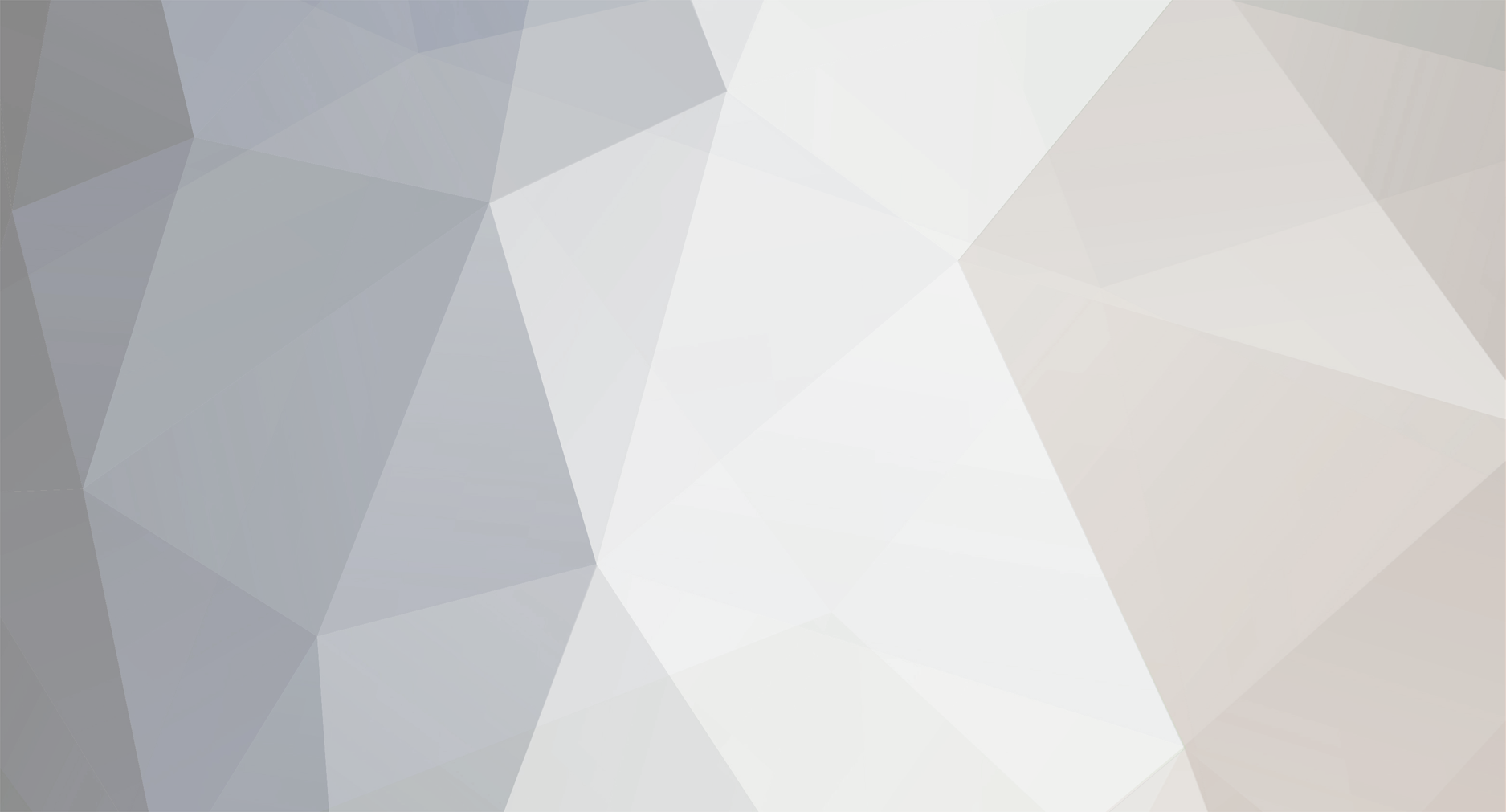
V1980
-
Постов
54 -
Зарегистрирован
-
Посещение
Тип контента
Профили
Форумы
Блоги
Загрузки
События
Сообщения, опубликованные V1980
-
-
Чем больше мы ставим вольтаж, тем больше объёма наплавленного металла, мы просто выбиваемся из допусков по ширене и высоте усиления, если уменьшить силу тока, то не получим необходимого провара и формирования усиления нижнего валика. Мы пробовали различные вариации режимов и увеличение вольтажа не даёт нужного результата. Может мы могли бы провести устную дискуссию!?
хорошо! можно по скайпу, маил отправил Вам в личку, т.к. не приветствуется засорение чата ненужной информацией
ну а насчет ширины шва и высоты усиления это как-то маловероятно по нашему ГОСТу
-
Теоретически Я понял о чём Вы. Напишу Вам режим для толщины 10 мм: зазор 2мм, DC 920A 33V, AC 500A 34V, Vсв=590mm/min, расстояние между горелками 20мм, высота обеих горелок от верхней кромки 30мм. Сварка с обратным формированием шва на меднофлюсовой подкладке. Расположение горелок Я описывал выше. Шов с обратной стороны нестабилен по высоте, бугристый, перепады высоты шва небольшие, но визуально очень заметны и непонятно почему возникают. Можете прислать мне электронную почту, пришлю Вам фотографии, чтобы было более наглядно. Думали, что это подкладочный флюс, но при испытаниях нескольких, выявились те же признаки. На установке с системой SeriasArc, такой проблемы нет. Мучаемся уже больше года.
даже по старым учебникам глубина провара при скорости до 40 м/ч 1мм на 100 А св тока, т.е. при вашем режиме для DC провар уже 10 мм, он просто прожигает первый валик. и еще для 900 А характерно напряжение около 40 В, при таком низком напряжении сварки давление дуги на св. ванну очень большое, им вы видимо ограничиваете ширину шва и заодно получаете требуемое усиление.
по режиму для АС согласен, он работоспособен.
-
Развод головок только усугубляет. Первая головка вертекально вторая углом вперёд на расстоянии 20-25мм. Есть фото,но они сюда не загружаются - файл слишком большой.
для 10 мм длина сварочной ванны 25 мм это не мало. получается что мощность 2-ой дуги настолько велика что переплавляет полностью шов от 1-ой дуги
с учетом того что при проваре больше 0,8 толщины металла идет фактически выпадение ванны соотношение токов у вас примерно 500/700-800 А по дугам
если так то 2 дуга просто выдавливает шов от 1 дуги вниз, так как он еще горячий. поправьте если я что-то не так понял
-
У нас сварка способом Tandem - две сварочные головки DC/AC проволоками 4мм. Обратное формирование не выходит при сварки двумя проволоками одновременно, сварка одно проволокой DC получается без проблем. Привезли флюс на испытания, который Вы посоветовали, в скором времени будем испытывать, думаем, что дело в подкладочном флюсе.
если у ВАС 1 проволокой получается, а 2-я нет причем тут подкладочный флюс тогда? головки в любом варианте разнесены вдоль шва даже если варите в 1 ванну. или я что-то упустил?
попробуйте разместить 2 электрод углом вперед, это снизит давление дуги на еще не до конца кристаллизовавшуюся ванну от 1-ой сварочной головки или используйте более длинный флюс и дальше отведите 2 головку
-
Добрый день! Я работаю на судостроительном заводе. У нас год назад установили линию плоских секций с порталом односторонней сварки способом Tandem - двумя головками 1-постоянка, 2-переменка. Уже год пытаемся подобрать режимы, но остаётся такая же нестабильность и дефекты (вытекание металла, подрезы, западания). Всё дело скорее всего в медной подкладке - неплотное прилегание + в некоторых случаях некачественная резка и сборка, но даже если всё в идеале, каждый раз получается что то новое. Не подскажите режимы и флюсы , которые вы используете. Могу тоже поделиться опытом, за год уже кучу всего перепробовал.
Не подскажите, будет ли толк и возможна ли замена медной подкладки на флюсовую подушку? + вопрос выше. Заранее спасибо.
вопрос логично разделить на 2 части:
- некачественная резка, т.е. отклонения в геометрии собранной секции. они не должны влиять на размеры шва в границе допуска отклонения геометрических размеров шва (объем металла в усилении шва должен превышать отклонение в размере фаски при резке)
по режимам позднее их надо искать.
кстати какая толщина листов?
-
Балки из какого материала? Если это их руукевский хвалёный RAEX 400, то брызги, даже в смеси аргон+СО2 - неизбежны (RAEX - высокоуглеродистая сталь). А насчёт таких швов, то как то, на заводе у меня был настолько толстый сварщик, что при приварке к балке двух косынок не мог нормально варить и наблюдать за процессом (может или маску или горелку к стыку поднести, а вместе - никак). Варил - на ощупь, не видя, что варит. На мой вопрос - что это за шов? отвечал, что он всегда так варит.
P.S. Покупаете самосвал или автоцистерну (Даже Вольво или МАН), не поленитесь хорошенько осмотреть надрамник и сварные швы снизу кузова или бочки (там где не парадная сторона). Правда теперь их часто шпаклюют.
раекс как и велдокс не высокоуглеродистые стали. там все дело в упрочнении и структуре металла. а то что брызги в смеси К-18 это факт и вообще они как-то интересно варятся
-
У меня нет опыта внедрения автоматических систем.
ИМХО:
Проблема 1. Для решения этой задачи необходимо иметь стабильные размеры геометрии сварной рамы для этого необходимо иметь: 1) Балки одинаковой геометрии (понятно почему); 2) Полностью автоматизированный процесс сварки рамы в одном и том же сварочном приспособлении (так как если сварка рамы производиться в ручную или полуавтоматом то неизбежно отклонение геометрии связанные с разным тепловложением и зачастую с разным порядком наложения сварных швов.) Только после этих мероприятий можно получить стабильную геометрию рамы и в последствии применять схему о которой вы говорите.
Проблема 2. Ситуация осложняется тем что получить стабильную геометрию секторов свальцованных из листа или из сварной трубы достаточно проблематично. Поэтому при сборке Вам гарантирован нестабильный размер зазора и процесс автоматизации в данном случае видимо возможен только при использовании саморегулирующийся системы (сами знаете сколько они стоят)
Все ИМХО.
а если использовать копир? т.е когда собран стык, опускаешь копир и головка в принципе при сварке корня шва по копиру запоминает расположение оси шва т.е происходит как-бы самообучение на следующих проходах добавляются при необходимости смещение головки от оси шва. правда здесь система сложноватая получается
-
Я не встречал, но ГОСТ 14771-78 один из самых крутых
, если добавить СП и СНиП то будет вообще атас! там все прописано межваликовые впадины, отклонения катетов и тп
-
1
-
-
Подскажите пожалуйста кто в России делает медную подкладку с канавкой , длина подкладки 6200 мм.
собрались варить лист продольно?
Вам проще сделать её секциями(на китайцах штатная ок 450 мм), заказать на любом маш. заводе
-
Приветствую уважаемые.Прошу у вас совета. как это соотношение выставить на этом редукторе.
сейчас смесь 92 Аr на 8 СО2, поверни праваую "крутилку" на 20 % и будет самое оно
. если горелка совковая можно немного увеличить расход и то это по обстоятельствам
чем больше аргона тем меньше брыгз, но и хуже ванна кипит (по ржавчине в шве будут поры)
-
1
-
-
В общем вот что получилось.
http://websvarka.ru/talk/public/style_images/master/attachicon.gif2014-04-19 14.37.23.jpg
это скорее всего струйный перенос (spray arc) если добавить скорость подачи проволоки, уменьшится вероятность подреза по стенке)
-
у вас скорее всего не подрезы а как бы утяжины.
а прожеги это наверняка неравномерность поджатия листов к подкладке, ведь у вас точечные прижимы (лапки, или т.п.)
лично по моему убеждению гораздо эффективнее для 1 сторонней сварки рукавная флюсовая подушка
-
1
-
-
@V1980, Вы про какую модификацию ВС-600 говорите?
самую древнюю с 3 пакетниками (80-х годов)
-
@Isperyanc, и я не варил. Мне вполне хватает заявленных ПВ:
http://websvarka.ru/talk/public/style_images/master/attachicon.gifS5024054-копия.JPG
Лишь иногда, в редких случаях, на одном источнике по очереди работают два-три сварщика и выключают сварку лишь для пересменки.
400-550А - 100% нужны для источников типа ВС-600, ВДУ-1201 (автоматической сварки в газе и под флюсом) при использовании в несколько смен на длинных швах.
к стати у ВС-600 ПВ 60% при 630А, у ВДУ-1201 100%. т.к заточен он под автоматическую сварку
просто на ВС неубиваемый диодный мост, в принципе на токах 400 А можно варить без вентилятора
минут 5, и у него еще нет защиты от перегрева
-
почему нельзя использовать падающие характеристики?
при миг/маг сварке конечно допускается к/падающая характеристика только для проволоки до 1,2 мм. а жесткая используется потому, что при случайном изменении вылета даже в относительно больших диапазонах позволяет обеспечить стабильность процесса сварки
-
1
-
-
Что нового? есть какие-либо успехи с прямолинейностью?
-
как и обещал выкладываю для господина morgmail фото внутренней стороны моего ЭСАБа и фото ручки моей горелки(вдруг ЭСАБ и горелки не выпускает)
этот Эсаб очень похож на TECMAN. а эсаб как и линкольн свои АСФ не производят гораздо проще купить качественный китай и поставить свой бренд, добавив 30% стоимости как минимум. на фубаге 9-13 примерно такой же светофильтр
-
@Технолог по сварке, у двигателей может сбиваться калибровка. Шаг двигателя не постоянная величина, она изменяется. Я сам толком не понимаю как там это все работает, вызывали специалиста. Но глюк был в том, что когда резали одну деталь, по одному чертежу, на одинаковых режимах - размеры получались совершенно разные.
Я почти уверен, что дело в тепловом расширении. Сам видел как загибает во время резки сталь толщиной 30 мм. А нержавейку резали узкими полосами по 200 - 300мм, они потом только на изготовление ятаганов годились
все правильно на плазменной резке 1 резак, а при роспуске кислородной резкой может и 8 резаков быть.
про шаг двигателя (сервопривод) даже если он и глючит
будут изменяться только линейные размеры (длина или ширина) в данном случае этого нет рез ведь прямолинейный т.е. одна из 2-х координат постоянна
-
1
-
-
еще вариант, лист не плотно прилегает к столу (т.е. лежит как-бы волной) система стабилизации высоты реза включена наверняка. кромка которая не плотно прилегает к столу соответственно будет иметь больший линейный размер.
как вариант попробуйте пригрузить лист к столу внутри обрабатываемой детали хотя-бы в 3 точках по длине карты
-
а в направлении перпендикулярном стыку подобные деформации есть?
кстати про перемычки верно подмечено, хотя наверняка отход минимальный, т.е особых бонусов от оставленных перемычек ожидать трудно
да и в качестве эксперимента можно прикрепить за плазмотроном распылитель воды и посмотреть на эффект
-
может попробовать резать листы на ванне с водой? тогда теплоотвод от места реза будет более быстрый.
-
@Spider2, некоторые уже пробовали дуть на св. ванну воздухом, пропаном из зажигалки... В подаче пара Вы будете первопроходцем (по крайней мере на этом ресурсе)
в одном институте разрабатывали технологию наплавки деталей в среде пара, а для сварки применять его для сталей думаю проблематично так как пар диссоциирует на кислород и водород(источник пор). про углекислоту в пищевой допускается гораздо большее содержание воды
-
Помогите пожалуйста! В контору купили трактор для автоматической сварки под флюсом компании Линкольн модель Крузер, и теперь хотят чтобы я на нём начал варить, а я его впервые увидел когда из коробки достали! Помогите пожалуйста, подскажите хоть примерные режимы сварки для разных толщин металла: сталь от Ст3 до 09Г2С толщины до 20мм. Что-бы хоть какие-то цифры были а там я уж по факту посмотрю и подгоню более конкретно! Скажу ещё что трактор просто купили, а на обучении управлением сэкономили, сказали что сами разберётесь!
по этой теме много инфы.
для проволоки 3 мм (флюс ОК 10.71, АН-60) все швы 2 сторонние
толщина: 4 мм, ток 300-340 А, напряжение 26-28 В, скорость сварки 0,75-0,95 м/мин (на стальном листе) провар ок 3 мм
6-8, 340-450; 26-29; 0,70-0,84; провар 3-4 мм
-
Да обычная третья сталь идет.
Кстати, нагревать перед сваркой тоже пробовали,только руки все пообжигали пока варили.
для проволоки 1,2 корень я бы варил с подачей 13 м/мин и напряжением 28-30 В. для 1,6 ок 9 м/ч напряжение 32-36 В. положение нижнее (ротор вертикально) сам варил под просвет балки со швом Т8 проволокой 1,6 мм на ПДГ-508 на таких режимах подача 2-3(6)ролик д. 50 ммматериал балки 10хснд стенка 20 мм лафет(полка) 32 мм технология простая: корень, кантовка корень, заполнение 2 прохода, заполнение 2 прохода со стороны 1 шва
-
1
-
Длина и сечение сварочного кабеля
в Ручная дуговая сварка — ММA
Опубликовано
про потери тока в кабелях, Вам в помощь закон Ома для участка цепи. 16 мм кв. по моему мнению достаточное сечение для того чтобы варить не только 3, но и 4. вместо штатного 25 кв кабеля поставил 16 кв. длинной 5 м, при ПН ок 60 % температура кабеля на 10 градусов выше окр среды.