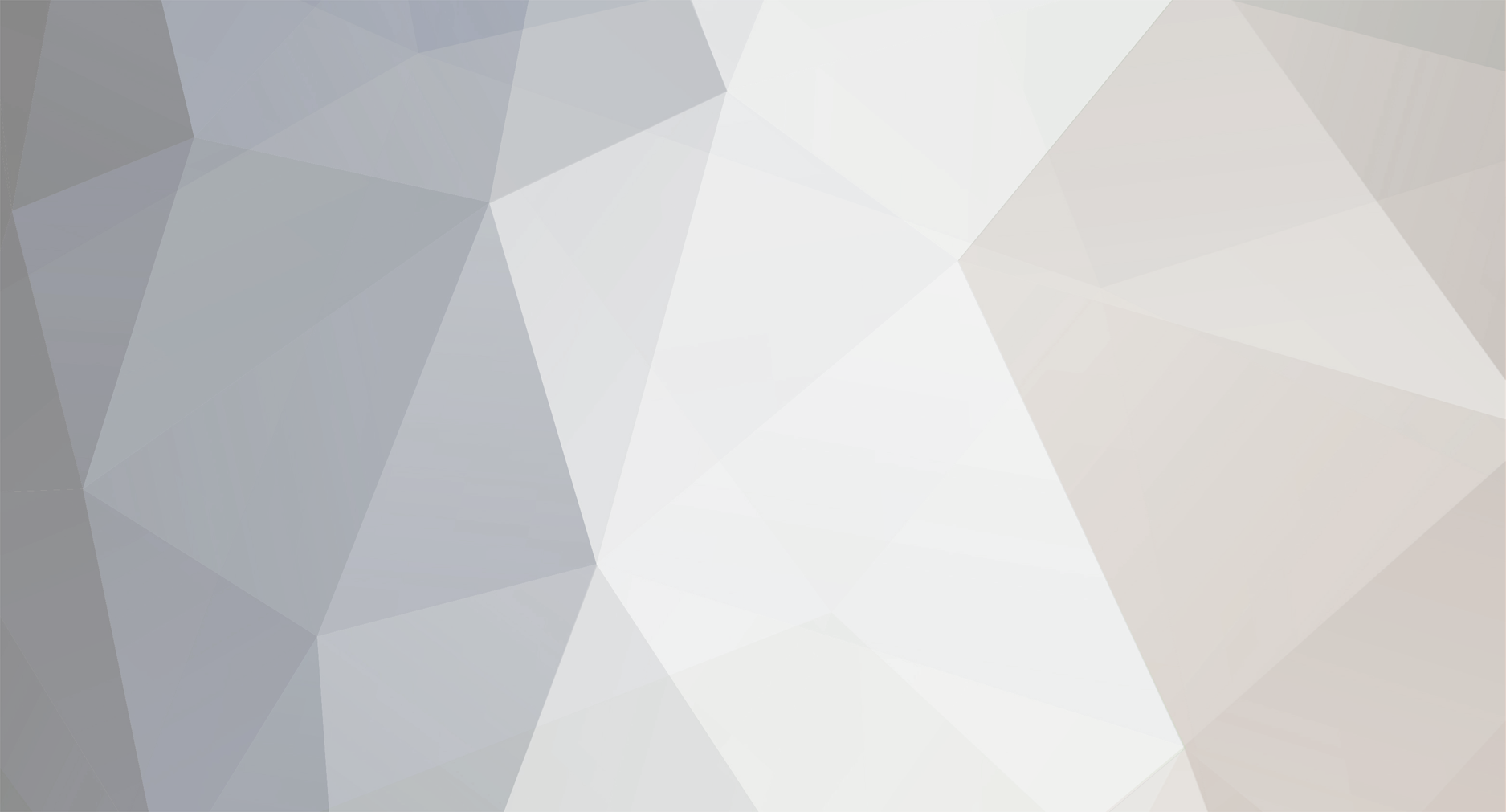
Oswer
Участник-
Постов
288 -
Зарегистрирован
-
Посещение
-
Победитель дней
3
Тип контента
Профили
Форумы
Блоги
Загрузки
События
Весь контент Oswer
-
@Steelcar, Жестко, дверцу на шины, не позавидуешь, особенно в тесном пространстве. А если говорить о более высоких линиях, то у "шестерки" идущей по частному сектору, и при том сильно разветвленной, есть единственный недостаток - отключают часто (по причине аварий или разных работ). Линию на 35 кВ, а тем более на 110 кВ "рубят" сильно реже, как никак это магистраль. А отключать электроснабжение расточного станка нам финишном проходе, или плоскошлифовального с электромагнитным столом бывает черевато.
-
Пока не получается, встало на ручник (временно отвлекли). Но могу описать процесс. Наш "театр" начинается с вешалки, на которую повесили автогазовай выключатель нагрузки и предохранители (общие). Получилась входная группа: Ну это конечно не считая "скворечника" (вводного узла с проходными изоляторами и защитными разрядниками). Со входной группы поворачиваем на группу высоковольтного учета: Трансформаторы напряжения, тока, и их низковольтные провода. Ну и вся группа целиком, с пары ракурсов: Горизонт завален (к счастью это только на фотографиях). Так же я пролоббировал вынос шинопровода в трансформаторную камеру, это многократно упростило мне расшивку: Его сверху видно. Главная проблема была в том, чтобы уйти с учета на размыкатели трансформаторов, а те стоят по бокам подстанции... Ну это мелочи, удалось выпутаться по простому. К опорам шинопровода, честно говоря, был применен перк "кривые руки" второго уровня, это вызвало наложение геометрии Лобачевского на нашу реальность. Выправлять не стал, даже и не спрашивайте почему. На функционал не повлияло, а перед собой мне стыдно не бывает, тут уж извините. Пара общих видов: Здесь видны коммутационные группы трансформаторов, и проходные изоляторы в трансформаторную камеру. Левая группа в процессе сборки. Подвод к трансформатору, проводом, но с зазорами превышающими требования к шинам, по этому можно. Да и ток маленький, всего сорок ампер. Решетки отгораживающей подводящую шину пока нет. Немного "цветовой дифференциации штанов": И это куда как не конец, это только середина. Еще нужно доделать холодную сторону, группу коммутации резерва (генератор), и компенсацию реактивной мощности. Да кто же мне по серьезному разрешит? Там в пределах километра идут две линии, на 35 и 110 кВ, но нам это не доступно, у нас только "шестерка" под боком... P.S. Блин, на перегоки пишем? P.P.S. Еще одну забыл: На ней уже и скотч снят, и начали стойки шкафов появляться.
-
Неужели детали флюгера? Было бы здорово увидеть его в сборе.
-
Статистика по цвету примерно такая: - "горчичная" светомасса - это светосостав постоянного действия, как правило содержит соли радия для активации люминофора. - светло-зеленая - это накопительный состав, светит после нахождения на свету, постепенно снижая свою эффективность до следующей засветки. Но тут могут быть вариации, например может фонить не "горчичная" светомасса, но это редкость. Кроме часов есть еще шкалы приборов (видел какой-то манометр с ж/д подвижного состава с похожими цифарми на шкале), "глазки" в старых тумблерах, компасы Адрианова и многое другое. А 1975 год, это скорее всего тот момент, когда соли радия в светомассе перестали применять окончательно (не раз слышал, что приборы после 75-го безопасные, но иногда называют более ранний год окончания применения радия). Неужели есть смысл подделывать такое сложное механическое устройство, им цена на том-же Авито то 1000 до 6000, ну может чуть дороже. да и берут их не каждый день. Хотя кто его знает.
-
Верное замечание, СПД с солями радия там встречаются, но не во всех. По вашей ссылке видно, что цифры на циферблате характерного "горчичного" цвета, это оно и есть. Причем иногда фонит жестко, когда такое покупаешь, недурно проверить дозиметром (ладно, хотя-бы "трещалкой" на счетчике Гейгера, отбраковывая любые которые дают превышение над фоном), а то там могут быть сюрпризы. Хотя есть и нормальные экземпляры, без радия, они более поздних годов выпуска (с какого момента стали делать безопасные, я уже не помню). А если по теме брызгостойкости (имею ввиду сварочные брызги и искры от УШМ), то более стойкие с полимерным стеклом, к минеральному брызги пригорают очень хорошо
-
Я обламывал, но скорее по привычке, мне так удобнее на толстых электродах (у меня были четвертые). Проводимости обмазки там скорее всего нет (железный порошок в обмазке разрозненный, и не дает полноценной электропроводности). Ну и если приглядеться к кончику стержня после сварки, там часто виден тонкий слой коричневого "стеклянного" налета, так-что просто при касании оно скорее всего не загорится, придется "чиркнуть" с нажимом. Хотя наверное еще зависит от аппарата, напряжение холостого хода будет сильно влиять на комфорт повторного поджига. P.S. Это если речь идет о повторном поджиге, обычный старт был без проблем, как и всегда у ESAB'а.
- 4 ответа
-
- 2
-
-
Я когда самостоятельно учился варить (это было три или четыре года назад), для пробы брал их, было интересно что они из себя представляют. Тогда мне показалось, что они довольно требовательны к навыкам сварщика, особенно на вертикале (сейчас понимаю что это не совсем так, просто навыков у меня тогда совсем мало было). По моему субъективному мнению, ванна у них горячее и жиже чем на УОНИ такого же диаметра (они требуют больше тока). Внутренний угол мне ими понравилось варить, нижнее положение тоже без проблем, горизонтал (на вертикальной плоскости) мне тогда не дался толком, вертикал на подъем труднее чем УОНИ, потолок вполне сносно, но шов более выпуклый получался. Корень варить я ими тогда не смог, но это не электроды виноваты были . В основном жег их при "плюсе" на электроде, пробовал менять полярность, горят по другому... в чем именно отличие я наверное не смогу объяснить, просто кажется что электрод горит более "нервно" и менее ровно, приходится чуть завышать ток. Но какой либо критической разницы во внешней геометрии шва заметил. На переменке жечь их не пробовал, но производитель говорит что можно. Заявленные прочностные характеристики, особенно на морозе, радуют глаз. P.S. Мое ИМХО, при работе ими, лучше иметь в виду повышенную текучесть их ванны, если варить что-то не слишком толстое, то стоит быть осторожнее с выбором диаметра электрода. Я брал 4мм, варить ими что-то тоньше 8мм мне было тяжело (хотя повторюсь, я был неопытный). Уж не знаю на сколько полезно мое мнение, но о своем опыте написал как есть, правда опыт не большой, шесть килограммов всего их сжег.
- 4 ответа
-
- 1
-
-
Судя по всему плазма, но могу быть не прав.
-
Вот я почему-то как узнал,что речь идет о датчике для панели приборов, подумал что дойдет до связки из доступного датчика и совместимого с ним прибора (но озвучивать не стал, думал меня тапками закидают ). На моей первой работе, в автобусном парке, мы также делали - вместо датчика температуры двигателя (или давления масла) от VDO ставили на Мерседесы отечественные датчики, через штуцер-переходник, а на панель ставили прибор от камазов старого образца (где приборы круглые по отдельности стояли). И ездило годами, причем на десятках машин (правда наши датчики давления масла дохнут часто). На мой взгляд, решение вполне жизнеспособное. Мне почему-то кажется, что @Глобул не отговаривает от такого решения, а предрекает ему долгую жизнь. А я вообще сперва подумал, что датчик завязан на блок управления ГМП, у меня ГМП ассоциируется с ZF или Voith (но это из-за автобусов).
-
Да, а ведь это сильно осложняет ситуацию. Я это упустил из виду. Вот в том то и дело, что аналогово это один гемморой (там имитировать характеристику вспотеешь, если вообще выйдет), а в цифре - это другой гемморой (тут уже надо обладать навыками программирования, а не только схемотехники). Хотя, возможно это верный путь. Можно попробовать найти кого-нибудь из студентов, которые дружат с микроконтроллерами, подросткам может быть интересно, и не сильно сложно (хотя чужой труд может выглядеть легче, чем на самом деле). У микроконтроллеров, даже у дешевых, сейчас есть АЦП на борту, а питание можно получить простым и дешевым линейным стабилизатором. Но тут какое дело, чтобы снять зависимость сопротивления от температуры, нужен живой датчик, а где его взять? Даже если есть другая машина (рабочая), дадут ли ее разобрать, чтобы снять датчик и провести замеры? Ну и микроконтроллер - это все-же немного более габаритно (даже если не делать печатную плату для него), хотя это мелочи. P.S. Интересно, коробка передач чьего производства?
-
Сам по себе - да, ничего не выдает. Но он ведь куда-то подключен. Как вы и говорите, там на другом конце провода должен быть прибор (термометр), или блок управления. Так-что в любом случае через датчик идет какой-то ток, и его выходе изменяется напряжение в зависимости от температуры. Каскад должен сымитировать это изменение напряжения (для этого надо пустить ток через датчик, образовав делитель с помощью дополнительного резистора), но калибровка - это отдельный гемморой (при том локальный). Работает онскорее всего по напряжению, как и большинство автомобильных датчиков (если он подключен к блоку управления). Просто мысли в слух, как посчитать (даже имея ВАХ и родного датчика, и замены) я на вскидку не скажу. Хотя может меня глючит, и я не прав... давно не трогал аналоговую электронику.
-
@supoplex, вот и у нас листогиб на модернизацию напрашивается, нужно поставить энкодер на гибочную балку, линейку на задний упор, линейку на нижнюю балку (она опускается под толщину металла). Но прежде всего гидростанция - насосы там рабочие, но некоторые клапана в гилроблоке иногда заклинивает (и это при чистом масле), так что гидравлика будет первой на очереди. Конечно хочется ЧПУ к нему, благо Константин начал осваивать MESA и можно будет собрать относительно бюджетный комплект. На 1М65 одну из линеек (продольную) придется брать магнитную, стекло не доедет. А угловой позиционер который лежит на полке, я хочу прикрутить к трбогибу, будет малая автоматизация . P.S. Вот блин, в начале четвертого десятка начинаешь понимать, что с приходом возможности к техническому творчеству (когда есть материалы и оборудование) на него просто начинает не хватать времени. Мне бы все это, и времени свободного, как в детстве .
-
@Фунтик, это хорошо, что и "кратковременная реанимация сознания" и реанимация линии прошли успешно. А так, если быть честным, такой человек - это серьезная угроза простоя линии, да и ТБ на пьяную голову нарушается чаще... в общем, опасная ситуация. @supoplex, эх, напомнили про автобусы... Как вспомню Mercedes O345 или O405G - так там местами позабористее Тошибы было: электронный газ (на механическом ТНВД), автоматическая коробка передач (ГМП Voith DIWA II), многочисленные системы защит (блокировка движения при открытых дверях, блокировка при превышении угла изгиба сцепки на сочлененных автобусах, ABS/ASR, система противозащимления на дверях и куча защит от неправильных действий водителя). А им на момент моей работы и ними было 15-17 лет. Но все равно, я их на то время любил за добротность конструкции, и сейчас считаю многие из тех конструктивных решений удачными. А вот НЕФАЗы выпуска конца нулевых: это словно мир Говарда Филлипса Лавкрафта для электрика - никакой логики, только мерзкие и необъяснимые конструкторские решения, сквозящие безумием и приводящие в отчаянье (потом говорят лучше стало). Но собственно можно и к мастерской вернуться. Нашел у себя фотографии установки линеек на Dainichi (японский токарный станок). Процесс был нудный и прерывистый, по этому есть некоторые моменты, которые не попали на фотографии. Поперечная линейка (без защиты и с кожухом из стального уголка): Кронштейн измерителя и "бампер" на задней бабке: А это кронштейн измерителя продольной линейки. Я сварил его из подходящих кусков металлолома (да, швы мои, увы варю редко, а от того местами получается страшно), а Константин фрезеровал и сверлил. Сама продольная линейка. С ней, к сожалению, не все так просто. Китайцы наотрез отказываются отправлять длинные стеклянные линейки обычными способами доставки (как выяснилось, не зря). Их иногда удается уговорить (на свою голову). На первом фото видно жирный "горб" на линейке (но она целая и рабочая). Пришлось ее править по месту (сделал несколько кронштейнов, закрепил их на станине и осторожно отжал болтами линейку), процедура прошла успешно, но как мне кажется на грани фола (в самом критичном месте был прогиб около 6 мм). И сам "телевизор" (поселили на коробке скоростей, станок не длинный): Ну и просто немного бардака, который я развел при работе со станком: На первом фото, на заднем плане, видно начинку фартука 1М65 который на тот момент тоже был разобран для ремонта. А на втором фото можно (правда с трудом) наблюдать решение проблемы кабелей фартука (штатный кабель, и два кабеля от линеек) - убраны в 50-й металлический рукав (там еще место для шланга СОЖ осталось). Кстати, тут @Lohus, спрашивал о том как привыкают токаря к "цифре" и просил фото/видео. Фото установки появились, видео работы наверное позже снимем. Токаря к цифре пока не привыкают (УЦИ на этот станок поставили недавно, и в работе он был мало, я его использовал пару раз с тех пор), но фрезеровщик привык и успешно использует. Да и не обязательно это - у них же лимбы никто не отбирает , не хочешь цифру, не смотри или выключи. От себя скажу, что последний разряд (который обладает дискретностью +/-0.005мм) на станках нормальной точности является просто ненужной информацией (он от вибрации станка постоянно скачет), а вот сотки уже ведут себя нормально: и на холостом ходу, и при точении.
-
@Леонов Сергей, не, это только со стороны так кажется. На самом деле, когда начинаешь делать все от начала и до конца сам, в голове складывается четкая картина: что, откуда, зачем и куда идет, и к чему все эти вещи приводят. Я вот когда чинил электрику на нашем фрезере 6Т12, тоже не смог разобраться в чужих "ремонтах" внутри щита с релейной логикой. Мне оказалось проще и быстрее высыпать весь щит наружу, а потом полностью собрать заново. Было: Стало: Потом еще добавил (после замены концевиков на индуктивные): Так что, не все так сложно, как кажется. Главное начать.
-
Забыл написать, в конце прошлой недели наших сварщиков постигла беда: в масках сели батарейки. У троих человек сразу... блин, это точно не заразно? Ну казалось бы, в чем беда? Ну сели батарейки, поменял. Но нет, это более замороченный процесс. В этих ESAB'ах батарейки приварены к выводам, припаяны к плате и похоронены в фильтре. Вот так это выглядит: Будем лечить маски от внезапной напасти: Берем донора и пересаживаем панельку для батарейки на фильтр. Собираем фильтр обратно и ставим в маску: И так три раза. Все, теперь все просто и удобно: села батарейка - поменял. Уж батарейку CR2032 можно купить в любом магазине, даже на кассе в супермаркете .
-
Ну вот, сегодня мы с Константином наконец закончили ремонт трубореза 1М983, я про него писал здесь. На сей раз работ было немного: собрали вал продольной подачи, поставили на место гидроагрегат и новые щетки муфт, и поменяли сгоревшее токовое реле (и контактор заодно). Вышло излишне долго из-за логистических проблем, посылку с муфтой и щетками только вчера смогли доставить. Фотографий почти не делал. Гидроагрегат получил новый двигатель, правда несколько большего размера, и не фланцевый, это потребовало изготовления нового кронштейна: Несмотря на выросший размер все отлично вписалось на прежнее место, ниша в станке просто огромная. Ну и щит с новым контактором и тепловым реле: Что удивительно, щит стоит отдельно от станка, прикрепленный к стене, а со станком его соединяют два кабеля.
-
Кто тут вспоминал труборез пару страниц назад? Внезапно на меня свалилось такое счастье, как ремонтные работы по станку 1М983. У людей возникла проблема с подачами (пропала поперечная - в обе стороны, и продольная - в одну сторону), а еще выбивает какой-то автомат, и перемычку поставили (иначе не запускается), ну и дым пошел откуда-то сзади. В общем, не работает. Сразу предупрежу: подробных фотографий нет, не до того было. Собрали инструмент, и вдвоем с напарником выехали на ремонт. Подач нет, слышно как срабатывают муфты (три из четырех), мотор быстрых подач работает, но по поперечной подаче перемещений нет, продольно только в одну сторону. Надо разбирать фартук. Внутри фартука нас сходу ждал сюрприз. Один подшипник (шариковый упорный) лежит внизу, по частям. И еще пара роликовых конических высыпались при снятии крышки (сепараторы целые, но не держат ролики): Сюрприз был оперативно демонтирован и собран на тряпочку, номера подшипников записаны, подшипники заказаны. Это мелочи, их несложно поменять. Но почему нет подач? Поверяем муфты - три работают, одна... замкнута. Неприятно, но дает ответ на вопрос, почему нет одной из продольных подач, и почему выбивает автомат (он как раз и стоит на питании муфт, между трансформатором и выпрямителем). Сразу снял вал продольной подачи целиком, муфту на месте не снять. Заодно снял щетки (не уверен что правильно называю эту часть контактного узла), они сильно уставшие, их уже чинили и как минимум одна из четырех потребует замены или ремонта. Дальнейший осмотр показал, связь между фрикционным валом поперечной подачи и ее винтом нарушена. Где-то в паразитном блоке шестерен что-то срезало. К счастью у этого станка (в отличии от 1М65) есть крышка открывающая доступ к этим шестерням без снятия фартука. Открываем и сразу видим в чем беда - выкрутился стопорный винт, который не дает проворачиваться одной половинке шестерни, по отношению к другой. Самого винта нет. Недолгие поиски в недрах фартука ничего не дали, а вот поиск магнитом в ведре с маслом которое мы оттуда слили принес результат . Совмещаем половинки отверстия и вкручиваем винт (позже закернил, но не сфотографировал): Ладно, с подачами разобрались. Муфту найдем и закажем, комплект щеток тоже (совместно с заказчиком разумно решили, что если уж муфту придется заказать, то и щетку чинить не стоит, проще не "экономить на спичках", благо стоят они не дорого). Теперь поищем перемычку без которой не запускается, найдем, уберем, и заставим работать без нее, как и было задуманно заводом. Недолгий осмотр показал, перемычка "обходит" контакты теплового реле стоящего в цепи электродвигателя насоса смазки (у коробки скоростей за смазку отвечает отдельный гидроагрегат). Сработка этого теплового реле запрещает запуск не только гидронасоса, но и главного двигателя. Еще немного осмотра и замеров приносят неутешительный результат: сгорела одна из секций реле и сгорел электродвигатель насоса (он и задымил). Его мы поменяем, а вот порядок сгорания я бы хотел узнать (скорее всего сгорел двигатель, поставили перемычку, двигатель догорел до замыкания и сжег тепловое реле). Вывод прост, элементы защиты придумали не просто так. Волшебный дым (на котором работает все электрическое) покинул этот двигатель, и этот двигатель не может больше работать . Теперь ждем доставки муфты и щеток (удаленность нашей дислокации накладывает свои особенности на работу). А вообще, станок интересный, позволяет резать конические резьбы (для меня было загадкой, как это реализовано). Ответ нашелся на месте: Оказывается винт поперечной подачи имеет свободное скольжение вдоль своей продольной оси. Передняя его часть глубоко входит в рукоятку подачи, вращение передается посредством шпонки, а его задний конец жестко связан с ползуном (узел видно на первой фотографии). Сам ползун может ходить в пазу, который можно повернуть в горизонтальной плоскости (как суппорт резцедержателя на токарном станке) задавая конусность резьбы. Когда эта функция не нужна, опора связывающая этот ползун со станиной снимается. А еще у этого станка моторизирована затяжка и ослабление патронов (но окончательно затягивать нужно вручную): На первой фотографии видно оба патрона и рукоятку переключения привода зажима (самая верхняя, посередине). На второй фотографии, сверху в кадре, электродвигатель затажки патронов, а под ним шкив ременной передачи главного электродвигателя, он содержит в себе муфту сцепления (электромагнитную), если присмотреться, то можно разглядеть по середине шкива контактное кольцо и графитную щетку. Ну и просто несколько фотографий: На первой виден ручной тормоз шпинделя. На последней сгоревший гидроагрегат в сборе (насос Г11-11 и двигатель АИРМ63А4У2) Кстати, патроны у него интересные, четырехкулачковые, с общей затяжкой (как на обычном самоцентрующемся патроне), но с отдельной подтяжкой каждого кулачка своим винтом. Нашел еще фотографии . И снова по теме которую недавно обсуждали (но тоже имеющие отношение к этому станку). Это же "шланговая" муфта, целая и рабочая (в отличии от электродвигателя): Тут видно все: и шланги (в роли демпфера), и обрезки болтов (в роли пальцев), и всю незамысловатость конструкции (две половинки выточили на токарном станке, а потом просверлили по стыку). Все рабочее, передаваемая мощность маленькая (0,25 кВт), а муфта довольно большая. А еще видно очень кустарный кронштейн, отверстие резали УШМ, а потом чем-то скруглили. Станок по слухам был взят довольно давно, с завода который проводил ему капитальный ремонт (купили, откапиталили, продали). Ну вот, опять длиннопост получился...
-
Да, вы правы, наличие муфты не отменяет необходимости соосности валов, но нам тут остается положиться на изготовителей узла, в котором стоит муфта (соосность задали они, изначально), в соосности валов Тошибы я не сомневаюсь. Это вообще хороший станок, с ним приятно работать, и он служит примером, как надо делать промышленное оборудование. Для единичного экземпляра это нормально, да и ходить такая деталь будет не в пример дольше родной (пластиковой). Лить под давлением пару штук не будешь (цена будет космическая). Да и в отходы не слишком много ушло, два кубика которые остались по бокам будут убраны на полку, и позже станут материалом для каких-нибудь деталей. Да, изготовление литьевых форм это вообще затратное занятие. Но если учесть, что в этой форме отольют многие тысячи грузил (а при бережном отношении со стороны литейщика и дестки тысяч), то никакой стружки не жалко.
-
Тут наверное все зависит от условий работы муфты. Если узел "открыт всем невзгодам" при работе, то наверное долго не проживет, особенно если есть возможность собирать абразив. Но внутри какого-либо агрегата он будет жить спокойно. Его долговечность будет обусловлена стойкостью эластичной вставки. Вот пример из коробки скоростей нашей Тошибы: Узел по частям (мы изготовили только эластичную вставку из полеуретана), и в сборе. Обломки старой вставки (рассыпалась от старости), и место монтажа (электродвигатель пока не установлен): Кроме масла туда ничего не попадает, должна прожить долго. У муфт с круглыми пальцами есть преимущество в полевом ремонте, можно подобрать подходящие куски резинового шланга. Часто вижу такой ремонт на гидростанциях отечественного станочного оборудования, но шланг быстро разбивает. А на фото изношенной муфты (той что клиент принес) видно что поздно за ремонт взялись, полумуфты успели побиться друг об друга без резины. В таком случае любую конструкцию нужно будет изготовить заново. Эх, мы бы рады, но нам каждый раз несут разные радиаторы, как сговорились . А у тех клиентов, что приходят с большой кучей одинаковых, с бачками проблем нет, они стальные, на болтах прикручены.
-
Возможно о станке в котором зажат материал заготовки (станок ведь не весь видно). Но по факту это станок 1М65 (потомок ДиП-500). Трубонарезных станков 9Н73 не видел, но наш 1М65 похож на трубонарезной 1Н983, особенно с таких ракурсов, как в том сообщении.
-
@Фунтик, идея с порошковой горелкой хорошая, она тоже приходила нам в голову. Но я ума не приложу, как сделать стабильную и надежную угольно-порошковую горелку маленькой мощности. Когда полноценная котельная, тогда проще - огромный факел в большой топке, зажигается один раз и горит очень долго. Маленькую наверняка надо будет оснащать рекуператором по входящему воздуху, как-то интуитивно чувствую, что маленький факел от пыли в холодном воздухе будет нестабилен, хотя может я и не прав. Да и по мере прогрева теплоносителя нужно снижать мощность (и расход топлива с воздухом), а он и так не велик. Оно конечно заманчиво, и уголь любой фракции подойдет (все равно молоть), и со шлаком проблем меньше (не спекается кусками, загаживая топку и мешая работе), большая часть золы улетит в трубу, а там ее можно поймать циклоном и "уронить" в бункер. Но боюсь что будет как с горелкой на отработке - чем меньше, тем сложнее добиться стабильности. Я конечно не теплотехник, по этому могу быть не прав, если кто в этом разбирается - пишите, тема интересная.
-
Так ведь разнообразие, оно всегда полезно глазу. Будем стараться и дальше . Как уже ответил Константин, котел полностью самодельный, твердотопливный. И может сложится ситуация, когда топка набита углем, который как следует разгорелся, а электроснабжение нарушилось (банально свет отключили, надолго). Источник бесперебойного питания конечно есть, но стопроцентной уверенность в его готовности нет - иногда выключают свет по паре раз за день, могут и пару дней подряд. Это может привести к ситуации, когда батареи не успевают зарядиться полностью, и время автономной работы сильно падает. Если в такой ситуации не "заткнуть" котел принудительно, он легко закипает (после того как остановился циркуляционный насос). А "затыкать" его надо именно физически перекрывая воздуховод, просто выключить поддув бывает недостаточно, такая ситуация возникает в узком диапазоне работы (топка полная и хорошо разгорелась, уголь крупный). Но хочется отсечь максимальное количество неприятностей, без экстремального фанатизма, по возможности доставая компоненты для автоматики с полки. Ну и автоматика избавляет от необходимости следить за котлом после окончания рабочего дня, можно набить топку под верх и идти домой, ничего не выйдет из под контроля. А вообще, это тоже временно, надеюсь со временем будет газ. Поставим нормальную заводскую котельную, и не надо будет ничего "изобретать".
-
Вчера решил заменить щит управления котлом, система автоматики немного разрослась и ей стало тесно в старом щите. А вызвано это появлением новой воздуходувки (ведь подача воздуха у нас принудительная), вот такой: А ей преобразователь частоты нужен, иначе на некоторых режимах подача воздуха будет слишком велика. Да и ПЛК я туда давно хотел повесить, так сильно удобнее. Опять все тот же процесс сборки на столе, только теперь компонентов немного больше, и ПЛК наконец-то встал на место: Немного бардака из проводов: Сборка закончена, смонтировал на место: Это конечно еще не конец. Нужен тормозной резистор не ПЧ воздуходувки (когда надо подбросить топлива останавливаешь ее, и ждешь несколько секунд прежде чем открыть дверцу), нужно проставить датчик температуры на обратную магистраль (пока не сильно критично, но второй канал измерительного модуля есть, так что можно и поставить), ну и стоит прикрутить к этому всему какую-нибудь web-scada (можно будет дистанционно смотреть, что там происходит, хотя это и не необходимо, но приятно). Датчик пришлось поставить двухканальный, других Pt100 не нашлось . А еще поставили заслонку на впуск (аварийную), котел изредка выходит на самотягу (при выключенном поддуве), а это лишает автоматику возможности его заглушить. Привод заслонки (саму заслонку не фотографировал) и rosemount'овский двухканальный Pt100 (если сравнивать его инертность с китайскими "бетонными" Pt100, то это небо и земля).
-
Это поправимо, у меня их немного больше, и я добавлю. Самое начало сборки. Попутно идет поиск компоновочных решений, и учетом последующего расширения (например добавления частотного преобразователя на приточную вентиляцию, и еще чего-нибудь): ПЛК на свет и вентиляцию? Почему бы и нет, пусть будет: Вообще-то на него много чего повесить можно, они очень хорошо расширяются, только успевай модули добавлять под растущие нужды . Ну и сборка ввода: Автоматический выключатель, общий контактор для автоматического или дистанционного отключения всего цеха (скорее мера предосторожности, чем острая необходимость), и маленькая ошиновка. Все готово, ставим ввод на место: На последнем фото видно маленький просчет - катушка контактора защищена автоматом, одним автоматом... а она на 400V, и ее надо защитить с двух сторон (ведь с двух сторон фазы). На фотографии Константина видно, что там поселились два предохранителя.
-
@tehsvar, развернуто пояснили, спасибо. Всегда думал что и в IGBT диод получается "побочно", в процессе производства, а оно оказывается не так. Буду знать.