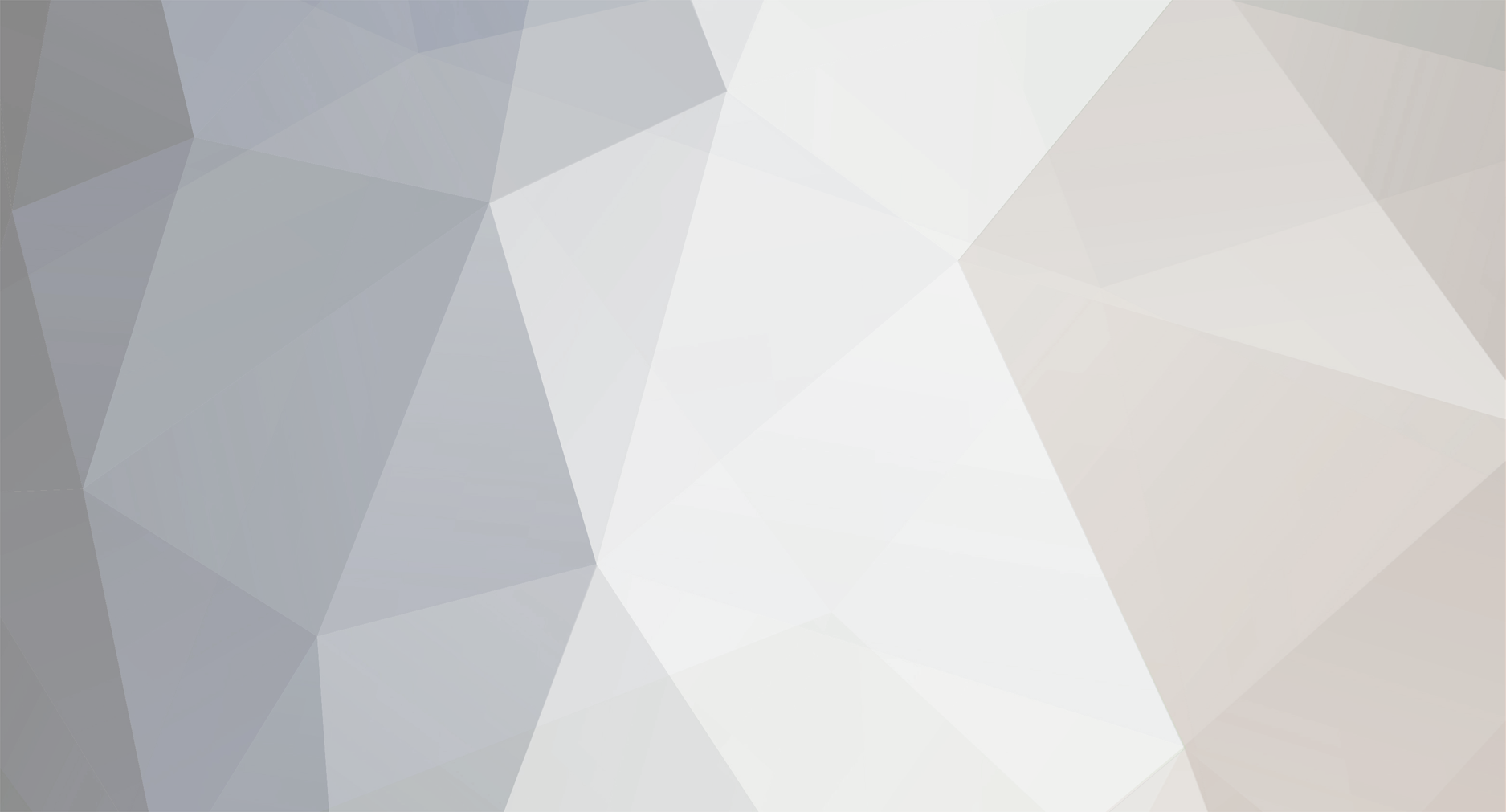
5SVR5
Участник-
Постов
134 -
Зарегистрирован
-
Посещение
Информация
-
Oткyдa Вы узнaли o проекте Вебсварка?
нашел в интернете
Посетители профиля
1 332 просмотра профиля
Достижения 5SVR5
-
Да горелка охлаждаемая, на кулере есть цифровое табло. Завтра посмотрю что оно показывает.
-
Здравствуйте! У меня на производстве используется плазменно-порошковая наплавка. При помощи неё наплавляем твердый сплав. В сварочную ванну порошок попадает через отверстие находящееся в аноде горелки Кастолин E52. Время от времени происходит забивание каналов расплавленным порошком. Не могу понять причин этого забивания, хотя сам процесс элементарный. Может быть кто из вас сталкивался с данным процессом, в чем причина забивания, можно ли его минимизировать, может быть существуют какие либо защитные средства. К сожалению в интернете информации по данной технологии немного.
-
Могли бы Вы мне сбросить схему вашего стенда, а то мы сделали из балластного реостата и получилась какая то шляпа. Что то мерит, что то нет. EWM вообще показывает ошибку.
-
Представьте если такого оборудования 40 шт, теоретически можно сварить на каждом КСС, тем самым аттестовав его, но это столько времени, денег, проблем, страшно даже представить. Если все оборудование прошло поверку, то аттестацию технологии можно провести на одном, а варить по этой технологии соответственно можно любом завалидированном оборудовании. Ведь в принципе НАКС, при аттестации оборудовании, делает то же самое. Только я не разу не видел, что бы они это делали в реальности, протоколы они не предоставляют, да и делают они это раз в 4-ре года. В ИСО 15614-1 п.8.4.8 указано следующее: "При наличии требований к ударной прочности верхний предел области распространения аттестации по погонной энергии устанавливается на 25% выше, чем при сварке образца". Т.е. в +25% чем в протоколе аттестации и ниже. Следовательно рабочие карты сварки надо оформлять с таким диапазоном режимов, что бы рассчитанная погонная энергия не выходила на пределы аттестации. Действительно, с автоматическими способами гораздо проще чем с ручными. Я разговаривал с человеком который работал за границей инженером по сварке на объектах которые строились для компании Chevron. На вопрос как они замеряют скорость ручных способов сварки и высчитывают после этого погонную энергию. Ответил, что при помощи линейки и секундомера. Да, Вы не поверите, но варят там сварщики по режимам указанным в картах. Если инспектор увидит, что режимы нарушаются, а находятся они на объекте постоянно и относятся к своим обязанностям с полной ответственностью, проблемы могут быть очень серьезными, вплоть до удаления всех сварных соединений которые выполнил данный сварщик. Что касается брака на производстве, допускать бракованные соединения это обман самих себя. С таким подходом к работе мы коммунизм не построим)))! Не которое время назад прочитал брошюру фирмы Voestalpine Böhler Welding по проведению калибровки оборудования. Они в ней написали, что шансы неправильных показаний при проведении калибровки современного инверторного оборудования их производства крайне низка, меньше 1%. Но они все же рекомендуют проводить его не менее чем 1 раз в год, при этом выявляя и другие недостатки, такие как поврежденная проводка, кабеля, разъемы и т.д. (что случается с гораздо большей вероятностью). Так же надо проверять оборудование после капитального ремонта и длительной работы оборудования в верхних пределах своих возможностей. Короче западная мать его культура производства и отношение к качеству (. В случае обнаружения несоответствий то, решением проблемы будет заниматься отдел промышленной электроники, они люди грамотные и образованные разберутся что надо делать. Если требуется привлечение сторонних организаций, то на оборудование которое в год производит продукции на миллионы ни каких денег не жалко.
-
По ИСО, в аттестации технологии, один из важнейших параметров сварки, если не самым важным, является погонная энергия, а это соответственно сила тока и напряжение. Аттестуя технологию сварки (WPS) определенного материала, т.е. добившись необходимых свойств, прежде всего механических, можно в дальнейшем оформить множество карт сварки, которые будут аттестованы, при условии того, что погонная энергия в них не выходит за пределы полученные при аттестации технологии. Если КСС при аттестации был сварен на одном оборудовании, то где гарантии, что остальное сварочное оборудование в производстве или же даже на другом предприятии, в случае сварки по аттестованной карте, действительно сваривает на тех режимах которые указаны в карте? Следовательно на одном оборудовании сварка будет хорошая, а на другом возможно нет. При проведении поверки можно понять как работает оборудование, в случае некорректной работы провести ремонт, откалибровав его, или же не использовать его при сварке ответственных конструкций. Следовательно, данный процесс можно завалидировать - т.е. оформить документы о проведении работ с полученным результатом, которые можно предоставить какой либо инспекции. С другой стороны, конечно, специализированное оборудование в сегодняшних условиях не приобретешь, так может быть его можно сделать самому, может быть там ничего сложного в конструкции нет?
-
Я конечно понимаю, что с обеспечением качества сварки у нас в стране беда, но все же я не верю, что так везде. Я где-то слышал, что при производстве оборудования для атомных станций что то похожее проводится. По поводу того, что нельзя откалибровать современное оборудование, то это неправда. Был участником калибровки оборудования Фрониус, к тому же у меня есть протокол калибровки на оборудовании Кемппи. Но они калибруют только собственное оборудование, а у меня в производстве полная солянка. В интернете я видел оборудование (только импортное), которое калибрую, судя по рекламе, любое оборудование и способы сварки. Просто я думаю, что может быть кто-то использует самопальное.
-
Добрый день! Коллеги кто нибудь из вас сталкивался с калибровкой сварочного оборудования? Надо проверить действительно ли правильные режимы сварки показывает оборудование при сварке, т.е. сравнить отображаемые значения с эталонным. Данные действия регламентируются ГОСТ Р ИСО 17662, а сам процесс калибровки описывается IEC-60974-14. Хотелось бы узнать как это делается у нас в стране, по каким документам и каким оборудованием.
-
Индекс A по ISO - классификация по пределу текучести Индекс B по ISO - классификация по пределу прочности Буква М идущая сразу после обозначения стандарта AWS на сварочные материалы указывает на использование в спецификации метрической системы измерений (написано в разделе область применения всех спецификаций AWS на сварочные материалы).
- 2 ответа
-
- 1
-
-
Коллеги добрый день! Читаю данный форум, очень много информации про электроды следующего характера: варят не варят, полярность, пространственное положение, провар, производитель и т.д. Но практически нет информации про легирование наплавленного металла. Попытаюсь описать свой вопрос на примере УОНИ 13/55. Стержень электрода проволока Св-08А, а механика сварного шва как у проволоки Св-08Г2С, ну или где-то рядом с этим. Очевидно, что выполняется легирование металла через обмазку электрода. Вопрос у меня в следующем – есть ли зависимость, что при изменении технологии сварки изменяется механика сварного шва, в частности увеличивается ударную вязкость. Например, при перегреве металла ударная вязкость будет ниже, следовательно этот параметр надо контролировать. Например, при сварке под легированным флюсом повышение напряжения сварочного тока приводит к увеличению легирования наплавленного металла, следовательно, изменяется свойство наплавленного металла. Влияет ли сила тока, полярность, пространственное положение, технология ведения электрода на механику сварного шва?
-
Мне нужно выполнить соединение за один проход при этом попасть в область распространения (по таблице QW-451.1) как по толщине основного металла Т , так и по толщине наплавленного металла t. У меня это получается образец толщиной 10 мм с конструктивным непроваром в 4 мм, аттестация подобных сварных швов допускается (описано в QW-202.2(. По таблице QW-451.1, для аттестации технологии я должен выполнить механические испытания, одним из которых является статический изгиб. Очевидно что, нецелесообразно проводить испытания на изгиб на лицевую и обратную сторону - разрушение будет как раз по этому непровару. Для толщины КСС 10 мм допускается проведение изгиба на боковую сторону. У меня вопрос, вообще по ASME возможно ли проведение испытания на статический изгиб образца имеющего конструктивный непровар? Спасибо за ответ!
-
Действительно Вы правы, я перепутал это с пунктом 7.5.1.2.4 API 6A "Основной металлический материал должен сохранять минимальные требования к механическим свойствам после термической обработки после сварки. Изготовитель должен указать методы для обеспечения этих требуемых механических свойств и протоколирования результатов в рамках PQR" - я так понимаю, что после ТО наплавленного КСС необходимо проверить механику основного металла? Если в ASME sec. IX восстановительная наплавка относится, к простой сварке, то мой случай в API 6A описывается в пункте 7.5.2? В API 6A есть пункт 7.2.2 есть следующее: "Сварку должны выполнять в соответствии с аттестованными процедурами аттестованные сварщики. Сварные изделия, не работающие под давлением, должны соответствовать требованиям изготовителя". Эти слова можно понять так, что я могу подобные сварные швы выполнять сварщиками аттестованными по НАКС? Как вообще быть с теми швами которые действительно не испытывают нагрузки, например "Маховик"?
-
Спасибо за ответы! Это пункт 7.3.4.3 В конечном итоге, изучая стандарт, я определился с КСС для аттестации. У меня это будет просто труба толщиной 30 мм с разделкой по центру, глубиной что бы я мог выполнить наплавку в 1 слой - это будет где-то 4 мм. Стандарт ASTM A370 регламентирует проведение испытаний на ударный изгиб образцами толщиной 2,5 мм и 3,3 мм. То есть испытания провести можно. В своей практике, в российских документах, встречал то, что допускается, если невозможно изготовить образцы, сварить КСС такого размера, что бы можно было изготовить образец необходимого размера. Наверное есть какие либо разъяснения комитетов по этому поводу, сомневаюсь, что этот вопрос возник только у меня. По возможности, мне бы хотелось, при возникновении данного вопроса, аудитору предоставить какое ни будь документальное подтверждение.
-
Еще один вопрос. В связи с тем, что ударная вязкость сварного шва является существенной переменной, то по QW-410.9 ASME ces. IX мне необходимо выполнить отдельно аттестацию однослойной сварки, а отдельно многослойной сварки. Так же выполняя требования API 6A, которые указывают, что если после сварки проводится ТО (в моем случае для снятия напряжений), то при аттестации технологии необходимо выполнить измерения твердости и ударной вязкости сварного шва (п.7.3.4.3) и околошовной зоны. API достаточно подробно разъяснят порядок проведения данных испытаний. Остальные испытания (растяжения, статический изгиб и т.д.), требуемые API 6A при аттестации технологии сварки, выполняются по ASME ces. IX. Мне не понятно следующее. При однослойной сварке толщина наплавленного металла t не будет превышать 3...4 мм. К тому же, в качестве КСС будет труба (мы выполняем сварку кольцевых швов). Как из такого КСС изготовить образцы на удар и твердость, и провести данные испытания? Может быть есть какие либо разъяснения по этому поводу?