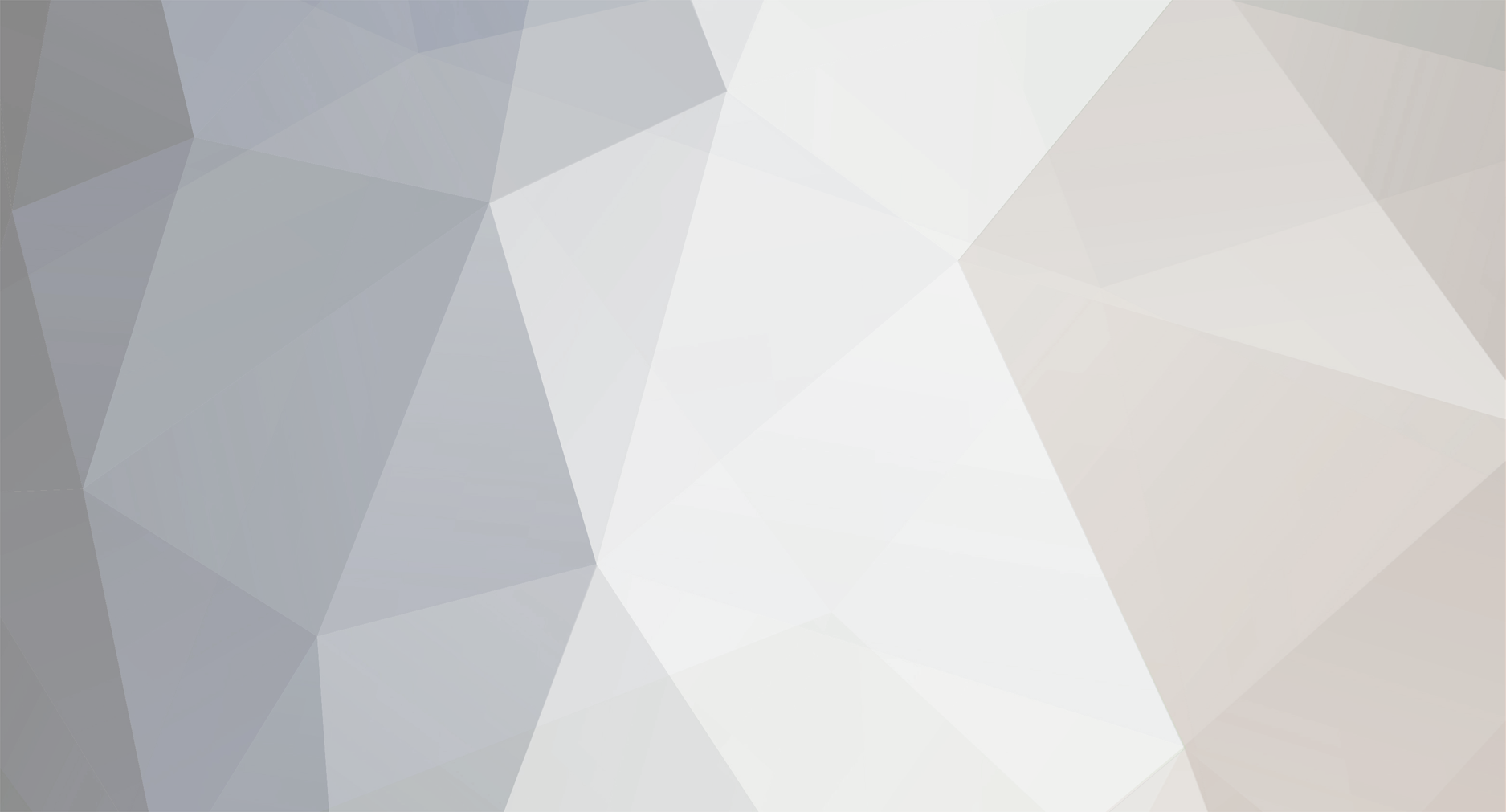
Spec
-
Постов
459 -
Зарегистрирован
-
Посещение
-
Победитель дней
32
Тип контента
Профили
Форумы
Блоги
Загрузки
События
Сообщения, опубликованные Spec
-
-
Вот и у меня руки толком не доходили. Работал только с отечественными ЭМ-14М (ручной) и ЭМ-17. ЭМ-14М неудобен, требует доводки. И процесс включения - выключения достает. Привод роликов подачи проволоки от турбинки. Думаю, буржуи придумали что-нибудь получше. ЭМ-14М выпустили в свое время много, можно в приличном состоянии задешево найти. И не обязательно с источником питания покупать (КДМ-2, КДМ-3). Хорошо подходит ВДУ-506 или другой ИП с жесткой характеристикой.
Ну, а если руки еще больше освободятся, рекомендую попробовать газопламенное напыление проволокой аппарат Топ-Жет-2. Я немного поработал с таким поработал. но потом плазма, газ, наплавка... . Им и цинк, алюминий пылить можно. Кстати, цинк - вредная для здоровья штука, алюминий дает хорошие результаты.
-
Правильно. Из кастолиновских можно еще применить подслои 25000, 29029 (Ni, Al, Mo). И бронзу 19850 (Cu + 10%Al + 1.5Fe).
Но я бы для восстановления штоков попробовал отработать технологию злектродуговой металлизации нержавеющей проволокой. Намного дешевле и быстрее.
-
Привет!
Обнижение 1 мм на диаметр, нарезание резьбы шаг 0,7 глубина 0,35, подогрев, напыление подслоя ПТ-Ю10Н, напыление бронзы ПР-БрАЖНМц. Припуск на обработку 1,5 - 1,8 мм на диаметр.
-
-
Можно.можно ли инвектором -
я бы хотел иметь для чугуна
Для эстетов, не имеющих финансовых затруднений, - электроды Кастолин 2-44 (сварка), Chamfer Trode 03/04 (разделка перед сваркой).
-
1
-
-
Горелка "Искра-2" (ацетилен+кислород), порошок - ПР-Н70Х17С4Р4.
-
2
-
-
-
С большой вероятностью после такой рацухи крышку в металлолом или в музей "Хитрости и смекалки". Крышки электродвигателей не только удерживают, но и центрируют ротор относительно статора. У них есть две соосные базовые поверхности, которые выполяются на токарном станке за один установ с достаточно высокой точностью. В данном случае оси этих поясков наверняка "поплыли", и окружности деформировались.
И уж если вставлять такие большие фрагменты из стали - почему бы не пойти дальше и сделать крышку полностью из стали (сборно-сварную), потом на станок, проточить посадочные. И электроды на "1500 тысяч" останутся.
-
1
-
-
Сварка чугуна - дорогое занятие с непредсказуемым (за исключением ГПН небольших деталей) результатом. Умные сварщики-ремонтники массово переходят на сварку алюминиевых сплавов. Расходы на материалы в 10 раз меньше.
Димон59. Посоветуйте родственнику поискать "живой" блок, можно б/у. Потом осознает свое счастье.
-
1
-
-
По описанию похоже на контактную конденсаторную сварку. Прижим, импульс тока при разряде конденсатора, охлаждение, снятие нагрузки. Электроды обычно медь с присадками.
-
1
-
-
Думаю есть. Если не пойдет - рассверлить всегда можно. На плазмотронах для напыления порошком диаметр канала сопла 6мм, для проволоки - 4 мм.
-
А если для порошкового напыления?
Для ГПН ацетилен из генератора подойдет, для газопламенного напыления нет.
1. Ацетилен из генератора влажный, в баллонах влага поглащается ацетоном.
2. Давление ацетилена для многих горелок газопламенного напыления должно быть стабильним 0,7 Кгс/см2
3 . Расход ацетилена при напылении достаточно высок 650 -1000 л/час.
4. Порошок дорог, экономия может дорого стоить.
-
2
-
-
схему сварочной микро пл. горелки
Не все так просто. Сварка - зажег дугу и грей, пока сварочная ванна не появится. При напылении все жестче. Имеем высокоскоростной поток горячего газа (плазмы) подаем порошок, который за микросекунды должен разогнаться и расплавиться. Причем скорость движения частиц очень сильно влияет на качество покрытия. В т.н. "микроплазменном" плазмотроне расход плазмообразующего газа низкий, иначе дуга погаснет. Скорость полета частиц тоже низкая. Можно пойти по пути уменьшения диаметра канала сопла плазмотрона - потеря в производительности.
Для работы в "сарае" главное - вентиляция. Напыление - довольно опасная для здоровья вещь. Я бы остановился на газопламенном напылении или ЭДМ.
-
Мы такие штучки называем "Диссертация".
Работал я с ламинарной плазмой. Красиво, тихо, мизерный расход плазмообразующего газа. Красота! Пока не подан порошок. Первый раз мы обалдели - порошок просто вываливался из струи плазмы. Покрытие удалось получить, напыляя сверху вниз (как при изготовлении Сникерсов). Покрытие получается рыхлое, когезия никакая. Оно и понятно, частицы падают не раэбиваясь. При увеличении расход плазмообразующего газа (даже незначительном) струя переходит в турбулентность, что соответствует обычной плазме для напыления. Расход газа растет, пятно увеличивается, все преимущества, заявленные в статье, пропадают. Кстати, ламинарный плазмотрон греет напыляемую деталь при одинаковой подводимой мощности сильнее, чем обычный.
-
1
-
-
А что такое "микроплазменное напыление"? Я бы охарактеризовал такие устройства как аппарат малой мощности. А сама плазма (газ в ионизированном состоянии) будет иметь не мении 6000С. Имея ИП небольшой мощности, газ в плазмотрон надо подавать в небольшом количестве, иначе дуга в плазмотроне погаснет. Отсюда - напылять оксид алюминия можно, но очень долго и муторно. Порошок же для этого надо брать настолько мелкий, насколько дозатор справится с его подачей. Горка порошка, насыпанного на плоскость, при наклоне плоскости либо течет, либо обваливается. Надо подобрать фракцию минимального размера, которая "течет". Мы напыляли от 30мкм.
-
@sedovskj, для фторопласта 250С
Оксид алюминия лучше применять в виде шлифзерна электрокорунда. Там наиболее однородные по размеру частицы.
-
Одно время моя супруга занималась защитой металлов от коррозии, в т.ч. и порошковыми красками. На деталь порошок наносился в электростатическом поле, потом оплавление в печи. Покрытие довольно равномерное по толщине, глянец, все ровненько. Автолюбители НИИ толпой со своими железками бегали. Горелкой вручную так не нанести. Когда меня задолбала УГПЛ, я совместил эти два способа: нагревал деталь, горелкой без пламени наносил фторопласт после чего оплавлял. Все очень просто.
-
Аргон-азотной , аргон водородной плазмой напылял детали размером от иголки и больше. У плазменной струи высокий градиент температур, так что микроплазма не требоварась
Вот и у меня в лаборатьрии бала плазменная наплавка, плазменное напыление (Ar+N2, Ar+H2, Воздушная, воздух + пропан), ЭДМ, газопламенное напыление, газопламенная наплавка, детонация, куча приборов. Разразился капитализм, Наши комнаты ушли под коммерцию, осталась комнета, где пушка стояла...
-
Ностальгия... Коммерция достала, хочется что-нибудь для души...Ребята, чтото вас в разнос понесло -
Я и говорю - площадка на подъемнике типа автовышки и турель - как гарпунная пушка у китобоев. Да, много приходилось напылять, наплавлять, варить. Наружные обоймы подшипников, валы, сопла ракетных двигателей коррекции траектории , цилиндры судовых дизелеей, типографские ножи. Жаль снимал мало, цифры не было. Два года доводили до ума защитные втулки титановых кислотных насосов. Вышли на керамическое алюмофосфатное покрытие. Стойкость выросла в 10 раз (30 суток против 3). 2 серебряные медали ВДНХ. Было это на закате СССР. Даже фторопласт напыляли (лопатка хлебопечки). И муфели водородных печей (жаростойкое покрытие , интерметаллид Ni-Al). Это я напыляю. Аргон-азотная плазма.
-
Дело хорошое (для вашего руководства и клиентов), но вредное для операторов. У меня в последние время специализация по восстановлению/упрочнению деталей машин. Это совсем другая история.
Дуговой металлизатор ЭМ-17 по паспорту обеспечивает 12 кг/час по Ал, что при толщине покрытия 0,5 мм составит 90м2/час. По цинку (плотность 7,1) - 40 кг/час.
-
1
-
-
Таким металлизатором я напылял насадки винтов. Что это такое мне хорошо известно. Помимо веса достает процесс "Пуск" - Стоп". И постоянный износ и последующая настройка направляющих для проволок. Потом это дело мы модернизировали. Согласен, что такой металлизатор далеко не "ручной". Если вы специализируетесь на больших поверхностях надо подумать о механизации. Что-то типа автовышки, на ней стационарный металлизатор ЭМ-17. Механизированное перемещение повысит равномерность покрытия по толщине.
Держать все это хозяйство в руках абсурд, надолго не хватит. Я подвешивал пистолет со всеми шлангами.
Про 2 катушки проволоки на операторе мне минчане рассказывали. Смонтировали их на поясе, повесили их как кольты, на оператора, долбануло его током, еле откачали.
Напылять внутри емкости - сродни самоубийству. Только в скафандре. Без мощной вытяжки через 15-20 минут видимость на нуле. Работа для приговоренных к высшей мере. Нужны роботы.
-
Да, электродуговая металлизация. Напыляете порошком? проволокой? Шнуром? Впервые слышу, что напыленное дуговым металлизатором покрытие может отслоиться. Мы много напыляли на стальные листы - отковырнуть не могли, не то, чтобы само отслоилось. И без подслоя, иначе пропадает эффект протекторной защиты. Напылили как-то на стальную трубку Ал. 0,2 мм, без пропитки. Повесили за окно. Несколько лет висела - никаких следов ржавчины. Производительность ЭДМ 20-25 кг/час. Простота, дешевизна процесса: сварочныв выпрямитель с жесткой ВАХ, сжатый воздух, 380В.
Я тоже против пропана в обычном (не свехзвуковом) газопламенном напылении. Только ацетилен. Во-первых в себестоимости покрытия основная доля - стоимость порошка. Скорость горения ацетилена выше, порошок летит с большей скоростью, а это важно. На заре капитализма занимался переводом горелок на пропан, приходилось через приставку сжатым воздухом разгонять порошок. И все равно качество по сравнению с Ац. снижается.
То, что буржуины щеки надувают, так к этому бизнес обязывает. Мол, должно быть как у нас, а как - не скажем, покупайте.
Если результат хороший и повторяемость на высоте, значит технология правильная.
Думаю, применяете пистолет типа TOP JET. Хорошая, кстати, машинка, вполне пойдет на пропане, есть обжатие и разгон сжатым воздухом.
Газопорошковое напыление
в Плазма и газ-резка, сварка, напыление
Опубликовано
Для регулировки расхода обдувающего воздуха.