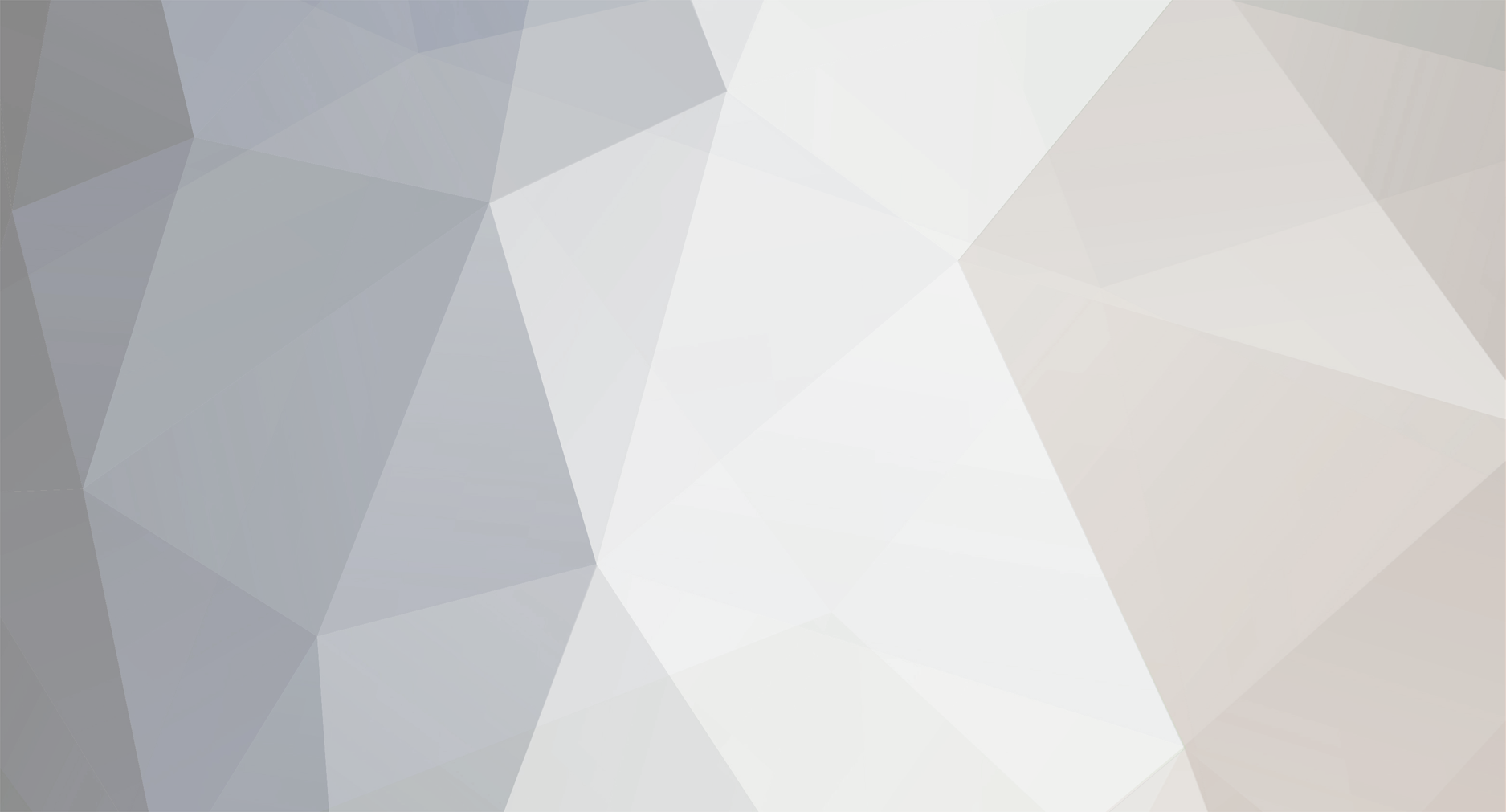
Spec
Участник-
Постов
459 -
Зарегистрирован
-
Посещение
-
Победитель дней
32
Тип контента
Профили
Форумы
Блоги
Загрузки
События
Весь контент Spec
-
Там же и БРИМы продаются. ARC 200 (ПВ-40%, 8кг, 20...200А)-- 7820 р., ARC 200B(220B, 20…200А, 8кг,ПВ-60%,форсаж дуги,10кг)--- 10500 р. ARC 160 / ARC 160A (BRIMA) (220B, 20…155А, 8 кг)-- 6950 р ARC 140 (BRIMA) (220В, 20...140А,8кг) ---------- 6200 р. Поговорите, может вышлют - почта, багаж, транспортная кампания..
-
Есть у меня "Дуга-318МА" 2000 г. выпуска. Хороший аппарат, но, говорят, в последние годы качество их снизилось. Подробности можете узнать, позвонив в Тулу "Интерсварка" (4872) 37-08-38, они занимаются их обслуживанием и ремонтом. Рекомендую присмотреться к недорогому инвертору из линейки BRIMA ARC. А чтобы правильно выбрать оборудование - сформулируйте задачу и для ее выполнения приобретайте оборудование.
-
-
Для подачи порошка используется кислород. В таких горелках обычно 2 инжектора - один для подсоса ацетилена, второй - порошка. В наплавочных горелках порошок идет вместе с горючей смесью, в горелках для напыления отдельно по центральному каналу.
-
Да, не на научном, но для выбора способа восстановления изделия эти цифры очень важны. Я даже перевожу их в кг/мм2, так понятней клиентам. И величина когезии важна, пористость, коэффициент трения. Никель, который Romich напыляет на опорные шейки распредвала, в парах трения не применяется, т.к. в отсутствие или ограничении смазки (что часто бывает при превышении усилия сжатия или малых зазорах) идут задиры. По поводу адгезии. Цифры примерно как у плазменных покрытий (рис.) Из своего опыта - штифтовая методика очень не точная, много влияющих на точность измерения факторов, и к тому-же трудоемок процесс изготовления образцов. Мы в свое время от нее отказались и перешли на клеевой метод. Возникла проблема клея. Дело пошло, когда нашли в Шостке пленочный, если не ошибаюсь ВК-20. Площадь образца увеличили до 20 мм (штифты Ф4). А зто по какой методике? Трещины. Их зачастую замазывают компаундами, запаивают, запыляют... Течь перестает, но трещина остается. Качественный ремонт предполагает полное удаление трещины с последующей сваркой. Даже раздека и провар на 3/4 толщины в значительной мере ослабляет конструкцию - остается концентратор напряжений. Вибрация при работе механизма, термические циклы сделают свое черное дело. При сварке чугунных блоков (да и др. деталей из чугуна) в околошовной зоне есть микронадрывы, которые Кастолин предлагает запаивать. Вот в этом случае ДиМет может оказаться полезным. Но "лечить" трещины только напылением (радиаторы - другая тема)с моей точки зрения нельзя. Оно, конечно, напылить можно, и даже верю, что герметично получится, но есть большой риск, что "благодарный" клиент на счетчик поставит или, пардон, морду набьет. Про масло... Мне вот не понятно, неужели так трудно помыть и обезжирить напыляемую поверхность? Тем более, что в процессе напыления на нее осядет и прилипнет к смазке абразивный порошок. Для меня, да и для многих других, подготовка поверхности под напыление - "священная корова". Я даже пальцем запрещаю прикасаться к подготовленной под напыление поверхности. Сегодня разрешишь - завтра он грязной рукавицей ухватится. А потом стоит - глазами хлопает - "Отвалилось покрытие..." Детонационно-газовое напыление. Когда я работал в Туле пушки не было, мы напыляли в основном плазмой, меньше газом и ЭДМ. Детонационная установка "Днепр" была у нас в Апатитах. Тоже обстреливали подложку вначале корундом (подготовка поверхности) затем нужным для покрытия порошком, но потом от этого ушли - ствол дороже. Я этот метод почему упомянул - очень напоминает ХГН (или наоборот - ХГН детонацию). Кстати, не понятно, почему ХГН выделяют из категории "газотермическое напыление". Ведь в процессе участвуюет нагретый газ. Детонация в принципе то-же самое, только температура и скорости повыше. Нагрев и разгон порошка осуществляется за счет энергии продуктов детонации газовой смеси (обычно ацетилен+кислород). Скорость распространения детонационной волны 2000 - 4000 с/сек. Температура в зависимости от состава смеси 2200-5500С, скорость полета частиц 600 - 1000 м/сек, коэффициент использования порошка 50-70%, скорострельность 1-6 цикл/сек. Адгезия покрытий (не всех, конечно) достигает 160 МПа, пористость 0,5-1,0% При всех достоинствах этого метода он имеет и крупные недостатки (нужна шумоизоляция, работа в автоматическом режиме в серийном производстве) Детонация хорошо пошла для напыления коленвалов.
-
-
"хорошая адгезия, высокая скорость, страшная сила..." Это не научные термины. Сколько в цифрах? На сдвиг или нормальный отрыв? Какая методика применялась? На каких подложках? От ВСЕХ, говорите. И от детонационного? А как быть с трещинами, которые Romich "успешно" лечит? Ее ширина от нуля до нескольких микрометров и она заполнена маслом. Это масло как удаляете? Здесь надо бы поточней - какой струей: воздуха, порошка. Если струей порошка - вопрос: что дешевле Ролс-Ройс (порошок) или Ока (ацетон, бензин)? А вот из этого вытекает еще два вопроса: 1. как определяется момент полной очистки напыляемой поверхности от масла? 2. Каковы данные по адгезии (если они проводились, конечно) покрытий, нанесенных на предварительно обезжиренную и маслянную подложку?
-
Бизнес план. Все просчитать, определить потенциальных клиентов, предполагаемый объем заказов. И осторожнее с кредитованием, можно "попасть" на бабки.
-
В принципе можно, если жить надоело... А если серьезно - не занимайтесь самодеятельностью с горючими газами, себе дороже.
-
Смотря какой гараж... Проволока может корродировать, омедненная корродирует еще быстрей. Медное покрытие имеет миркротрещины, в коррозионной среде в местах таких дефектов образуется гальваническая пара (медь-железо), что приводит к коррозии железа. Так что, если в гараже сухо - ничего с проволокой не будет. Но в случае длительных перерывов в работе - лучше домой.
-
Даже лучше. Некачественное покрытие медью осыпается, забивает канал горелки, проволоку клинит...
-
-
Прилагаю паспорт на горелку "Искра-6"Искра-6.djvu
-
Какой грансостав в мкм?
-
Интерсно, какой коэффицинт использования материала - сколько идет на деталь - сколько мимо? Хотелось бы знать мнения разработчиков и владельцев аппаратов. Материалы не из дешевых...
-
Это комплект "Термика" производства одноименной фирмы. Активно выпускала газопламенное оборудование на заре капитализма, сейчас этой фирмы нет. Я работаю с этой аппаратурой, вернусь домой - проконсультирую.
-
Вернусь на Север 15 января, все предметно обсудим. С Новым Годом!
-
С Новым годом, коллеги! Здоровья, счастья, хорошего провара и никаких трещин!
-
Привет, коллеги! Поздравляю всех с наступающим Новым годом! Я опять в Туле, доступ к компу ограничен, поэтому буду краток. Ребята, а не напоминает ли вам Эта тема "Горыныча"? Мне напоминает, только более спокойная, да и здесь есть предмет для обсуждения. Вернувшись домой я выложу свое мнение. Вадиму персональный привет и поздравления!
-
Да, держак получается боевой, но угольный электрод в него не вставить...
-
Электрододержатель лучше заменить. Для резки угольными электродами есть специальные резаки (воздушно-дуговая резка). Для резки по мелочам рекомендую купить режущие электрода ОЗР-1, они не дорогие.
-
Трудно удалить старые уплотнения. Лучше при плотно закрытом шпинделе 5 выкрутить сальниковую гайку 1 и, если шайба 2 полностью утоплена в корпус положить еще одну или под имеющуюся подложить еще одно пропитанное воском кожаное кольцо. Но сначала попробовать подтянуть сальниковую гайку. Все делать при закрытом шпинделе 5. Часто бывает, что вентиль перестает травить при откручивании шпинделя до упора.
-
Ацетиленовые вентили. Вентиль ацетиленового баллона изготовляется из стали. Применение сплавов меди с содержанием ее более 70% недопустимо, так как при контакте с ацетиленом возникает взрывоопасная ацетиленистая медь. Вентиль ацетиленового баллона (рис. 24, б) состоит из корпуса 10, редуктор к ацетиленовому баллону присоединяется хомутом, снабженным специальным нажимным винтом. Для вращения шпинделя 5 применяется торцовый ключ, надеваемый на выступающий квадратик хвостового шпинделя. Нижняя часть шпинделя имеет уплотнитель 6 из эбонита, который является клапаном. В качестве сальника применяют кожаные кольца 3, прижимаемые сальниковой гайкой 1 и шайбой 2. В резьбовой хвостовик вентиля вставляется прокладка из войлока 9, которая выполняет роль фильтра. Войлочный фильтр 9 и сетка 7 крепятся стальным кольцом 8. На боковой грани корпуса вентиля имеется кольцевая выточка, в которую вставляется прокладка штуцера 11, изготовляемая из кожи или другого эластичного материала. К этой прокладке прижимается входной штуцер ацетиленового редуктора.
-
N3-00-02 (никель, корунд)за 2478 р/кг? Тогда все понятно...
-
тор, я был не совсем внимателен, читая пост 15, цитата в нем не выделена зеленым, принял ее за Ваше высказывание. romich пишет, что ДиМетом напылялись распредвалы. И мне действительно интересно, какой материал наносился. На кулачки и опорные шейки. С тем, что качественно напылять можно и на более дешевом оборудовании - я согласен. Те же распредвалы прекрасно напыляются газопламенным пистолетом Mogul-U9. Через интернет ребята купили новые (видимо неликвиды) по 5 т.р. Стоимость комплекта (+ баллоны, 2 редуктора, шланги еще 8-10 т.р.) около 13-15 т.р.