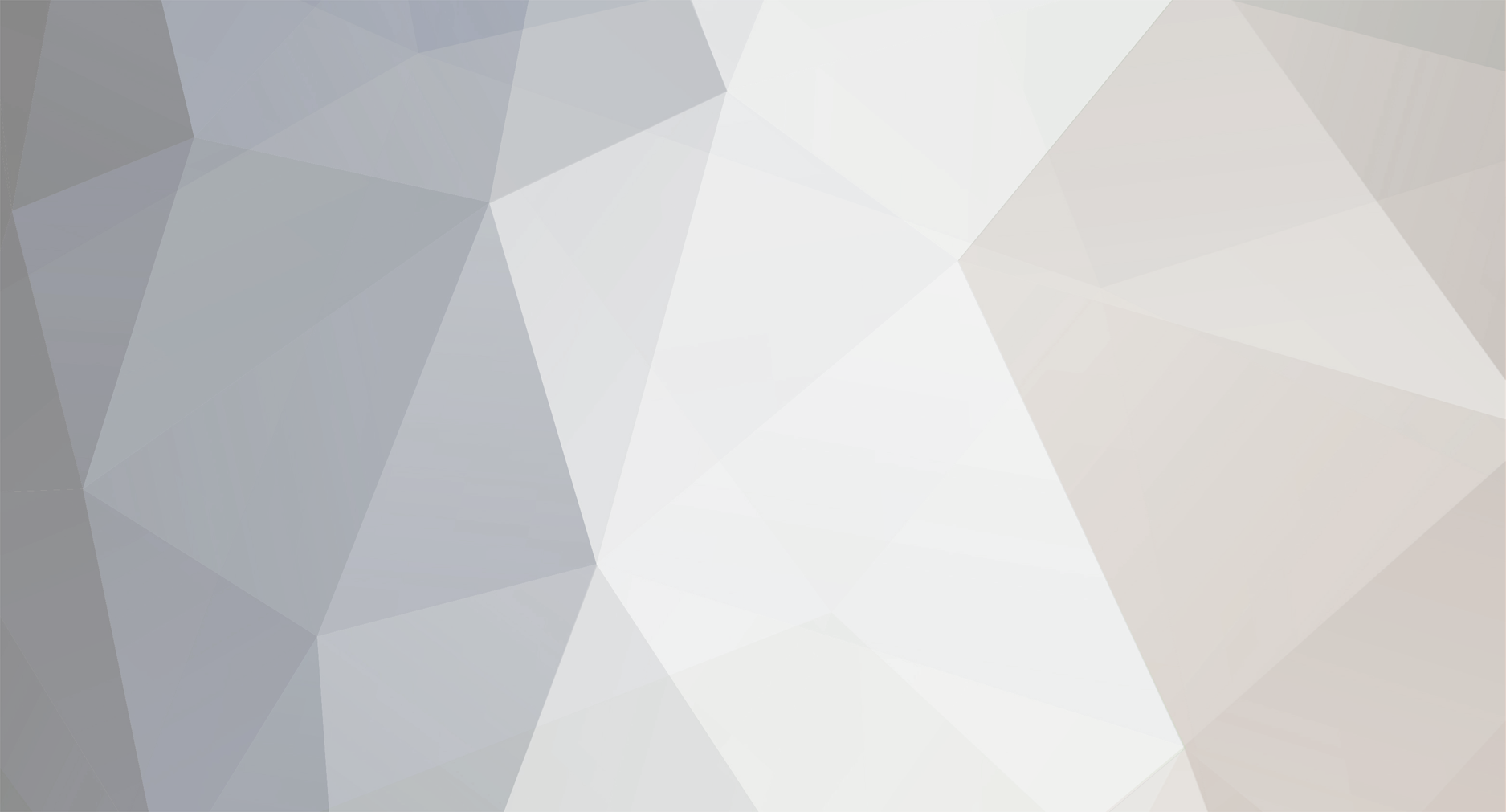
Spec
Участник-
Постов
459 -
Зарегистрирован
-
Посещение
-
Победитель дней
32
Тип контента
Профили
Форумы
Блоги
Загрузки
События
Весь контент Spec
-
Ну вот, все проясняется. Если бы сразу сказали, что речь идет о нанесении антикоррозионных покрытий ЭДМ я бы и спорить не стал. При ЭДМ не требуется предварительный подогрев, подготовка поверхности - дробеструйка либо зачиска абразивом. И толщина покрытия 0,25-0,50 мм. При ЭДМ в отличии от газопламенного, плазменного наппыленя частицы гарантированно расплавлены и нагреты выше температуры их плавления. Я напылял внутренние пояса насадок гребных винтов траулеров, так что с этим процессом знаком. Но больше 30 лет занимаюсь плазменным, газопламенным напылением деталей машин. И не только из литературы, по своему опыту знаю, как важен предварительный подогрев. Насчет передирания не согласен, т.к. много лет работал в НИИ, Академии наук и сам занимался исследованиями прочностных и других характеристик покрытий. Удивление вызвало как напылить небольшую деталь, не выходя за рамки 100С. Если исхитриться - оно конечно можно. Но зачем? И что это даст?
-
Некорректный вопрос! Можно предположить что это цилиндр Ф200мм длиной 200 м. Но это так, насчет точности формулировки. По существу. Не думаю, что вы напыляете всю поверхности детали. Но если принять во внимание, что подогрев до 200 - 250С повышает прочность сцепления примерно в 1,5 раза, то стоимость такой детали, цена сборки - разборки оправдает затраты на подогрев. А греть можно более производительными способами, чем горелка. Мне приходилось напылять вар шахтного вентилятора массой 18Т, посадочное место по подшипник качения Ф400мм. Грели 2 часа, потом нарезание разьбы, подслой, слой ПГ19М-01. Толщина слоя 8 мм (не ошибка). После остывания обработка в размер.
-
Насчет диффузии спорьте с Хасуем, Кречмаром, Кудиновым и другими исследователями. А пока ознакомьтесь с влиянием температуры подогрева подложки на прочность сцепления. Это тезис доклада Х Всесоюзного совещания ; "Теория и практика газотермического нанесения покрытий", Дмитров 1985. Обратите внимание на графики (стр. 43) зависимости прочности сцепления покрытий от скорости полета напыляемых частиц и температуры подложки. Автор (Хасуй) имел в воду оксидную пленку на напыляемых частицах.
-
Ошибаетесь!. Особенно в отношении напыления термореагирующего подслоя. Предварительным подогревом подложки осуществляется активация ее поверхности.
-
Из книги "Наплавка и напыление". Хасуи А., Моригаки О. Перевод с японского. Москва, "Машиностроение" 1985 г. с. 173-174.
-
Имеется в виду тело оператора? Или предварительный подогрев? При напылении, в зависимости от требования к детали нагрев может превышать 200С., а при напылении, особенно газопламенном способом, мелких деталей доходит до 300-400С.
-
Идеальная деталь для газопорошоквого способа. Небольшая, требующая прочной сварки без поводок. Но у Вас ее нет... ЦЧ-4 не рекомендую, поищите электрод с никелем, (одного хватит). ЭСАБ ОК 92.58, ОК 92-60 или МНЧ-2 Ф3мм. Х - образная разделка, фиксация в струбцине (тисках), 2 прихватки по краям. Дальше нагреваете стык до начала свечения и небольшим током - 60-70А варите попеременно с двух сторон. Высокий нагрев предотвратит возможные микротрещины, отбел и поводки.
-
-
Об этом много написано. Посмотрите: http://websvarka.ru/talk/index.php?showtopic=995, можно в поисковике задать "Газопорошковая наплавка", там тоже много интересного.
-
Тоже на расточку? Да, есть переносные расточные приставки. Но точность их выставления оставляет желать лучшего.
-
Думаю, что основное назначение ПП - наплавка, т.к. в лигатуру можно заложить требуемый состав. Диаметр ПП. 3,2 - не для всех подходит (оборудование), да и проблемы с хранением, влага, след. пористость при наплавке. Незначительное превышение температуры при сушке - разупрочнение оболочки, раскрытие шва, флюс в канале горелки, заклинивание. Для Ф1,6 эти проблемы не так страшны. Для сварки оправдано применение ПП, у кого нет СО2, И сварка на свежеи воздухе, где ветерок сносит защиту СО2. И - боритесь с пористостью! На фото изношенная резьба вала дробилки. 1 - наплавка; 2- нарезана резьба.
-
Потому, что речь об узле в целом. В данном случае разговор о наружной обойме подшипника, след. он монтируется в гнездо корпусной детали, чаще всего это рудукторы. Хорошо, для примера возьмем КПП. Для этого надо:1. Разобрать, промыть КПП. 2. Решить, каким способом восстанавливать поврежденное гнездо: а) расточить, напылить, расточить в чисте; б) расточить (что не всегда возможно, места мало), завтулить, зафиксировать втулку, расточить в чисте. 3. Найти подходящий координатно-расточной станок. 4. выставить коробку, чтоб не потерять ось вала, который будет установлен через подшипник в ремонтируемое гнездо; 5. Изготовить втулку, запрессовать, расточить. В случае напыления коробка снимается с расточного станка, устанавливается во вращатель (иначе качественно не напылить), напыляется, далее п.4. 6. Чистка коробки от стружки, пыли. 7 Сборка. Да, раз возникла такая тема, гнездо разбито. И не всегда сохранилась геометрия. Если пошли грубые задиры, то либо растачивать, втулить, либо замена узла. Но зачастую гнездо разбивает так, что появляется зазор 0,05 - 0,20 мм. Подшипник уже не сидит. Смещение от оси при этом составляет так-же 0,05-0,20 мм. Величина и направление большей оси овала гнезда определяется микрометрическим нутромером. Это место маркируетя. На обойму подшипника напыляется основной слой, затем на дуге примерно 140 град. без вращения наносится слой бронзы в один проход. Бронза - чтобы по цвету найти утолщение. Шкурение, сборка. Главное- при таком способе не ушла ось вала. А теперь прикиньте, сколько будет стоить клиенту ремонт с расточками, включая поиски подходящего координатно-расточного станка) и сравните с вариантом напыления обоймы подшипника. Стоимость напыления примерно 300 - 500р. Вот и получается, что дело не только в совести...
-
"полоска из жести" - это - "портянка". После напыления никаких обработок, напыление с небольшим припуском: 0,2 - 0,3мм, доводка шкуркой. При этом не нарушается ось подшипника. Прочность сцепления напыленного слоя 3-4 кг/мм2 на отрыв, на сдвиг больше, зависит от подготовки поверхности (обдув корундом).
-
Подшипник качения, напылена наружная обойма. Напыление во вращении, слой ложится равномерно, нагрев не превышает 150 С. Делали неоднократно, проблем не было.
-
Можно попробовать дробеструить обойму подшипника. Сам я редко использую дробеструйку, в большинстве случаев хватает резьбы.
-
Если говорить о сварке меди газопорошковым способом, то это скорее пайка. Хорошо подходят кастолиновские порошки 10180, 10186. Или прутковые припои, медно-фосфорные, серебряные. Медь варил дуговым способом вольфрамовым электродом в защитных газах (гелий, азот). Удивила масса детали, если ее нагреть до красна (выше 580 град С).тогда не то что варить, к ней и подойти будет "таааааак тяжелооо.."
-
Похож на карбид кремния черный, по фото трудно сказать точно. Для чего он на работе используется? Насечку на закаленный поверхностях дает?
-
Если примете вариант "кольцо", края впадины делайте с галтелями. Иначе оставите концентратор напряжений. Удачи!
-
И еще учтите, что вал изготовлен из углеродистой стали, при наплавке в ЗТВ будут закалочные структуры, вал впоследствии может лопнуть. Думаю, кольцо - оптимальный вариант. Какое давление на выходе компрессора? Каким оборудованием, материалами для напыления располагаете?
-
Перед изготовлением кольца задранный участок шлифуется. Наплавка электродом может вызвать деформацию, уж лучше автоматическая наплавка во вращении, но и в этом случае возможна поводка. Плазменные, газопламенные покрытия, электродуговая металлизация иногда применяют для восстановления коленвалов бензиновых двигателей, проблемы с дизелями, там выше нагрузки.
-
Тяжелый случай... Можно обнизить всю шейку и детонацией напылить. Напылять только зону задира - получите проблему мех. обработки (соосность). Если только прошлифовать в ремонтный размер. Напылить с оплавлением изношенный участок можно, но отпустятся прилегающие участки. Можно выточить кольцо из стали типа 40Х, разрезать на полукольца, установить в зону износа, заварить полуавтоматом по стыкам, прошлифовать.
-
Серега 63, скинь фотку дробеструйки и пистолета от нее. Черные гранулы могут быть и карбидом кремния черным. Абразивные частицы при соударении раскалываются, так что острые грани образуются автоматом. И пыль заодно. Дробь мы применяли марки ДЧК фракцией 0,5 -1,5 мм. ДЧК дает более развитую шероховатость, но не подходит для обработки твердых поверхностей. Песком работать не надо, вредно, да и толку мало...
-
Вчера сделали очередную рулевую рейку. Самофлюс 40-45 HRc, напылен до Ф29,5 и оплавлен. Токарная обработка Ф28,05. Зона напыления предварительно обнижена Ф27, резьба.