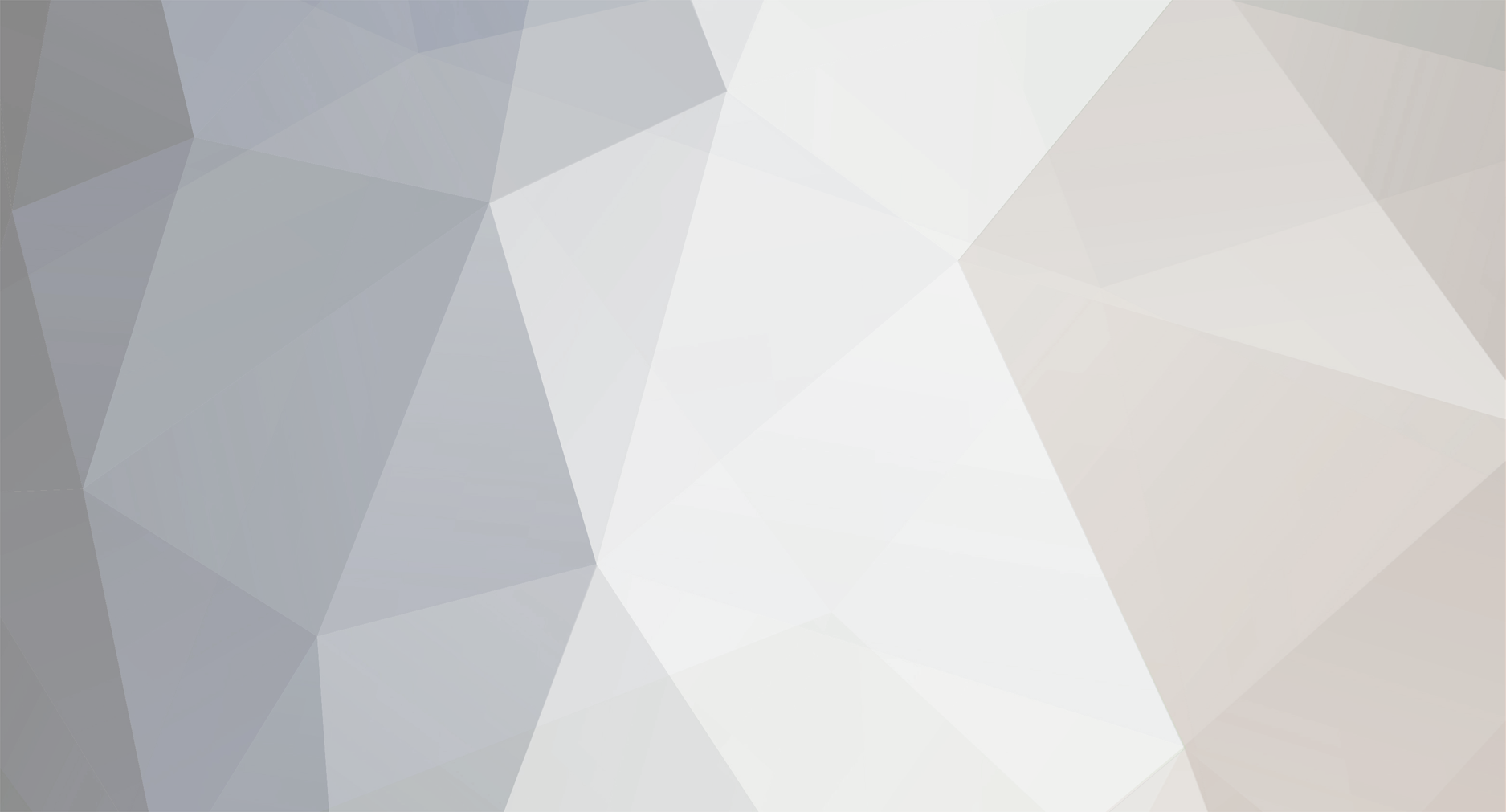
fav
Участник-
Постов
51 -
Зарегистрирован
-
Посещение
-
Победитель дней
2
Тип контента
Профили
Форумы
Блоги
Загрузки
События
Весь контент fav
-
Периодически работаем с титаном. Гибкий подув как мы кажется будет гораздо удобнее, чем используемые на данный момент медные сапожки. Так что больше личный интерес попробовать, но где купить еще не нашел.
-
Если зазор в ноль то понятно, а в случае с зазором 3-4 мм уходит и очень даже не хило. заглушки у нас всякие есть в том числе самодельные из резины, алюминия. Про малярный скотч были мысли, но боялся что гореть начнет?
-
Чтобы обеспечить качественный поддув (в том числе при прихватках) кто чем герметизирует стыки? иначе расход аргона особенно на больших диаметрах очень высок!
-
ух какие знакомы штуки! только мы из меди обычно делаем. тут увидел заводского изготовления, гибкие... а вот где купить не знаю (((
-
Ничего хитрого в распространении газов нет. Процесс формирования точки схожий, но имеет ряд особенностей и преимуществ. Про лазерную сварку совершенно отдельный разговор, там другое формирование шва, но при правильном подборе режима кратера там быть не должно если есть - то это дефект! Если есть желание можем обсудить это в "личке" или в отдельной теме про лазерную сварку. но лучше почитайте для начала литературу по лазерной сварке. Что это за разрушение такое "на вращение"? Где вас такому научили? А появление трещины это не просто опасная штука - это не допустимая ни в каких пределах штука! Если уж говорить о расчете на прочность и распределении напряжений касательно точечных сварных соединений, то работать оно может на срез/на отрыв. Если разрушать точку, то в расчет берут площадь этой точки. Если разрушение происходит по краю по окружности это не значит что оно несущее а остальная часть точки не работает,просто как и в случае со стыковым соединением эта зона наиболее ослаблена. Нет никакой гарантии что кратер в дальнейшем при работе не будет являться началом трещины которая дальнейшем, при нагрузке может раскрыться и дойти до основного металла.
-
а бывают случаи что ну совсем ни как не подлезть... тогда есть еще такой способ ))) ну и соответственно без всяких зеркал, загнутых электродов итп. p.s: только что разглядел это соединение на фото, которое выложил "АВН" в предыдущем сообщении (Фото0013)
-
Кратер как в случае протяженных швов так и в случае точечной сварки является концентратором напряжений, тем самым ослабляя шов.Плюс к тому усадочные рыхлости в дальнейшем могут привести к возникновению и развитию трещины. собственно поэтому кратер - всегда НЕ допустимый дефект! В случае точечной виг-сварке, данная точка будет ослаблена и при нагрузке по ней может пойти разрушение. У нас на предприятии все сварщики отключают функции заварки кратеров/нарастание/гашение итп и производят заварку вручную несколькими повторными зажиганиями на кратере, ну вот удобно им так.. не переучить уже))))
-
Если в Москве то позвони (495)518-25-29, (495)518-25-29, 8(926)111-24-45 Щицын Владислав Юрьевич. спецы заварят тебе плазмой - качество будет не сравнимое с аргоно-дуговой сваркой. Или в Перми можем заварить такой же плазмой. через грузовую компанию можно свозить туда-обратно.
-
Похоже все таки мои изначальные размышления были верными. Образование хрупкого мартенситного слоя происходит в обоих случаях как в случае сварки Cт3 с Cr-Ni сталью, так и в случае сварки Cт3 c Cr-Mn сталью. Так как уровень легирования металла снижается, приближаясь к Ст3. Похоже все дело в ширине этой зоны, которая как раз зависит во первых от режима сварки, а во вторых от запаса аустенитности металла шва (большой запас аустенитности позволяет снизить толщину малопластичных участков там самым повышая пластические свойства металла и снижая вероятность появления трещин). При перемешивании 12Х15Г9НД+св08Х20Н9Г7Т запас аустенитности у нас получается с сварном шве заметно меньше, чем в случае 12Х18Н10Т+св08Х20Н9Г7Т. Получается что если нужно сварить аустенитную сталь с перлитной лучше применять присадочный материал с высоким запасом аустенитности. Если все таки есть необходимость сварить 12Х15Г9НД+Ст3 лучше применять проволоку с содержанием никеля более 20%
-
При перепроверке химии выяснилось что материал не AISI 201, а 12Х18Н10Т (не из того материала подготовили образец). Были сварены повторные образцы Ст3+AISI 201. результат следующий: 1. По результатам определения химического состава установлено, что материал коррозионно-стойкого листа 2 КСС соответствует нержавеющей холоднокатаной стали 201 по американскому стандарту AISI (American Iron and Steel Institute), аналогичной российской коррозионно-стойкой стали 12Х15Г9НД по ТУ РМО-005/08. 2. Образцы КСС листов 2 (Ст3+AISI 201) не выдержали испытания на статический изгиб. При изгибе образцов на угол 100гр через оправку ? 4,0 мм, по месту сплавления бывшей жидкой ванны с материалом листа из углеродистой конструкционной стали типа Ст3 были обнаружены множественные надрывы и трещины длиной более 5 мм. Надеюсь кому-то пригодится.
-
Все зависит от полуавтомата. если хороший инвертор с импульсным режимом то шансы на успех очень высоки. А так есть известные технологии EWM-Coldarc, GMA-пайка от ESAB. где современные аппараты с микропроцессорным управлением делают этот процесс довольно простым. В свое время работал в региональном представительстве ESAB была возможность по-баловаться этим. Сам не пробовал, но в теории шансы на успех есть. сейчас к сожалению не где попробовать. не попадается оцинковка по работе ни где (((
-
Я считаю что наиболее удачный способ - миг-пайка. но можно попробовать заварить аргоном на переменном токе, на малых токах, держав дугу на присадке - присадку я бы попробовал чистый цинк (у него температура плавления будет чуть ниже чем у сплава).
-
если что вспомню напишу, пока ничего в голову не приходит. вроде все как по учебнику, если рассмотреть касательно сборки под сварку то: зазор между свариваемыми кромками максимально допустимый по ГОСТу. Зазор может стянуть либо в процессе сварки, либо при постановке прихваток. При стягивании зазора можно восстановить зазор с помощью шлифовальной машинки с отрезным кругом нужной толщины. Прихватки лучше располагать по возможности таким образом, чтобы сварщику было удобно дойти от прихватки до прихватки без отрыва. Если длинная прихватка - можно по краям сделать запилы шлифмашинкой чтобы снизить вероятность дефекта. см. внимательно пост №9 ))) соединение С17 уже говорит о том какая разделка, и о том что подкладка отсутствует. что у сварщика не получилось - не было качественного формирования корня шва (превышение корня шва, непровар, вогнутость корня с подрезом - все разом на 2-х пробных катушках). материал 12Х18Н10Т присадка св06Х19Н9Т.
-
Моё удивление было не меньше. Поэтому я и написал что сварка толстой нержавейки сильно отличается от сварки тонкой. Данный сварщик несколько лет варил только трубы типа с ф12 по ф89 (стенка до 4мм) при том собирали всегда без зазора и легко продавливали корень. Собрав без зазора ф168х10 ничего хоршего у него не получилось ))) Не зря сварщиков учим на каждый диапазон диаметров и толщин отдельно.
-
Согласен выгорание происходит! Но если плавить непосредственно присадку то выгорание лигатуры будет в ней? а шов будет на 80% состоять как раз из этой присадки Чтобы снизить выгорания лигатуры обычно не допускают сильного разогрева детали и не применяют форсированные режимы.
-
разделка С17 как на ф57 так и на ф168. В случае с 57-ой трубой 2 прохода, первый без присадки, без зазора в стыке - отлично выходит проплав. В случае в 168х10 (поворотный стык, 3 прохода) даже при минимальном притуплении без зазора - качественное формирование корня очень не простая задача.
-
Были выполнены образцы Ст3+AISI 201 сваренный Св-08Х20Н9Г7Т и Ст3+AISI 201 сваренный ER309L Результатам испытаний: проволока и материал соответствует сертификату. при статическом изгибе более 120 градусов трещины отсутствуют на обоих образцах. Почему же все таки появлялись трещины на сборках? до сих пор не понимание...
-
Добавлю не много из своего опыта: может где-то обсуждалось на форуме, но если честно я первый раз слыщу. По моему опыту в частности при корневом проходе дуга направляется прямо на зазор, а присадка подается чуть сбоку на кромку разделки, где расплавляется и стекает в ванну. если взять в частности трубопроводы то да. трубы типа ф57х3.5 и менее отлично варятся без зазора, но вот в ситуации с трубой 168х10 врятли такой трюк у Вас выйдет. Не так давно опытнейшему аргонщику (который десятки лет уже варит трубы) объяснял как сварить 168х10, потому что привычными ему способами без зазора у него ничего не получалось. Объяснил как обеспечить проплав корня с зазором, ориентироваться по "замочной скважине" и вот уже 1-ая партия трубопроводов прошла рентген 100% просто отлично! еще есть хороший вариант - "не выводить кончик присадки из зоны защиты до полного остывания"
-
во время учебы в магистратуре очень тесно занимался плазменной сваркой. Во время работ проведенных на кафедре были получены положительные результаты сварки Д16 плазмой проникающей дугой. плазменная сварка Ал сплавов. Оборудование для плазменной сварки - разработка кафедры.
-
to "blazen79" - образцами в ближайшее время займусь... С этим я не согласен, сварщик - не автомат. Каждый варит на своих режимах и соответственно с разным тепловложением. проволока св08Х20Н9Г7Т, по сути то же что и Е309МоL. только чуть меньшее содержание молибдена компенсируется титаном, а меньшее количество никеля марганцем. хотя может я тут и ошибаюсь т.к никель влияет на пластические свойства положительно, а марганец отрицательно. И в каком это документе регламентируется? варим трубы высокого давления из нержавейки для газпрома тоннами, первый раз такое слышу. Если есть возможность поворачивать - кто будет варить неповортный стык???
-
Добрый день. не так давно решили существенно сэкономить и вместо привычной 12Х18Н10Т во многих случаях стали заменять 12Х15Г9НД (AISI201). При сварке AISI201+AISI201 проволокой св08Х20Н9Г7Т все отлично. В случае замены где полоса из AISI201 приваривается к квадратной трубе из Ст3 прерывистым швом - начались проблемы. На внешний взгляд все хорошо,а при кантовании сборки процентов 5%швов покрывалось трещинами. Сейчас уже приходят рекламации со станций. Стал разбираться с этим, по диаграмме шеффлера просчитал эквивалент Cr-Ni получается при сочетании СТ3+AISI201+св08Х20Н9Г7Т при различной степени перемешивания структура шва может попадать на зону Аустенит-Мартенсит, что в последствии при динамических нагрузках дает трещины. т.е все зависит от сварщика? жесткий режим - сильное перемешивание - дальнейшие трещины, мягкий режим - минимальное перемешивание - трещин нет. Верно ли я размышляю? Есть ли у кого-то мысли по этому поводу? А то уже всю голову себе сломал как уйти от этой проблемы.
-
опыта сварки биметаллов у меня не было, но вот на сколько я видел - для защиты от коррозии в результате образования гальвано-пары (в частности при сочетании нержавеющих материалов и алюминия) применяют цинковые аноды. В результате коррозия проходит по аноду, и его со временем заменяют на новый
-
Мы у себя на предприятии регулярно варим подобные фланцы. прижатие к плите обеспечивает хорошее охлаждение и снижает деформации. Разделку применяем С15 т.к С16 это слишком сложно - детали надо ставить на станок для снятия фаски. а тут сдул газом или плазмой, подровнял болгаркой и в работу. P.S: применять одностороную разделку если честно даже в мыслях не было )))) но думаю что при этом части фланца будет приподнимать от плиты вместе с прижимами. хотя, смотря какой шов про длине.
-
Вариант конечно безусловно интереснее. Но если "считать деньги", то выше приведенный вариант на 8-9 тыс выйдет дороже )))))
-
Вариантов тут не много. Посмотри "ПДГ-351" вполне неплохо справляется со своей задачей... цена в районе 50-60 тыс руб.