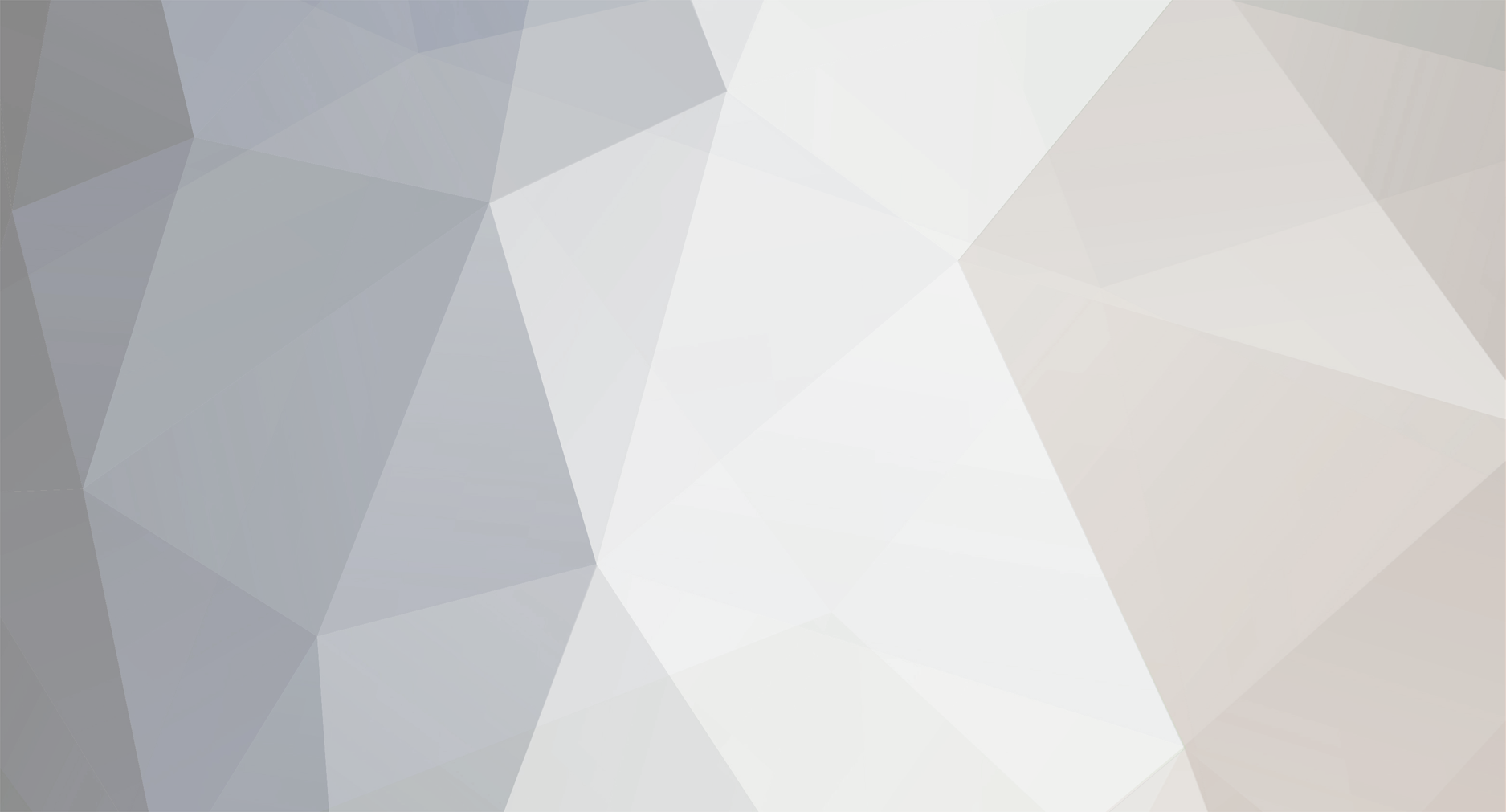
Технолог по сварке
-
Постов
20 -
Зарегистрирован
-
Посещение
Тип контента
Профили
Форумы
Блоги
Загрузки
События
Сообщения, опубликованные Технолог по сварке
-
-
Доброго времени суток, форумчане!
Возник вопрос выбора сварочной проволоки, аналога СВ-08Г2С, производства Кореи и Китая. Выбор стоит между Hyundai, Kiswel и Grovers. По характеристикам наплавленного вроде идентичны, по качеству пробных катушек тоже. А как в промышленных масштабах себя показывает? Кто пользуется проволоками данных марок, дайте свои отзывы.
Еще интересует реальное происхождение катанки, не на одном ли заводе все катают? У кого есть инфа, подскажите.
-
У нас сварка способом Tandem - две сварочные головки DC/AC проволоками 4мм. Обратное формирование не выходит при сварки двумя проволоками одновременно, сварка одно проволокой DC получается без проблем. Привезли флюс на испытания, который Вы посоветовали, в скором времени будем испытывать, думаем, что дело в подкладочном флюсе.
Надеюсь, что это Вам поможет. А у кого заказывали флюс (если не секрет)?
-
У Вас установка для сварки Tandem ом?
Нет! У нас установка Oerlikon, выполненная под заказ (не стандарт). Сварка одной проволокой.
А у Вас сварка ведется двойной проволокой?
-
Спасибо за совет. А что и как вы варите на медной подкладке?
Варим листы в карту из 09Г2С и 12Х18Н10Т. У нас специализированная установка.
-
Я использую обычные дисковые фрезы на болгарку, толщиной 2-4мм в зависимости от толщины. Щетки не помогут, т.к. в корне алюминия вся "грязь" собирается и оксиды.
-
...... в данный момент занимаемся поиском специального мелкодисперсионного подкладочного флюса, т.к. не получается именно нижнее формирование......
Могу посоветовать флюс Oerlikon марки OP10U. Очень мелкая фракция. На протяжении 3 лет используюю его на предприятии для сварки на флюсомедной подкладке. На сегодняшний день ничего лучше найти не удалось. Подходит как для "черных", так и для нержавеющих сталей. Единственный минус - высокая стоимость и мало кто поставляет.
-
Прижим, как я понял - гидравлика. Поэтому если сам метал не волной, механически деформированный, то гидравлика его выравнивает. Дефекты сварки могут быть по разным причинам. Т.к. это сварка под флюсом, то впервую очередь надо отталкиваться от качества самого флюса + его срок годности и условия хранения. Насчет корня шва, то надо применять специальный флюс для корня шва, т.е. в ложбинку замыпать другой флюс нежели чем с верху.
Сам лично пробивал 12мм без разделки. 15-16, может и получиться, но надо и флюс знать какой приенить и диаметр проволоки не 2.4 и т.п.
Сам применял флюс унифицированный, т.е. и для корня и для верха. Но когда режим подбирал и не попадал с режимом то флюс прилипал так, что ни зубилом и кувалдой не сбить. А качественный и нужный флюс это почти 50% качества шва.
Дело в том, что флюс для крня и основной действительно разный. Сроки хрнения в полном порядке. Режимы, на мой взгляд, подобраны оптимальные (подбирали совместно с немцами в течении полугода). Похоже, что все дело в медной подкладке, а точнее в качестве поверхности канавки. Вот единственный вопрос остается с периодически возникающими подрезами в крне шва, даже на новой медяшке. Каковы все-таки их причины возникновения я понять никак не могу.
Пробовал регулировать и скорость, и силу тока, но результата получить никак не получается. Подрезы конечно очень не глубокие, но мне это не совсем нравится.
-
Как мне кажется не очень удачный выбор технологии сварки для таких толщин. Какова длина швов?
Длина швов от 2 до 6 метров. Чаще в районе 5 метров.
-
Если действительно так, тогда надо смотреть на то, что периодически меняется. А это сварочные материалы. 1.Проволока порошковая небось, т.е. наполнение её может менятся, я бы здесь поэксперементировал и проверил. 2. Флюс, его прокалка. Дефекты то обычные и причины должны быть стандартные, скорее всего. Кстати как с скачками напряжения цеховой сети? По прожогам я всё-таки бы присмотрелся к прижатию подкладки.
Проволока применяется сплошного сечения. По прижатию хороший вариант, обращу особое внимание. Спасибо.
-
Что есть флюсо-медная подкладка, это "ползун"?
Нет, это не ползун. Флюсо-медная подкладка у нас выполнена в виде медного бруска прямоугольного сечения длиной 6200мм. Эта подкладка имеет простроганную канавку, в которую в последствии засыпается мелкодисперсный флюс, участвующий в защите и формировании корня шва.
Подкладка водоохлаждаемая (в ее теле расположены трубки, по которым циркулирует вода).
-
-
Варим 09Г2С 3мм и 4мм, а также 12Х18Н10Т тех же толщин. Проволоку пименяем Oerlikon, для сварки 3мм диаметром 2, а при сварке 4мм диаметром 2.4. При сварке периодически возникают прожоги, а иногда непровары. Режимы и сборка при этом не меняются, а дефекты то возникают, то нет. Вот основная проблема!!!
-
Особенности?... Ну например равномерное распределение флюса по длине, одинаковое прижатие подкладки. Но в общем ничего "особенного" нет, обычная сварка под флюсом.
Я сначала подумал, что очередному студенту нужен реферат по теме: Сварка на флюсо-медной подкладке и он бедняга, вот незадача, не может найти книгу или главу в книге с таким названием. Потом увидел ник автора ...
На вскидку , посмотрите например страницу 97 (Сварка и сварочные материалы т.2 Волченко В.Н.)
Книг то я много уже перелопатил))) Но на практике все гораздо сложнее получается! Вот по этому и спрашиваю "бывалых" в этой области.
-
Поделитесь опытом автоматической сварки под флюсом на флюсо-медной подкладке!!!!
Какие тонкости необходимо учесть при ведении данного процесса? Необходим ли зазор в стыке, какой диаметр проволоки, какой ток, напряжение, скорость сварки? В литерату ре очень расплывчато написано, интересен практический опыт!
P.S.: Варить необходимо сталь 09Г2С толщиной 3 и 4мм, а также нержавейку 12Х18Н10Т толщиной 3мм.
-
Возможно еще дело в шаговом двигателе, хотя его глюки обычно проявляются не системно.
А можете по подробнее про глюки шагового двигателя пояснить? Как обычно проявляются дефекты при его не исправности и что в нем (наиболее вероятно) может выйти из строя?
Вариант с температурой листа до резки интересный. Дело в том, что листы которые сегодня резали были завезены в цех с улицы и были холодные и влажные. Резку начали не дав им прогреться и просохнуть (план горит, что поделаешь). Буду наблюдать дальше что будет.
P.S.: 0,5мм на сторону - это не стабильно происходит. В ряде случаев листы с тыкуются без зазора. Бывают случаи (но редко), когда зазор по всей длине стыка переменный, т.е. кромка после резки не прямолинейная а кривая.
-
а в направлении перпендикулярном стыку подобные деформации есть?
В направлении перпендикулярном стыку таких деформаций нет! Диагональ тоже в норме. Такое явление наблюдается только в середине листа (как указано на рисунке выше).
кстати про перемычки верно подмечено, хотя наверняка отход минимальный, т.е особых бонусов от оставленных перемычек ожидать
Отход действительно минимальный (не более 10мм с каждой стороны). Перемычки более эффективны на толстолистовом металле, а в моем случае эффекта врятли удастся добиться. Кроме того, лишние врезания будут портить кромку детали, а этого допускать мне никак нельзя, так как перед сваркой лист никак не обрабатывается больше.
-
1
-
-
может попробовать резать листы на ванне с водой? тогда теплоотвод от места реза будет более быстрый.
На ванне с водой опробовать не удасться, так как стол у нас с вытяжкой, а установить на этот стол дополнительно ванну с водой будет проблематично. Слишком большая длина и ширина листов.
Может есть еще варианты? Возможно дело все-таки не в усадке? Уж слишком не равномерно она проявляется, а иногда совсем отсутствует.
-
1
-
-
Это происходит от нагрева металла.
А я грешил на механику портала. Сегодня (буквально 2ч. назад) зазор в стыке был больше 4мм. Пришлось подгнять болгаркой (стачивать края). Может подскажете как можно компенсировать линейное расширение?
-
Добрый день, форумчане!
Возникла проблема с получением прямолинейного реза листов на установке плазменной резки с ЧПУ Hyperterm. При резке стали 09Г2С и 12Х18Н10Т толщиной 3 и 4мм наблюдается "серповидность" на кромках. Режимы резки выставляю согласно инструкции по эксплуатации.
Режимы резки:
1. Для 09Г2С толщиной 4мм - Ток 130А; Скорость резки 5550мм/мин; Газ О2/Воздух
2. Для 12Х18Н10Т толщиной 3мм - Ток 80А; Скорость резки 2180мм/мин; Газ F5/N2Дело в том, что прямолинейность нам очень важна, т.к. листы после резки стыкуются под одностороннюю автоматическую сварку на флюсо-медной подкладке, и при таких зазорах в стыке получаются прожоги или вогнута наружная сторона шва.
Может кто-то сталкивался с такой проблемой? Будут интересны любые мысли.
Выбор производителя сварочной проволоки
в Расходные материалы
Опубликовано
Доброго времени суток, форумчане!
Возник вопрос выбора сварочной проволоки, аналога СВ-08Г2С, производства Кореи и Китая. Выбор стоит между Hyundai, Kiswel и Grovers. По характеристикам наплавленного вроде идентичны, по качеству пробных катушек тоже. А как в промышленных масштабах себя показывает? Кто пользуется проволоками данных марок, дайте свои отзывы.
Еще интересует реальное происхождение катанки, не на одном ли заводе все катают? У кого есть инфа, подскажите.