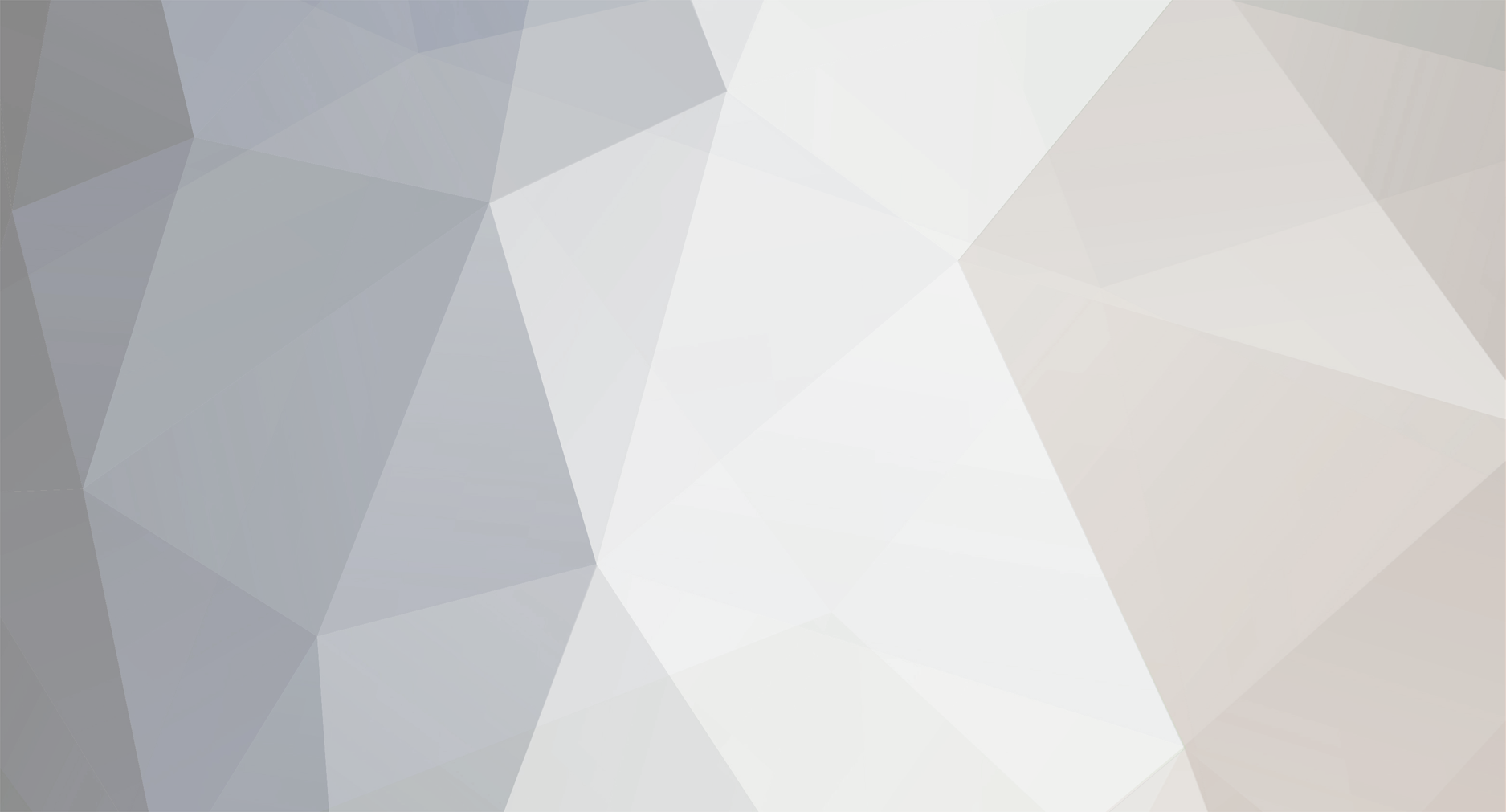
Reankor 2002
-
Постов
915 -
Зарегистрирован
-
Посещение
-
Победитель дней
44
Тип контента
Профили
Форумы
Блоги
Загрузки
События
Сообщения, опубликованные Reankor 2002
-
-
Где то должно быть видео, найду покажу, там видно скорость напыления.
-
Это я , напыляю внутри трубы, в г. Чехов , трубы ТЭЦ , диаметр от 4 до 6 метров.
http://i.piccy.info/i9/d501649e631d67d24ecdd9035dc4d39d/1391880761/15531/568570/10.jpghttp://i.piccy.info/a3/2014-02-08-17-32/i9-5889291/512x288-r/i.gif
В частности, силами НПП «Ремост» при авторском надзоре ИЭС им. Е. О. Патона выполнены металлизационные работы на таких объектах:
несущие балки Воздухофлотского путепровода в г. Киеве (4000 кв. м., Zn-Al покрытие);
ортотропная плита Южного моста через р. Днепр в г. Киеве (10 000 кв. м, Zn-Al);
резервуары для хранения авиационного топлива объемом 3 000 куб. м в г. Гостомеле Киевской области 2 резервуара, (Zn-Al покрытие);
газоотводящий ствол дымовой трубы высотой 320 м диаметром 11,4 м на Углегорской ГРЭС в Донецкой области (15 000 кв. м, Ni-Cr покрытие);
металлоконструкции гидротехнического оборудования для ГЭС «Аль-Вахда» (Марокко) и «Исфаган» (Иран) на Чеховском заводе «Гидросталь» Московской области (24 000 кв. м, Zn покрытие);
дымовые трубы районных тепловых станций для г. Москвы на Чеховском заводе «Гидросталь» (40 000 кв. м, Zn покрытие);
несущие металлоконструкции крытого паркинга для центров оптовой торговли «МЕТРО Кеш енд Кери Украина» на ЖЗОК (5 объектов, 10 000 кв. м Zn покрытие). -
Из защиты МИОТ
с подачей чистого воздуха, вытяжка , улитка 6-ка, пустые ведра в люк затягивает...
Все это напылялось вот такими аппаратами...
http://www.ua.all.biz/img/ua/catalog/436125.jpeg
УГПН-005 , эта техника решает такие вопросы на раз, после моих доработок, до 60 м/2 в час, по ТТХ завода 8-12 м/2.
ЭДМ такой скорости добиться не возможно.
-
- Популярный пост
- Популярный пост
РДС 3/4 труба на газ , ну весь монтаж котельной тоже мой.
http://s004.radikal.ru/i206/1402/0d/693148d6847b.jpg
Монтаж узла учета , счетчик G-160.
-
10
-
- Популярный пост
- Популярный пост
Индивидуальное отопление, врезка в газ и установка счетчика под давлением, РДС
http://s018.radikal.ru/i507/1402/0e/2742489118c3.jpg
Сварка 15-ых труб , подключение котла.
http://i024.radikal.ru/1402/0b/f41323beaf8a.jpg
Подключение котла (изготовили по заказу) нержавейкой, газ, вода, отопление...
http://s018.radikal.ru/i508/1402/3d/2c3394fd441a.jpg
Тоже РДС.
-
10
-
Производительность ЭДМ 20-25 кг/час. Простота, дешевизна процесса: сварочныв выпрямитель с жесткой ВАХ, сжатый воздух, 380В.
Только вот когда это все на столе , то удобно, а если в 1000 кубовой емкости - это писец...
Пистолет ЭМ-14М - Почти 5 кил весу, кабеля + шланг, при 500 амперах кабеля становятся дыбом, а дальше на спине ранец с двумя катушками проволоки кил по 15 , которая по боуденам (под мышкой) идет в пистолет ... и того кил 15-25 в руках, сил хватает минут на 10-15, на полу, про напыление стены вошпе молчу... в общем страшное зрелище... прикопали мы его и взяли УГПН-005, пистолет грамм 800, длинна шлангов 25 метров, даже аппарат тягать не надо.
-
ЭДМ это электро дуговой метод? Нет мы напыляли именно газопламенным методом, электро дуговое как раз ллучше подходит для ремонта деталей, чем как антикор, пористость (плотность ) у газопламенного больше 15-30 %, а у ЭДМ 5-10%, при больших площадях и толщинах начинает отрывать само себя
Насчет передирания не согласен,Я имел ввиду, что наши институты передрали (зацепили) технологии кастолин, и начали их развивать по своим направлениям, у буржуев ник то не напыляет пропаном, только ацетилен, а в Патоне решили что это дорого и построили всю технологию на пропане, вполне успешно и применяемо, но металлы свыше 800 градусов плавления лучше в ацетилене, и в нем порошок избавляется от окислов.
Кстати когда напыляли под Москвой, приезжали к нам представители ихнего института, сказали что у нас все не правильно, на вопрос почему? - потому что не как у нас, а приемку работы делали французы "Веритас" - их все устраивало... Москвичи взяли наши образци , через неделю приехали и сказали что делаем все не правильно , но результат (образцы) , правильные и отвечают требованиям...
-
Все это напылялось вот такими аппаратами...
http://www.ua.all.biz/img/ua/catalog/436125.jpeg
-
Все эти книги давно прочитаны и переписаны, первоисточник фирма Castolin, с них драли все, и Московские институты и институт Патона, в Патоне этим занимался отдел Максимова и Зеленина (я в нем отработал 12 лет), самое главное и эффективное , это шероховатость насечки, должна быть 40-60 rz , и тогда отпадают все надобности в подогреве , адгезия на пропане 350-400 кил. на пятачок 2.5 см. на ацетилене выше, цинк и алюминий нагрев поверхности 40-60 градусов
По поводу размеров, это трубы ТЕЦ в Москве, гидроэлектростанции по всей планете, общей площадью больше 60 000 метров квадратных.
Плотина «Аль-Вахда» гидроэлектростанция, напылял в течении 4 лет, 24 000 м/2. Материал цинк , толщина 150-180 микрон.
Большинство работ проходило на заводе "Гидростальконструкция" в г. Чехов под Москвой.
-
Нет в напылении и близко диффузионного сцепления. Это старый миф , который впихивали в уши для пущей важности.
А оксидная пленка убирается дробеструйной, на стали она восстанавливается через 8 часов, позже уже не рекомендуется напылять.
-
шариковой ручкой
http://i.piccy.info/i7/9bab38e2c67672263dfabae798923657/4-57-1126/62529246/DSCN5233_800.jpghttp://i.piccy.info/a3/2013-04-13-18-22/i7-4432441/554x771-r/i.gifВ каждом шарике своя картина...
http://i.piccy.info/i7/080741049c0cfbc025bd63145c87d9e0/4-56-546/22189010/DSCN4952_800.jpghttp://i.piccy.info/a3/2013-03-09-20-48/i7-4247196/563x758-r/i.gif
-
9
-
-
-
Напыление держится за счет механического сцепления, нагрев только вредит в этом.
Как вы себе представите подогрев детали в 50 тонн и площадью 400-500 м/2.
-
-
@G_Kar, 14.
-
-
- Популярный пост
- Популярный пост
Дочка рисует...
http://i.piccy.info/i9/fb0a4963c0c8c2559dda7a2434a8343d/1391803249/89798/568570/Yzobrazhenye_1454_800.jpghttp://i.piccy.info/a3/2014-02-07-20-00/i9-5885244/530x800-r/i.gif
http://s43.radikal.ru/i101/1402/ec/4d61b191076e.jpg
http://s018.radikal.ru/i518/1402/e4/dbbf8f51556d.jpg-
12
-
Имеется в виду тело оператора? Или предварительный подогрев? При напылении, в зависимости от требования к детали нагрев может превышать 200С., а при напылении, особенно газопламенном способом, мелких деталей доходит до 300-400С.
Нет. Если так происходит , то это не правильно...
-
Reankor 2002 сказал(а) 04 Фев 2014 - 10:29:Наверное имеется ввиду этиЭто пескоструи
Это и дробеструи, а при напылении, тело не должно нагревается выше 100 градусов.
-
-
@Сварик,Дипломная работа по слесарке в бурсе, станина строгального станка, 2 месяца, втроем, довели до 15-20 точек...
-
Ну тогда может его надо было сделать, (узел с камнем) свободно висящим - под своим весом, тогда как то более менее компенсируется износ камня.
Но в любом случае шлифование это есть первоначальный процесс (грубая обработка), а потом уже применяется шабрение.
-
Есть для охотников балаклавы флисовые, очень удобные и теплые.
-
Не, я о том что от начала движения и до конца , камень меняет размер, а значит и поверхность также.
Газопорошковое напыление
в Плазма и газ-резка, сварка, напыление
Опубликовано
Да зверь машина , но его место на токарном станке, за время работы в институте, напыляли все что в голову приходило, и подшипники бронзовые восстанавливали, и ролики для овсетной печати НГН-9 нержавейка, и капрон в хим ванны, контакты медные, валы - колен валы и т.д. и даже для КБ Сухого напыляли фонари для истребителей - на оргстекло напыляли метал для громоотвода, формы бутылочные, в общем сразу все и не упомнишь.