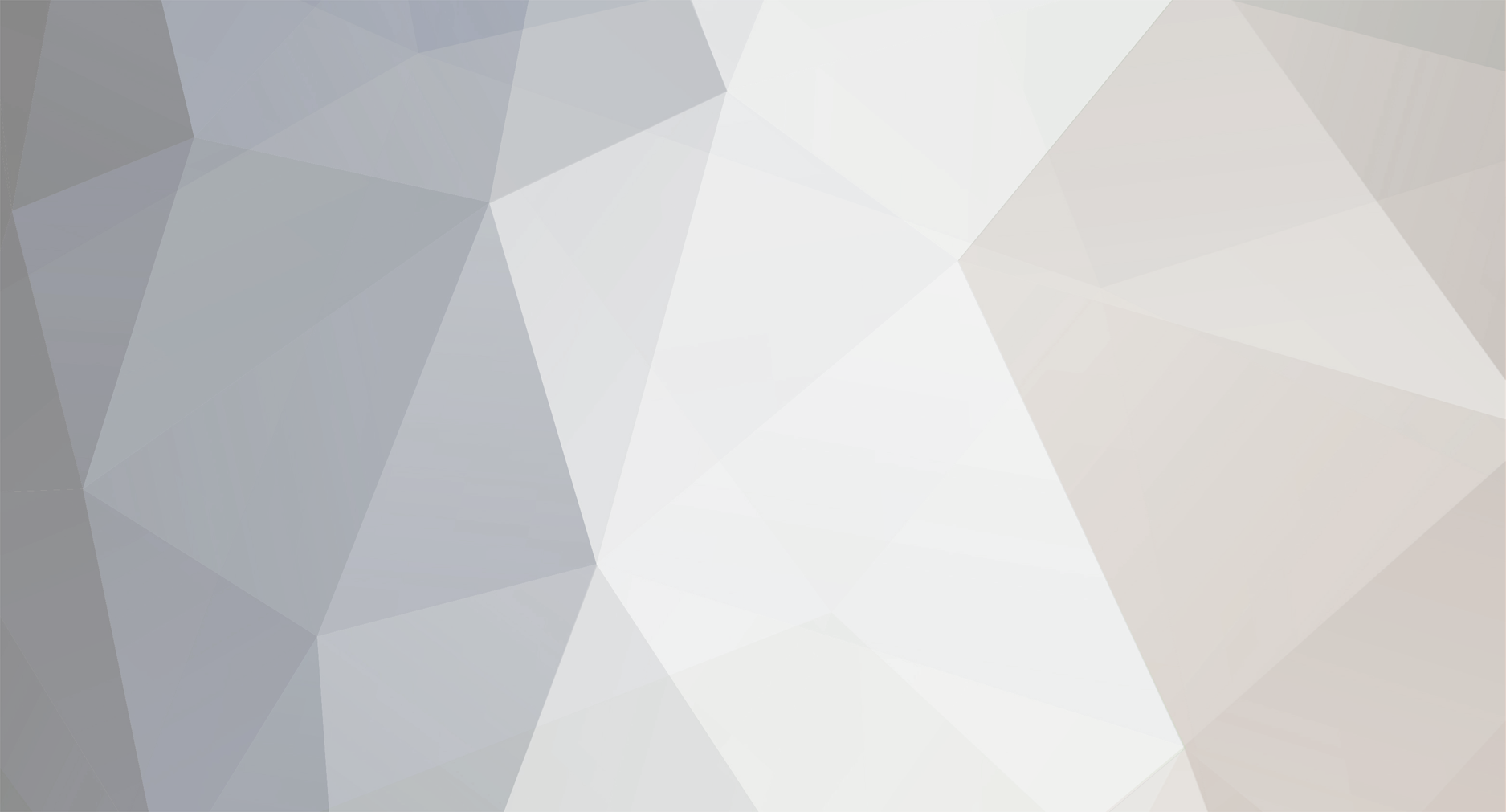
АндрОв
Участник-
Постов
119 -
Зарегистрирован
-
Посещение
Тип контента
Профили
Форумы
Блоги
Загрузки
События
Весь контент АндрОв
-
Отлично! Это под заказ или себе, вопрос к тому что следующий будет?
-
Вот здесь по шагам подробно рассказано как сделать на Arduino. Ничего сложного, в принципе по картинкам всё понятно, реально человек очень подробно всё написал, собираешь и работает. https://www.homemodelenginemachinist.com/threads/arduino-rotary-table-for-dummies.26744/
-
Именно эту плату и взял для этих целей, болтовня там как выбирать драйвер полезная, много ещё лишнего, а брать надо то что он использует в последний момент драйвер DMA860H ( в видео там всё есть у него под конец), как всё соединить у него там всё показано, ничего сложного, я ещё поставил зубчатый ремень и получилась передача 1/3 и при этом получилось 1,85 оборотов в минуту, а хотел ещё меньше. ( Шаговик взял вот этот https://ru.aliexpress.com/item/32798053451.html?spm=a2g0s.9042311.0.0.274233edIQzUcz) Можно взять вот такой редуктор под шаговик 23 https://ru.aliexpress.com/item/32817707616.html?spm=a2g0o.cart.0.0.45553c00KFd8KR И там уже получить ещё меньше, близкое к 0. Но я на этом остановился, сам знаешь как бывает, пришла в голову новая идея, может и соберу, так как практически всё есть уже. Теперь хочу вращатель с 350 патроном, у него проходное 100 мм... мне приятель привёз пол метра трубы толстостенной ф127/ф100 ( нашёл у себя в огороде, во как бывает ), теперь вот думаю каким путём всё это зафиксировать, варианты опять же разные. А на Ардуину ты зря катишь, я здесь собрал себе на базе Ардуины к делительной головке управление и вращение, в принципе пару вечером и всё можно освоить, а там возможностей куда больше.
-
Двигатель уж очень большой, какой мощности? Какие обороты? Бери не больше 1000. Редуктор с каким передаточным? У меня для этих целей лежит 1/110 и то думаю мало будет, хотелось бы получать снижение до 1,5 оборотов в минуту. Не проще взять шаговик, благо они сейчас не такие дорогие и к нему плату с регулировкой оборотов? Причём у шаговика как раз на малых оборотах большой момент. Щёточный узел можно взять от стартёра, если там вал позволяет, упрощает решение с креплением щёток.
-
Шестерёнки тоже лазером вырезаны и собраны в большую?
-
Шпилька может изгибаться, её ничего не будет, резьбу совать можно только елси добавить рычаг на ручкуи то маловероятно. Дело в том, что в этом месте нельзя без люфта, иначе оно будет закусывать, что хуже при работе. Затягивайте сильнее!
-
А посильнее затянуть не пробовали?
-
Высверливая я редко, обычно подгоняю под сварку когда рамы строю для багги, хотя высверливать тоже приходится иногда.... так вот редко когда то что высверлил куда то отваливается, по большей части в коронке затсревает.... возможно как раз потому что не боюсь ( так как всё равно когда раму делаешь куда кусок отвалится) и давлю до конца нормально, и он в коронку и залезает. Я не спорю, у каждого вероятно по разному получается... но иногда затрахаешься этот кусок от туда выковыривать, а ещё хуже когда забудешь его там и второй рез делаешь и его туда ещё и затолкнёт и разопрёт Кстати снимал видео про работу другого устройства, надо было показать его возможности, где как раз высверливал отверстия в трубе... видео само получилось нудное и длинное... на 14 минуте где-то как раз у меня застрял кусок и я его от туда выковыриваю...и так было с каждым куском, который я тогда высверлил. https://www.youtube.com/watch?v=2WTjzmvn3JI
-
Мусор/опилки будут сыпаться, а вот когда высверливаешь, этот пятак застревает обычно в коронке так, что его иногда вытащить то проблема... так что если магнит ставить то только ради опилок/мусора.
-
О чём я и писал, только если слабо затянуть, он через какое-то время может разболтаться, а самое вредное, что он разбалтывается в самый ненужный момент ... как-то когда ещё их испытывал, приехал на площадку к одной монтажной организации... когда они мне его принесли, всё болталось, тогда ещё шайба стояла...спрашиваю: А чего не затяните, оно же так не удобно?... А зачем, говорят, оно и так работает хорошо .... после этого стал затягивать сильнее и выкинул шайбу, но часто не получается его выровнять, как сильнее затягиваешь, так обязательно провалится в прорезь в раме, а сделать прорезь меньше, тоже не совсем правильно... вроде мелочь, но надо искать решение.... иногда решение простых мелочей тянется долго...пока его найдёшь, испытаешь... ну вообщем как-то так...
-
Это основа клемпа своей фаской проваливается в прорезь, раньше клал там шайбу, которая предотвращала перекос ( шайбу именно между корпусом и упорной пластиной не под гайкой), но эта шайба позволяла разрабатываться данному соединению, насколько бы сильно его не затяни. В результате испытаний пришли к мнению, что эту шайбу убрать, а если возникает перекос ( как у Вас) то на работу он не влияет в любом случае. Трещины на швах да косяк, буду проверять, их видно становится только после гальваники... данный узел работает на сжатие, этот узел вообще под вопросом ещё... тоже был добавлен уже в готовую конструкцию по причине увеличения диаметра зажимаемой трубы, жёсткости не хватало.... кстати о диаметрах и врезках, я бы не стал так однозначно про ограничения по размерам... может быть у сантехников это да, а у монтажников, у них вообще иногда запросы другие...часто спрашивают про 76 трубу и СТН60... СТН 60 тоже встаёт на 76 и можно врезаться, но это уже на пределе. Была задумка сделать маленький, только для врезок в трубы от 20 до 43 трубы, с ходом штока 20 мм ( для врезки больше не надо), зажим сделать регулируемый в пределах 25 мм, но посчитав затраты на изготовление и непонятный спрос пока отложил это проект "в ящик"... т.к. по стоимости ничего не выиграешь, все основные затраты те же, только работы в два-три раза больше и некоторые сложнее, а совсем упростить не получается или получается г__но... ну вообщем пока думаю что с этим делать.
-
Интересовался у пользователей СТН, это монтажные организации и сантехники, чаще всего они используют мощные шуруповёрты, и обороты маленькие и розетки не надо. В случае с СТН хорошо то что обороты низкие и крутящий момент большой.
-
В любом случае если бы делал бы то делал бы ЧПУ резку, с шаблонами заморачиваться стал бы по другому.... устанавливал бы шаблон вместо дрели на каретку, каретка всегда в одной линии, относительно длины трубы для места врезки позиционирование тоже контролируется на каретке. Плазма удобна, спору нет, но возвращаясь к публикации, в данном случае не применима была! - сварка невозможна по той технологии, как писал выше!Думаю на этом можно закрыть эту дискуссию в данной теме! - а зачем? если есть плазма? Я тоже куплю плазму, только денег надо накопить в десятки раз больше.
-
Примеры в студию, желательно с фото! Были такие примерки - неудобно. Для сверления использовалось устройство Ридгид для сверления труб с цепным зажимом, очень удобная штука кстати... но по скорости выполнения работ проигрывала, т.к. на каждой точке сверления надо выставить два положения, в ручную это занимает время. Всё универсальное хорошо когда надо сделать одну или две таких трубы, а когда разговор идёт о сотне труб, уже лидирует специальные приспособления. Если есть уже деньги - сравним по деньгам... плазма нормальная типа Хипотерма 150 т.р. уже в два раза больше по бюджету, я не говорю про лазер , а главное учимся читать вводные.. для кого писал о шаблоне... очень простое решение и главное очень удобное при серийном изготовлении сотни одинаковых деталей, когда труба небольшая ( не 6 метров) и всегда отверстия на одной координате во всех трубах... а когда 2 листа формата А1 и там мелким шрифтом координаты сотни труб по номерам и с размерами на каком месте сверлить, как в этом случае, сотни шаблонов? потом аренда склада шаблонов, учёт, лучше компьютерный с маркеровкой каждого шаблона и автоматическим складированием.... я думаю понятно к чему эти шутки. В последствии данное устройство переделали сверлить в трубе 12 метров, такая возможность у него есть, что ещё сократило время на работу... Кстати готов поспорить, что туже работу как вы сделали с помощью шаблонов я выполню быстрее на своей приспособе! вырезать такое отверстие коронкой быстрее чем плазмой...плазма в данном случае выигрывает по универсальности и расходникам.... хотя если учитывать стоимость самой плазмы то столько можно купить коронок что сверлить можно всю жизнь :-)) Плазма конечно вещь!!! Но я бы сделал для серийки что-то вот такое https://www.youtube.com/watch?v=-SYfcveqCx4 Я не претендую на гениальность решения, опубликовал аля может кому пригодится...
-
Лучше 22 мм, это под 1/2 трубу.
-
Какой будет винт, главное с каким рычагом?
-
В нотчере вал установлен в игольчатых подшипниках с сальниками, всегда использую японские NTN. А по направляющим-ездят втулки из полиацеталя, его там вполне достаточно.
-
С коронками работаю не первый день, вы абсолютно правы чем ниже обороты тем лучше. Есть такая же дрель но с регулировкой оборотов ( частотник к коллекторному двигателю не поставишь), я предлагал её с самого начала. но там смущала марка ( заказчика, для меня и так было понятно что это всё китай)... так вот сгорит, поставят с регулировкой оборотов. Изначально планировал поставить обычный 3-х фазный двигатель с редуктором и частотником, но это немного испугало заказчика и он попросил делать всё как можно ремонтнопригодней и доступней по частям. К тому же это бы увеличило срок изготовления и усложнило конструкцию. Если трубы не длинные ( метра по 4, длиннее не удобно уже становится), то делал другую штуку уже давно, ручную... принцип перемещения трубы, что бы сохранялась одна ось, очень простой. https://www.youtube.com/watch?v=VSBFPXLU2yU
-
Давно ничего не писал, а на праздники всегда есть время, но и за этот год особых изменений не было, кроме того что доработал чуть-чуть СТН с цепным зажимом, что он может зажимать трубу от 78 до 150 мм диаметром без ущерба и особого напряга. Ко мне в конце августа пришли люди из монтажной организации, которая занимается системами пожаротушения. Сначала купили СТН с цепным зажимом, для того что бы сверлить трубы 76 и 108, как я понимаю под разводку пожаротушения. Потом вернулись и попросили разработать устройство которым можно сверлить трубы длиной 5,25 ( что-то около этого) по одной оси. У меня мастерская маленькая, я там всего один работаю, и понимая какое это время займёт ( разработка, построение модели, изготовление и прочее) отказался... но потом, видимо поискав в других местах вернулись обратно.... договорились что особо быстро это не получится.... трудно, а иногда не возможно объяснить людям, что только разработка может занять достаточно времени до пилотного образца, я уж не говорю про сборку и изготовления самого пилотного образца, даже такого простого устройства... но тем не менее я за это взялся. Сначала пытался уговорить их сделать плазменную резку, и механика такого проста и опыт какой-то уже был, но как оказалось, что при изготовлении разводки пожаротушения нельзя использовать плазменную резку, как и сварку труб, трубы между собой соединяются специальными муфтами. Даже съездил к ним на производство и посмотрел как они это всё изготавливают, хотя основная цель визита была посмотреть уровень их автоматизации и самих работников... из чего в последствии исходил при проектировании того что должно быть. Задача была сформулирована так: простое, с измерителем длины, сверлить чем-то типа дрели или дрелью, что бы можно было заменить в случае поломки и было доступным. Как минимум месяц ушло до первых чертежей по которым можно было заказать резку деталей, реально ушло где то 60 часов чистого времени за чертежами, не считая тех вариантов, которые были отклонены по разным причинам. В конечном итоге была выбрана концепция обычной "сверлильной стойки" перемещающейся по направляющим вдоль трубы с фиксацией положения. К концу октября была собрана пилотная модель. Основа и направляющие трубы профильные 80х80, фиксаторы трубы с быстрыми прижимами для фиксации трубы в одном положении и фиксатор каретки на трубе такого же типа. Вот видео одного из первых испытаний, снято на телефон, так что качество не ахти. Так как мастерская у меня не большая, то модель была длиной 1,5 м, но для обкатки идеи этого достаточно. https://www.youtube.com/watch?v=lHtvNWijxGc Дальше надо было сделать "измеритель", этот вопрос стоял с самого начала при проектировании.... взял электронную рулетку, "разбил" её на две части, лазер поставил внизу каретки, что бы мерил от стенки, а монитор с управлением поставил к выключателю. Как оказалось, я не электронщик, задача не такая простая, но решаемая. Вот видео с испытанием с "электронной рулеткой" https://www.youtube.com/watch?v=Kiv-iAapOFA после того мы должны были полевые испытания, назначенное время всё время сдвигалось по разным причинам, за это время было решено ещё добавить простых линеек на одной из направляющих и указатель. Как оказалось не так просто найти линейки с права налево ( слева направо достаточно легко найти) , но так уж получилось и переворачивать всё не очень хотелось.. в конечном итоге нашёл 2шт. по 3 метра ( кстати взял последние две и продавец сказал что он даже не помнит что их покупали). Когда устанавливали у заказчика, то вначале получили порцию критики от исполнителей местных...начиная с того что можно купить риджит сверлилку для труб и она стоит всего 40 т.р. и как-то заставить её ездить вдоль трубы, причём она такая уже есть, вот только вдоль трубы ездит не очень и разметку надо сначала делать и прочеее... достаточно было ввести эту модель в поисковик на телефоне и убедиться что стоит она 120 т.р. после чего мастер понял что это больше чем его зарплата в несколько раз и замолчал.... но самое приятное, что когда каретка поехала, то всем это понравилось и уже окончательные операции по сборке производились всей бригадой. В частности наклейка линеек на 6 метровой трубе... Т.к. испытания прошли быстро и положительно, претензий не было ко мне, то было решено не демонтировать и оставить пока работать... так до сих пор и работает. От меня это достаточно далеко, поэтому только пару роликов снятых на телефон сами работниками, по моей просьбе. https://youtu.be/3NEprgGTeUE https://youtu.be/2B61C-6QQFA В принципе заказчик работой доволен, как было сказано: то что мы должны были сделать за 3 дня ( там сотни метров труб), просверлили с перекуром за 3 часа... таким образом скорость работы на этой операции возросла в разы...я предлагал ещё и другие операции немного упростить, но пока как я понял их это не особо беспокоит. Я сам остался не совсем доволен работой, когда уже всё было сделано, то работа круглых направляющих мне не нравилась, но переделывать не было не время не возможности на тот момент и было решено оставить так. Сейчас бы сделал ( и в принципе буду делать когда будет свободное время) на линейных направляющих с подшипниками и реечной передачей, так же хочу изменить зажим на каретке, немного модифицировать - усложнить.... тогда не было время играться, но когда время не давит, можно и более сложный сделать, с двухсторонним зажимом, а не как здесь с прижимом к площадке.
- 72 ответа
-
- 17
-
-
Даже интересно стало ... лезем не глубоко в указанный @kirogaz ГОСТ и читаем: "1.2 Конструкция деталей и сборочных единиц СРПС должна обеспечивать точность собираемых в приспособлениях металлоконструкций по 11-му квалитету" Хорошо бы собрать калитку или забор хотя бы по 15-ому квалитету - было бы идеально. Да и думаю при изготовлении рамки для калитки допустим высотой в 1,5 м трудно будет поймать 0,5 мм рулеткой у которой допуск 0.2 мм на 1 м ( ГОСТ 7502-98) Это я всё к тому, что знания великая сила, но применять надо к месту... а то получается как шутка не к месту...вроде и смешная может быть, но никто не смеётся.
-
Это я случайно зацепил, неудобно на процесс через телефон смотреть :-) А так сколько делал ещё не разу не цеплял... в принципе там не к чему направляйку делать, или надо тогда его стационарно устанавливать.... Когда обзор (это к ) сделаю все конструкции станет понятнее, оно очень небольшое всё и всё навесу получается :-) Там сам прибор весь в экране, а от индуктора уже не "фонит". Работал студентом на инженерной практике на ЗиЛе в лаборатории ТВЧ закалки 3 года, чуть-чуть представление имею с чем имею дело... главное что бы на пальцах ничего не было металлического типа колец, а то быстро очень разогревается, как видели... Если честно, то сам доволен как слон, пусть не дешево, но это решило то чего не мог решить в своей мастерской... закалка вещь нужная. Конструктор аппарата, сделал мне ещё 3 индуктора разных буду экспериментировать по возможности и потребностям.
-
От идеи закаливать горелкой отказался, всё же там хром и непонятно как себя поведёт при нагреве. Стал смотреть в сторону ТВЧ. Кого не спрашивал из знакомых не у кого нет...даже попробовать негде было. Посмотрел аппараты ТВЧ ( Китайского производства все)...цены ну уж очень кусачие, минимальный аппарат стоит как хороший сварочный, цены от 100 тыс. Увидел публикация одного человека на чипмейкере http://www.chipmaker.ru/topic/179752/ (он экспериментировал в строительстве таких аппаратов мощностью 2,5 Квт и обратился к нему за помощью...естественно не безвозмездной. В результате недолгого обсуждения он согласился собрать мне аппарат по новой схеме ( я в схемотехнике не силён, так что точно сказать не берусь что там было нового). Через два месяца я получил аппарат, аппаратик маленький, к нему прилагается насосик для циркуляции охлаждающей воды (если кому интересно сделаю обзор конструкции) ...аппарат полностью решил мою проблему, и теперь я могу закаливать хвостовики валов где место крепление дрели. Снял небольшое видео процесса на телефон. https://youtu.be/hFw8CWGZs9Y
-
Диаметр роликов должен быть от 6 до 10 диаметров трубы, в зависимости от толщины стенки и материала. Что бы особо не заморачиваться , если труба ВГП со стенкой 2,5 мм, то можно брать 8-9 диаметров трубы. Для примера для 20 трубы - 120 мм ( если ВГП то она скорее всего 21,3 мм), диаметр считается по центру/оси трубы. Ручей вытачивается в соответствии с диаметром трубы с допуском не выше +0,5 мм, что бы входила плотно. Можно ручей немного утопить на 2-3 мм, что бы стенки были выше центра трубы, но не обязательно. Если труба шовная, то гнётся швом внутрь гиба. Если стенка тоньше 1.5 мм, то во-первых надо увеличивать радиус гиба, т.е. ролик 10 диаметров трубы не менее, во-вторых лучше использовать дорн. Ну типа вот такого надо делать, эскиз для примера.
-
Естественно квадратное со скруглёнными углами - это и ежу понятно. И мы говорим о разных конструкциях с разными нагрузками, от этого зависит и что используем... в данном случае отверстия делались для сборки рамы для теплицы из профилей, как это относится к опорам ЛЭП?... не помню что бы опоры ЛЭП собирали из профилей... я никогда опоры ЛЭП не собирал, может и СНиП есть на такие опоры?
-
Я не против :-)) Просто рассказал как делают для облегчения сборки таких конструкций/соединений. Просто все привыкли сверлить - соответственно получают круглое, а когда штамп есть, то конструкторы рекомендуют оквадрачивать отверстия :-) Это не критика, просто делюсь чему научили...у тебя как всегда всё классно получилось Про заточку пуансона и пробивного стержня ( клапан используется?) можно подробнее?..интересно никогда не делал