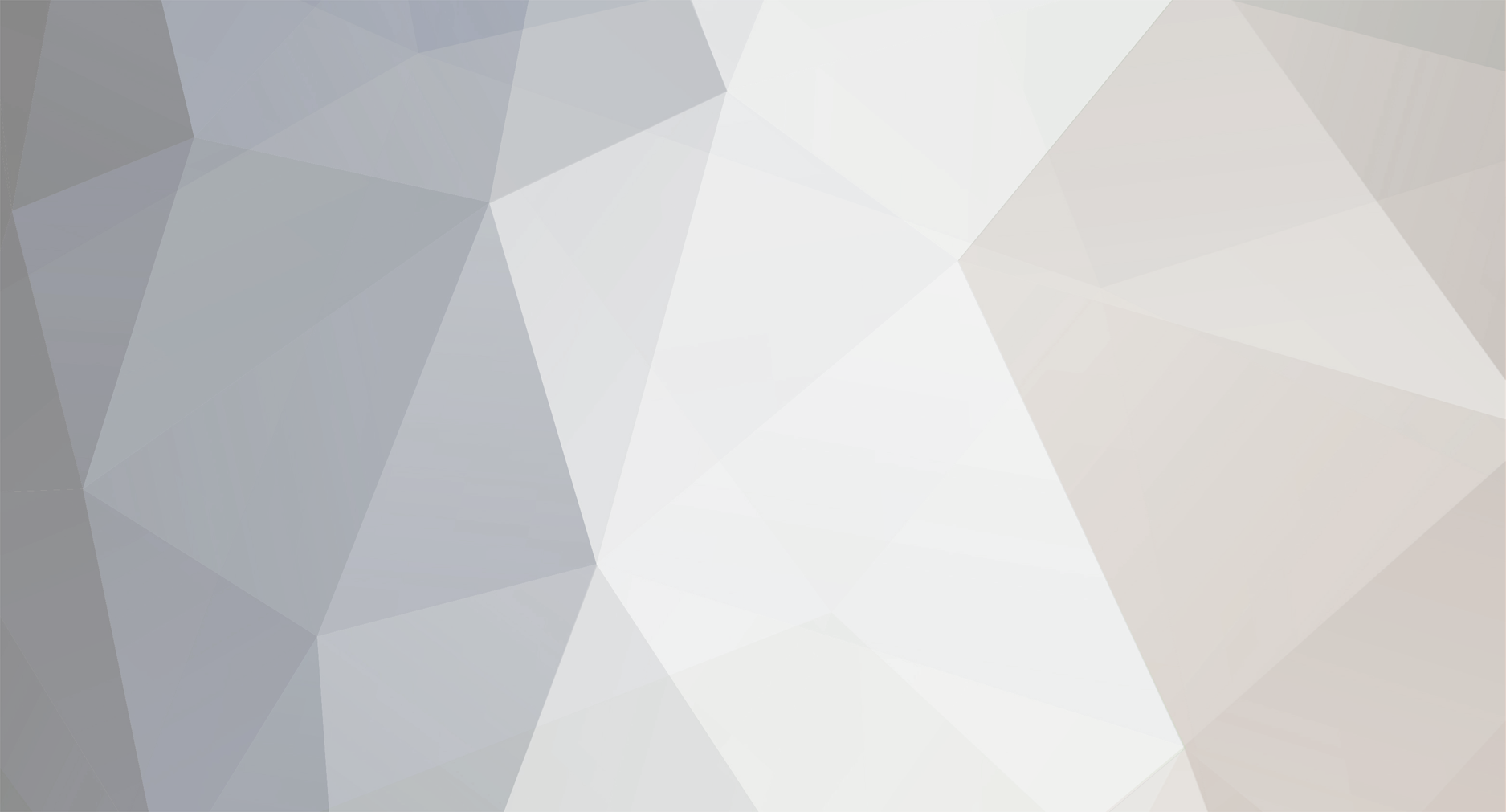
Legem
-
Постов
25 -
Зарегистрирован
-
Посещение
Тип контента
Профили
Форумы
Блоги
Загрузки
События
Сообщения, опубликованные Legem
-
-
Я вам дал минимум 2 совета для решения проблемы и з своего опыта:
1. подготовить планки так же, как и основной шов (если не понятно, в вашем учебнике это называется "разрезная планка" см.рис.148)
2. аттестовать технологию у знающих людей (организаций), а не у халявщиков.
Вы, как ответсвенный имееете право требовать внеочередную аттестацию на основаннии повторяющегося брака. Только не требуйте пункта из правил, он есть, но работайте сами.
3. третий совет, тоже был ранее - проконсультируйтесь для начала у тех, кто выдал протокол аттесации технологи, в которой ничего несказано о подготовке планок.
Уважаемый keria, мне интересен шов, которым приваривается технологическая планка к торцам свариваемых листов - должен он быть с полным проваром или нет, и если да, то на какой документ/литературу можно сослаться. Вот, собственно, и весь вопрос. В любом случае, спасибо вам за ответ!
-
Yt cjНе собираюсь ничего доказывать. Незнание закона не освобождает от ответсвенности.
PS Посмотрите в свою книжку, которую вы тут опубликовали. Там на картинке все нарисовано, во всяком случае разделка.
Извините, но ваша позиция вызывает недоумение. Вы утверждаете одно, но не можете подтвердить это ничем; выходит, ваши утверждения голословны. Я создал эту тему для реального решения производственной проблемы - вы же отказываетесь делиться своим опытом ("Не собираюсь ничего доказывать. Незнание закона не освобождает от ответсвенности."), в таком случае, зачем вы вообще сюда пишете? То, что мы на производстве делаем что-то не так, и ежу понятно. Если вам нечего сказать что-то конкретное по решению озвученной проблемы, не пишите, пожалуйста.
-
Планки свариваются абсолютно идентично основному шву, вплоть до формы разделки, зазоров и конструктивных размеров. И металл для планок берут новый со склада, кстати, а не в утиле. И зачищают, обезжириваюют, подогревают и т.п. абсолютно идентично. Если дефект вылезает на планке, весь шов бракуют. Какая на... статистика, какой разговор о неолном проваре, какие упоминания о проявлениях дефектов!? Как (кто) вам технологию аттестовал? Я в шоке.
Уважаемый, такие вещи не прописываются в технологии сварки. Если хотите доказать обратное, приведите, пожалуйста, пример нормативного документа, где упоминалась бы технология приварки таких планок, или пример аттестованной технологии сварки, где упоминалась бы обсуждаемая тема, или хотя бы ссылку на техническую литературу / учебник, где описывалась бы указываемая проблема (за исключением той, что я уже привел в посте №3).
-
может, что откопаете полезного, черкните пару строк.
обязательно!
-
так не понятен срок хранения. Я не знаю все и вся. Я исхожу из опыта предприятий. У каждого своя специфика. Поэтому я подразумеваю под словом хранение - продолжительный срок. Хотя бы неделю или может да же месяц.
Я думаю, что кто продает флюс у них должна быть рекомендация по хранению их товара. И так же емкости для хранения же использованного товара или ... В общем я описал основное, что видел. А уж в тонкости не нырял, нет надобности. Да и прогресс не стоит на месте
Я понял, спасибо большое=) У производителей флюса в основном идут рекомендации по температуре прокалки, у ESAB есть еще рекомендация хранить флюсы их производства при "150 +/-25°С".
-
А вот тута попоадробнее пожалуйста! Аттестовальщикам и нужно бы задать вопрос, почему это трещины идуть по аттестованным технологиям? В технололоигиях такие вещи четко прописываются. Будь я ответсвенный за ето дело потребовал бы внеочередную аттестацию технологии, имею полное право. Только не наступал бы на одни грабли второй раз. Канторку посолиднее поискал бы.
Да, вы правы, в типовой технологическом процессе (приложении к свидетельству об аттестации технологии) действительно нет данных о возможности появления таких дефектов и о мерах по предотвращению такой ситуации. Я в этой теме хотел бы узнать о предотвращении описанной проблемы на практике. Пока все указывает на то, что данные дефекты появляются из-за плохо сваренных тех. планок. Сейчас пока собираю статистику, в ближайшее время можно будет уже сказать, приведет ли сварка с полным проваром технологических планок к предотвращению дефектов.
-
не видел в вашем первом сообщении этого.
использовать две печи, одна для ночной смены, вторая для дневной.
Герметичные ... это громко сказано. Конечно полная герметизация не нужна. Иначе горячий флюс остывая стянет бочку
. Бочка (емкости) нужны такие, чтобы с крышками были и по минимуму пропускали окружающий воздух. Т.е. не было свободного сообщения с окружающим воздухом, чтобы влагу флюс не набирал.
Поэтому любую подходящую бочку можно использовать (выше постом вам фото показали, пост №11), лишь бы крышка была и как можно плотнее. Ведь и флюс пока вы варите, насыпаете, он в открытом состоянии. Влагу моментально (критичную для сварки) он не сразу набирает. После печи у людей есть масса времени на использование. И хранение нужно в теплом помещении организовать.
И у флюса есть большой гемор - его производство. Качество плавает. И как не просушивай, у плохого всегда будут проблемы.
Да, насчет того, что при герметизации стянет бочку за счет остывания флюса - согласен
бочку для хранения можно закрывать уже после того, как флюс остынет. Герметичность все-таки нужна, этого требует и нормативка : "флюсы после прокалки следует хранить в закрытых мешках из водонепроницаемой ткани (полиэтиленовой пленки) или в закрытой таре с крышкой с резиновым уплотнением, или в сушильных шкафах (печах) при температуре 80 ± 20 °С, или в сухих помещениях (кладовых) при температуре не ниже 15 °С и относительной влажности воздуха не более 50 %" (РД 34.10.124-94 Инструкция по подготовке и хранению сварочных материалов). Насчет производства флюса также согласен - стараемся пользоваться флюсами от ESAB, поскольку от флюса производства России (как не прискорбно) или Китая бывает много проблем.
-
1
-
-
а зачем так сложно?
Обычно: днем нагревают печь или с утра. Туда закладывают флюс. К вечеру флюс прокален. Печь выключают и она остывает ВМЕСТЕ с флюсом. К утру температура вменяемая для работы. Далее забирают флюс из печи и начинают работать. В это время делают закладку новой партии. И так до бесконечности, по кругу. В понедельник берется старый запас из герметичного бака. Герметичный бак поставляется либо производителем оборудования либо поставщиком флюса. Часто сушилка флюса сразу же поставляется производителем оборудования.
Спасибо за ответ! Сложность в том, что работают 2 смены, дневная и ночная, флюса используется много, и требуется разработать процедуру прокалки и использования в цеху флюса согласно нормативно-технических документов. Ваш вариант хороший, но не учитывается, что работа идет круглосуточно без выходных. И насчет герметичного бака тоже очень хотелось бы увидеть, как он выглядит, потому что даже такой "простой" информации нет.
-
бидоны сильно шикарно. Такие бачки поискать
Спасибо большое! А из-под чего такие бачки? И какой у них объем?
-
Вы не выложили не одного фото, задаёте вопросы
я лично рассуждаю чисто логически из той информации которую прочитал..
Фото чего мне надо выложить? Флюса? В интернете этого добра предостаточно, наш флюс ничем не отличается от других. Ваши рассуждения вполне логичны, но извините, мне нужны вполне конкретные ссылки на нормативные документы, и интересен также обмен опытом по практической организации всего того, что я указал в своем сообщении. Если бы в инструкциях на флюс и на сварочные аппараты была вся информация, которую я здесь запрашиваю, я не стал бы поднимать такую тему. Флюс у нас идет, как правило, от фирмы ESAB. В инструкциях к нему написано буквально, что прокаливать его надо в течении 2 часов при температуре 300 °C. И больше ничего. Частично информацию по хранению и подготовке флюса я нашел в различных нормативных документах, типа РД 26-17-049-85 "Организация хранения, подготовки и контроля сварочных материалов", РД 34.10.124-94 "Инструкция по подготовке и хранению сварочных материалов", и во многих других нормативных документах кое-что прописывается. В этой теме я поднял вопросы, которые не прописываются нигде, и я хотел бы узнать, в принципе существуют ли такие документы, где все это будет указано. По сварочным аппаратам точно такая же ситуация. Если нет никаких нормативных документов, то очень хотелось бы узнать, как все это происходит на практике. Все наши сварочные аппараты аттестованы, сварочные материалы и сварщики тоже аттестованы, есть аттестованная технология и наша продукция лицензирована. Но по поводу таких "мелочей", которые на самом деле не мелочи, информации нигде нет. Если вы работали со сваркой под флюсом, то расскажите, пожалуйста, как у вас был организован процесс прокалки и очистки флюса, если нет - я не вижу смысла во всех этих рассуждениях. Извините, привык выражать свои мысли достаточно прямо, ни в коем случае не хочу обидеть или задеть.
Спасибо! Это уже ближе к делу.
-
Обычные бидоны(алюминиевые) и туда засыпайте прокаленный флюс и складируйте
Как выглядят эти бидоны?
-
вот так вот?
Да, это сварка кольцевых швов, у нас варят еще и продольные
Что мешает прокалить при первой засыпке в печь при 350 градусах,а затем держать температуру(Ну к примеру 80 градусов)Регулировок нет ?В одной печи можно прокаливать,а в других хранить.На сколько я понимаю прокалка это не постоянное хранениеРегулировки есть, я писал, что температуру эти печи держат очень хорошо, и флюс не остывает в течение 4-5 часов. В цеху стоит 3 печи, объем производства большой, прокаливаем во всех печах одновременно.
вопрос изделие сваривается температурой флюса или всё таки сварочной проволокой и силой токане понял, что вы имеете ввиду.
а надо ли флюс горячий перемешивать с холодным(может даже не прокаленным флюсом), может дать возможность ему остытья писал про это. сварщику нужно сделать план, надо сварить как можно больше изделий, но если он засыпет горячий флюс в сварочный трактор,то просто сожжет его. поэтому он идет на нарушение технологии и процедуры прокалки флюса и смешивает его с холодным флюсом. Либо есть второй вариант - ждать, пока остынет флюс и потерять на этом час времени.
стоит ли прокаливать флюса больше чем требуется на одну смену( часть флюса на прокалке, часть на остывании, часть готовая для сварщиков, и то что находиться у сварщиков) своего рода не большой конвейерработа ведется 24 часа в сутки, 2 смены работают. И опять же, где сварщикам хранить прокаленный флюс?
думаю производитель флюса, должен был указать основные вопросы на упаковке, температуру, время остывания, ну и ...если бы производитель указывал такие данные, я бы не стал поднимать на этом форуме такие вопросы.
если проводить аналогию, между флюсом и электродами, и представить что электроды после прокалки 300-350 градусов отдать в работу сварщикам, то рукавицы и держаки тоже не выдержат думаю производитель сварочного оборудования оборудовал бы короба для флюса спецподогревателями, если были выдвинуты такие требования к флюсу какими бы документамимы все же говорим о флюсе, а не об электродах. с электродами ситуация несколько иная.
если флюс порошком(имеет первоначальный вид) то годен к повторному использованию, если спёкся думаю приравнивается к шлаку очистить очень просто, сито от спёкшегося и магнит от металлической составляющей пылиЭто регламентируется в каких-нибудь нормативных документах?
-
1
-
-
Приветствую всех! На производстве активно используем флюс для автоматической сварки. Флюс (в качестве примера возьмем АН-348А) прокаливаем в специально закупленных для этой цели печах. В процессе производства столкнулись со следующими проблемами:
1. Сварщики берут флюс из печки прямо после прокалки. Температура флюса в этот момент около 300-350 °C. Такой температуры не выдерживают флюсовые бункеры-бачки на сварочных аппаратах некоторых фирм-производителей и некоторые другие составные части сварочного оборудования. Чтобы уйти от этой ситуации, сварщик либо смешивает горячий флюс в ведре с холодным непрокаленным, либо ждет от 30 до 60 минут, пока температура флюса в ведре не станет приемлемой. Оба варианта, разумеется, не устраивают никого, так мы либо портим оборудование, либо слишком много теряем времени. Температура флюса в печи остается на уровне 250-300 °C в течении 4-5 часов с момента завершения прокалки (хорошая теплоизоляция у печи).
Самым адекватным выходом из положения в этом случае видится создание участка подготовки сварочных материалов, на котором будет происходить прокалка флюса и последующая выдача в цех этого флюса. На этом этапе возникает вопрос:
2. В чем перемещать прокаленный флюс? Есть ли готовые решения или надо будет разрабатывать самому. Участок подготовки, если он и будет создан, будет находится в том же цеху, где происходит сварка.
3. В чем хранить прокаленный флюс? Нормативные документы предусматривают "герметичную тару". Как она выглядит, где ее можно приобрести в случае надобности? Можно ли обойтись без сушильных шкафов, где постоянно поддерживается определенная температура?
4. Регламентируется ли нормативными документами процесс прокалки флюса? Имеется ввиду, температура печи, при которой должен быть засыпан флюс, время выдержки, время остывания флюса? Как все это выглядит на практике?
5. Регламентируется ли нормативными документами температура флюса , при которой его можно вводить в работу? Имеется ввиду, условно говоря, "не менее 30 °C и не более 100 °C".
6. Регламентируется ли нормативными документами действия с отработанным флюсом - что с ним следует делать, как много раз можно повторно использовать, как очищать от загрязнений, как определить, пора флюс очищать или нет, и, самое главное, как это все выглядит на практике? потому как на бумаге все написано красиво, а на деле всю эту процедуру затруднительно привести в действие.
Буду очень благодарен за ответы.
-
Всё смотреть лень , но частично есть информация , подскажите только куда можно скинуть ? Всё разом скинуть не смогу , интернет у меня дороговат.
Здравствуйте! скиньте, пожалуйста, на [email protected] по возможности все, что имеется из этого списка
-
Legem, не грамм, а градусов
ок, спасибо!
-
Поищите на авито муфельную печку под ваши задачи. Они я точно знаю бывают и по 1700гр.
1700 гр флюса - маловато будет...объемы производства требуют большего
Спасибо!
-
И что же они говорят про то как их приваривали раньше? Завод же выпускал раньше продукцию?
У нас постоянный поток увольняющихся / новых сварщиков, действительно грамотных сварщиков практически нет. Информацию по крупицам приходится собирать.
насчет планок, опять приходим к тому, из чего они изготовлены и свойства и качество материала + проволоки.Планки делаются из листа той же марки стали и толщины, что и свариваемые листы, варятся теми же сварочными материалами, что и прихватки и технологический шов.
Кстати еще не мало важное, подготовка кромой, поверхности сопрягаемой. Ее после плазмы без зачистки или каким методом подготовка истов происходит? Азотированный слой как минимум зачищать надо.Торцы планок и свариваемых кромок чистят после обрезки плазмой/газорезкой.
Как вы переворачиваете т.н. карту после сварки первого шва? Может трещины зарождаются именно в момент кантования карты?Обратите внимание на глубину залегания трещины, где она зарождается и в каком шве распространяется.Интересный момент, заострю внимание на этом, спасибо
-
Приветствую всех! На производство требуется печь для прокалки флюсов ФЦ-17 и ОФ-6. Особенность этих флюсов том, что ФЦ-17 рекомендуется прокаливать при 650 °C, а ОФ-6 - при 900 °C. У кого-нибудь есть информация, где можно раздобыть такие печки? Или только самим делать?
-
Если я правильно понял, то создается обечайка с двумя продольными швами. Надо заметить где и когда образуются трещины:
- только на 1-м шве, который затем деформируется (для этого нужно сделать УЗК до вальцовки) или на обоих,
- возле входной или выходной планки.
После этой информации будем рассуждать.
создается обечайка с одним - четырьмя (!) продольными швами, в зависимости от диаметра. и дефекты в основном идут на швах, сваренных в "плоском" состоянии. Насчет места - после входной или перед выходной планок - согласен, надо уточнять, чем и собираюсь заняться, так же как и определением, в какой момент времени появляются трещины - до вальцовки или после
Честно говоря, я бы попробовал скорость уменьшить сварки. Так сказать увеличить время на прогрев детали. Конечно ток немного надо будет снизить. Но не будет резкого перепада температуры.
И трещины бывают всегда или например когда только холодно? Т.е. если в цеху летом жарко, то трещины присутствуют?
Трещины идут в основном на толстом металле, насчет температуры в цеху - сказать точно не могу, влияют ли она на наличие трещин, так как не застал "теплого" периода. Местные работники утверждают, что брак напрямую связан с неправильной приваркой технологических планок, и что температура мало влияет на этот процесс (разумеется, есть речь идет не о минусовых температурах)
двухсторонний провар - рвёт в основном 14 мм
вопрос 8мм прогреваются сильнее
16 мм прогреваются меньше (или остывают- хороший радиатор,ну условно)
14 мм средина зона прогрева и скорость остывания где то пересекаются, возникает напряжение,
в средине деталь сломать сложнее(лист бумаги вы рвёте всегда с краю), слабое место край
надо играть силой тока, скоростью остывания,
и может такой вариант
- зазор изменить
- на концах по 50-100 мм снимать кромку, корень шва , прогрев, ну всё как по простому
- если изменить технологию сварки без технологических планок, сперва обечайки, а потом продольный шов, исчезает слово край "слабое место"
Без технологических планок варить не будем - начальные и конечные участки шва в любом случае должны быть выведены на планки (чтобы потом не исправлять кратеры, непровары и другие дефекты, свойственные для этих участков)
В крайнем случае, если дело действительно не в планках, будем греть металл перед сваркой. Можно будет попробовать делать разделку кромок на указанных концевых участках, но это довольно трудозатратно и с геометрией шва проблемы будут.
-
вопрос - трещин больше в начале шва или в конце
Трещины бывают и в начале, и в конце шва. Точнее сказать пока не могу, надо выяснить.
трещины находятся в том месте где были прихватки на основном изделии, или в разных местахпосле прихватки кромок варится технологический шов по всей длине свариваемых кромок. Трещины находятся ориентировочно в 5-60 мм от торцов листов, протяженность в среднем от 20 до 120 мм
чем выполняются прихватки ММА, МИГ, материалприхватки и технологический шов выполняются полуавтоматом в среде активных газов (82% Ar-18% СО2), проволока - ESAB Ok Autrod 12.22 диаметром 1,2 мм или аналог проволоки Св-08Г2С (не помню точно марку, иностранный аналог)
соответствует ли материал прихваток - сварочному основному материалусоответствует
это уже пройденные вопросы, и дело даже не в режимах автоматической сварки, иначе в брак шли бы все швы по всей длине. Остается только заострить внимание на сварке технологических планок (из-за непосредственной близости трещин к ним) и на порядок наложения швов при автоматической сварки - надо ли менять направление сварки при выполнении второго слоя двустороннего шва для уменьшения сварочных деформаций, и, возможно, ухода от трещин?
-
Так же важное место отводится под флюс
Используем в основном флюс Esab OK Flux 10.71, в печке прокаливаем при необходимых режимах.
возможно пластины чуть длиннее надо использовать, чтобы успеть прогреть соседнюю областьПластины длиной до 250 мм, ширина 120-150 мм, шов начинаем варить практически с самого начала пластины
А в цеху холодно?В цеху холодно, но температура не опускается ниже 8-10°C
О данном вопросе прочитал в книге, приводится ее решение - приваривать планки с полным проваром. Есть еще несколько источников, где сообщается о такой проблеме и о схожем решении ее.
Особенность вопроса в том, что трещины идут в основном на "картах" - то есть когда плоский лист варится к листу. На замыкающем шве, который заваривается после вальцовки (то есть когда варим продольный шов обечайки), таких проблем нет.
-
Приветствую всех! На производстве столкнулись со следующей проблемой: варим листы двусторонними швами типа С29 по ГОСТ 8713 автоматической сваркой под флюсом. Начало и конец шва выводятся на выводные технологические планки. Толщина свариваемого металла от 8 до 16 мм, материал - Ст20, Ст3сп, 09Г2С ("черный"). После сварки планки отрезаются, листы вальцуются в обечайку и варится еще один шов по той же технологии. Проводим контроль сваренных стыков УЗК - и очень часто, особенно на толщине от 14 мм, выявляются трещины на участках, недалеко находящихся от краев листа. Может ли неправильная приварка технологической планки быть причиной возникновения трещин, и если да, то как правильно приваривать эти планки (нужен ли полный провар между планками и свариваемым листом). Планки используем из той же стали, что и свариваемыми листы, и той же толщины, что и свариваемые листы; планки идут сплошные.
-
@Legem, вам необходим сварочный подшипник, цен только от 30 тыс начинается. как выход самодельный бронзовая втулка и щетки (как их рассчитывать понятия не имею) если не вращается деталь топ просто через клемму - болтовое крепление
Не подскажете, где такие сварочные подшипники можно приобрести?
Не найдёте. Используйте то что вам советует Павел, только в количестве не менее 4 штук. По 250 ампер на струбцинку это ещё терпимо, греться будут, конечно, но уже не так сильно, и по площади контакта кабеля с зажимами сильно выиграете.
Спасибо за ответы!
-
Приветствую всех! На производстве столкнулись с проблемой сильного нагрева струбцин, которые прикрепляют провода от источника питания сварочной дуги к свариваемому изделию ("массы"). Сами струбцины изготовлены из обычной низколегированной стали ("черной"), типа стали 20. Появилось предложение заменить эти струбцины на медные. В связи с этим вопрос: кто-нибудь сталкивался с выбором таких струбцин, и может ли кто-нибудь помочь в выборе фирмы-изготовителя, с учетом того, что на производстве используются сварочные токи вплоть до 900-1000 А и такие струбцины должны иметь возможность вращаться?
Выводные технологические планки при автоматической сварке под флюсом
в Технологии и документации
Опубликовано
Уважаемый keria, все же у меня сложилось стойкое впечатление, что вы не поняли суть проблемы, описанной мной. В приведенной мной странице из книги вполне внятно описано решение моей проблемы, и я хотел уточнить, есть ли еще в литературе / нормативной документации / чьем-либо жизненном опыте подобные отсылки к решению проблемы. Ну да ладно. По поводу того, как срезать планку, вопроса я и не задавал, но все равно спасибо за уточнение. Мне был интересен момент именно по приварке пластины к листу.