях обеспечить равную прочность с основной деталью. Аналогично и при стыковых соединениях, разделка важна прежде всего для того, чтобы ослабленная околошовная зона была не минимального размера перпендикулярная детали а располагалась под углом и имела больше размер, при этом напряжения по нормали в этой зоне будут меньше, чем без разделки. Теоретически с подкладным материалом можно сделать большой зазор без разделки и залить его присадкой. Но переходная зона будет почти плоской перпендикулярной и ослабит деталь.